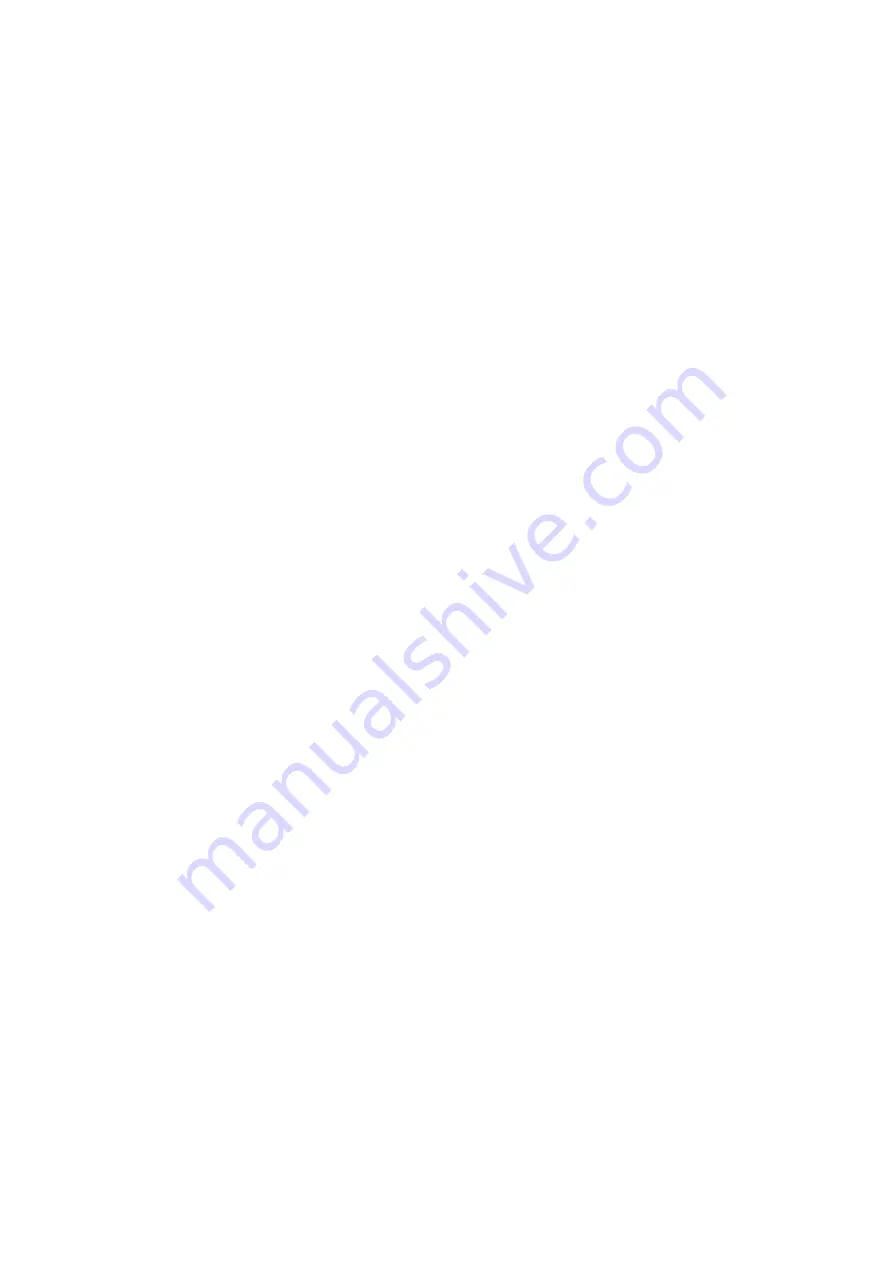
Lmic Operator Guidance:
Background
information to effective acoustic leak detection
All acoustic leak detection methods are based on the
premise that normal water passage through pipelines
takes place noiselessly. When the water passage is
disturbed a noise is created. Causes can include par-
tial pipe blockages, sudden changes in pipe diameter,
abrupt changes in pipe direction, pumps or meters in-
stalled in the pipeline, consumer usage or pipeline
damage. Pipeline damage can include holes, cracks or
splits, complete pipeline rupture, leaking joints or leak-
ing valves.
