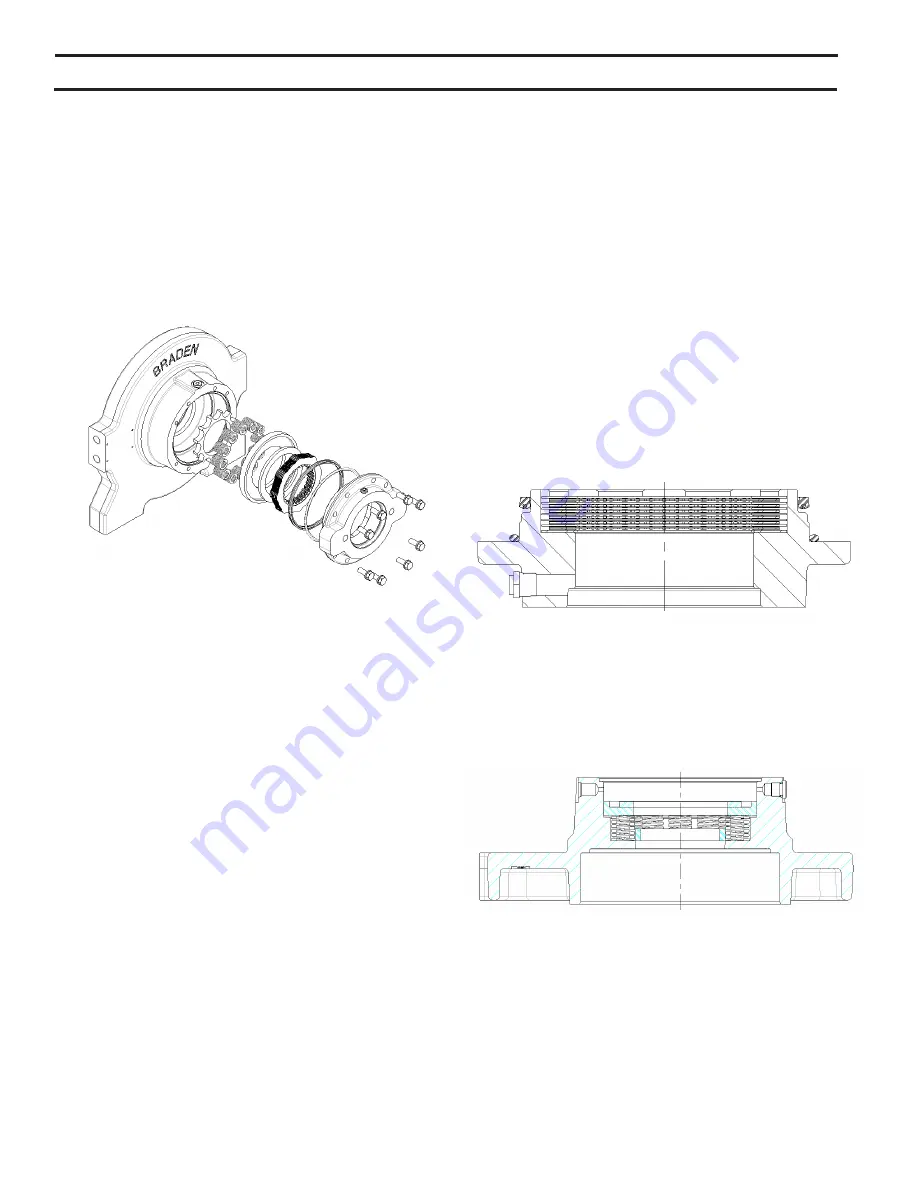
22
BRAKE SERVICE
Disassembly
1. Remove motor support by progressively loosening
eight capscrews, relieving the brake pack’s spring load.
Spring load will be relieved before capscrews disengage
motor support. Remove O-ring, U-cup seal, brake pack
(friction and steel discs), spacer and pressure plates,
brake springs, and spring spacer.
Inspection
1. Inspect sealing surfaces of motor support and brake cyl-
inder for wear and dings. Make sure the brake release
port is open and free of contamination.
2. Measure friction disc thickness with a caliper. Minimum
reusable thickness is .055 inch (1.40 mm). Measure flat
-
ness of both friction and steel discs. These should be
flat within .005 inch (0.13 mm). Look for signs of over
-
heating. Replace steel discs that show heat discoloring.
Examine friction facing for missing material, cracks, or
other damage. Replace as necessary. Inspect friction
splines for wear and replace if worn to a point.
3. Check spring free length with a caliper. Minimum length
is 0.938 inch (23.8 mm). Inspect springs for bending
or other damage. If any spring is suspect, replace all
springs as a set. Mixing old and new springs can cause
uneven pressure which contributes to poor brake ap-
plication, uneven friction disc wear, and possible spring
failure.
Reassembly
1. Begin reassembly by placing the motor support face-
down on a workbench.
2. Lubricate the new O-ring with oil and install onto the mo-
tor support. Lubricate the new U-cup seal and install so
that the O-ring side of the seal is facing the winch motor.
This allows the seal to expand when pressurized.
3. Soak friction discs in oil. This will keep the discs from
sticking together after spring pressure is applied.
4. Insert a steel disc into the bore of the motor support, fol-
lowed by a friction disc. Alternate steel and friction discs
until all are installed. The stack should finish with a steel
disc on top.
5. Place the brake housing end plate on a bench with cyl-
inder bore facing upward.
6. Install the spring spacer, followed by the brake springs,
pressure and spacer plates.