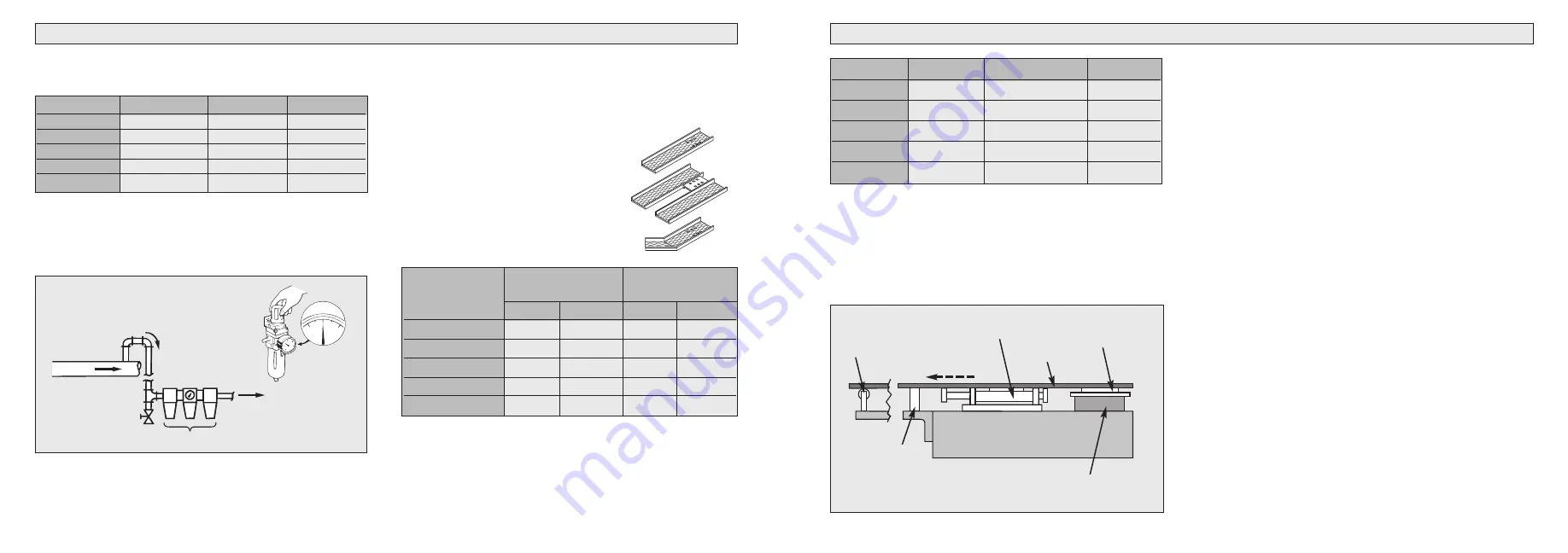
4
INSTALLATION
4. Connect the Air Line with flexible poly-flow tubing into
the threaded inlet. On Model TP-3 use 1/4” tubing for
1/8” NPT. Models TP-10, TP-40, TP-70 and TP-140 use
3/8” tubing for 1/4” NPT.
5. A custom “U” profile tray or chute
must be designed to handle each
specific application or tool. Any
material can be used, but we
recommend aluminum or any light
gauge material to reduce tray weight.
Maximum tray weight should not
exceed the following table data:
3. Fill the Lubricator with a good grade of hydraulic oil
such as Shell Tellus 32 or equivalent. Set the Lubricator
for one (1) drop per minute.
2. Air line requires use of an oil mist-type combination
Filter/Regulator/Lubricator, and Pressure Gauge. Set
pressure to 4-5 Bar (60 to 75 psi). Do not exceed 5.5 Bar
(80 psi) as excess pressure will damage the Transporter.
1. Rigidly Mount the Transporter to a solid surface using
these recommended bolts sizes:
Model
Quantity
Metric
Inch
TP-3
4
M 8
5/16
TP-10
4
M 8
5/16
TP-40
2
M10
3/8
TP-70
6
M 8
5/16
TP-140
6
M 8
5/16
60
(4)
75
(5)
Max. Weight Max. Weight
Tray Only
of Parts
Tray & Scrap
Model
Kg
Lbs.
Kg
Lbs.
TP-3
1,5
3.3
3
6.6
TP-10
3
6.6
10
20
TP-40
15
33
40
80
TP-70
50
110
70
140
TP-140
100
200
140
300
Recommended Air Line
Connection to Eliminate Moisture
and Particles from Main Line
Filter/Regulator/Lubricator
To Transporter
Drain
Main Air Line
6. Fasten the tray or chute to the Transporter with metric
screws at
all holes
. Be sure to use spacers or washers
between the Transporter and the tray to reduce contact
friction between the moving tray and the Transporter
body. Refer to the following table.
5
7. The Conveyor tray or chute must be supported at
both ends to minimize vibration and deflection. A block of
Delrin GP-500 or Nylon, low friction material can be used
for the tray to slide. For optimum installation, use P/A
Roller Slides to rigidly control the tray movement and
provide trouble-free operation. See page 27.
8. The Speed Adjustment is preset at the factory with
the correct frequency for a light weight tray or chute.
The speed can be adjusted by turning the screw or knob
clockwise to decrease the movement on the Models
TP-3, TP-10, and TP-40. The TP-70 and TP-140 are
adjusted by turning the screw or knob counter-clockwise
to decrease the movement. Maximum speed is not
required to move parts or scrap efficiently.
9. If the TP-40 Speed Frequency is inadequate, release
the Air Regulator Rod T40-029 and gently push forward
to increase speed or backward to decrease.
10. The TP-10 may require a slight adjustment to
maintain proper speed frequency after a period of
operation. If Speed Adjustment Screw T10-405 does not
slow the unit sufficiently, it may be necessary to slightly
snug the two screws at the Air Regulator Valve T10-401.
This reduces the air being released from the valve and
decreases speed. Snugging the screws too tightly will
cause bending of the Air Regulator Rod and poor
performance.
11. Spray the same Tellus oil used in lubrication on the
pistons each week.
12. If there is a build-up of sticky oil on the conveyor tray
or if the parts or scrap are very oily, they may stick to the
surface and reduce movement. To reduce the coefficient
of friction, try dimpling the surface of the conveyor chute
with a ballpeen hammer or use a different material like
expanded metal or profiled, roll formed material.
Chute
or Tray
Roller Slide
Spacer
Ball Bearing
Roller
Transporter
Feed Direction
Solid Slide -
Low Friction
Material
Press Bolster
Model
Quantity
Screw size
Depth
TP-3
6
M6
8mm
TP-10
6
M6
8mm
TP-40
6
M8
9mm
TP-70
6
M8
8mm
TP-140
6
M8
8mm
INSTALLATION