Careful application of leak detection techniques will
enable the operator to eliminate detected noises gen-
erated by poor pipeline design or consumer usage and
to identify leakage due to pipe system damage.
The strength and clarity of noise generated by leaks
will be affected by the water pressure, the size and
shape of the orifice allowing leakage, the type of
ground material around the pipeline, the type of
ground cover over the pipe, the diameter, wall thick-
ness and material of the pipeline and the quantity of
water leaking.
A small orifice or hole and high water pressure gener-
ally produce a higher frequency noise. Often the noise
level increases around valves, pipe elbows, T connec-
tions, pipe ends, etc. since the partial obstruction in-
creases pressure and creates some further distur-
bance in the water path.
Leak noise is transmitted along the pipeline both
through the water and the pipe wall as well as into the
ground around the pipe. The noise travels much better
through "hard" materials so that the noise travels
much further along metallic pipes than asbestos ce-
ment pipes which themselves are better than plastic
pipes. Ground material generally provides a poorer
travel path than the pipeline itself. Soft sandy ground
provides a worse travel path than well compacted
ground with a hard paved surface covering.
The leak noise can change in strength and pitch as it
travels along the pipe or through the ground. The
deeper the pipe is buried and the softer the ground the
more the noise will be dampened. The harder the pipe
material, the higher the frequencies detected will be,
and the further from the leak the noise will be detected
and the harder it becomes to accurately pinpoint the
exact point of maximum.
Background noise can interfere with leak detection.
Traffic and machinery noises can travel for consider-
able distances through both air and ground material
and often occur in the same frequency bands as leak
noise. Sometimes it is necessary to use leak detec-
tion techniques at night when interfering noises are
less.
It is very important to adopt a methodical approach
when using any instrument for acoustic leak detection.
It is necessary to practice the technique in order to dis-
tinguish between different sounds, recognising back-
ground or interfering noises, so that they can be elimi-
nated. It is also essential that other (non-leakage)
noise sources such as consumer draw-off or partially
closed valves are eliminated by logical site inspection
practices prior to any excavation taking place.
Hand probe
For normal soft ground surfaces the single pointed ex-
tension rod should be connected - do not overtighten
the screw thread. For direct contact with underground
fittings via access covers it may be necessary to use
the second extension rod - remove the single rod and
connect the extension rod - replacing the pointed rod
again. If the rods have been overtightened, spanner
slots allow easy removal.
Surveying
The leak location can be narrowed down by listening
at accessible contact points such as meters, hydrants,
valves and stop-taps, which provide points of good
sound pick-up particularly if the pipe is metallic. Use
the hand-probe/extension rod to listen at these points.
If there are no accessible contact points or if the pipe
is of non-metallic material use the microphone foot for
listening, placing the foot over the pipe route in the
area of the suspected leak. Move along the pipe route
listening at each accessible pipe-fitting or at regular
positions on the ground until you have identified the
area of maximum noise level.
Note
: When you are listening on pipe-fittings the loca-
tion of the point of maximum noise will probably not
indicate the leak position, only the fitting closest to the
leak. The noise level will also appear stronger where
there is less thickness of ground or other material for it
to pass through. The leak noise will follow the path of
least resistance.
Pinpointing the leak position
Pinpointing the leak position involves a process of
comparing a number of leak noises. Select the most
suitable sensor device; the microphone foot for hard
ground surfaces or the hand probe for soft ground.
Press the trigger to operate the Lmic and adjust the
headphone volume control to a comfortable listening
level. Once you have listened to the noise through the
headphones, release the trigger to switch off the am-
plifier and move the microphone foot or hand probe to
the next test position.
Repeat the sequence to listen to each of the test loca-
tions moving along the pipe route in the direction
where signal strength is increasing. If the leak noise
level falls you have passed the leak and should go
back and reduce the distance that you move between
measurements. The loudest leak noise will then indi-
cate the location of the leak bearing in mind the
ground conditions already mentioned.
3