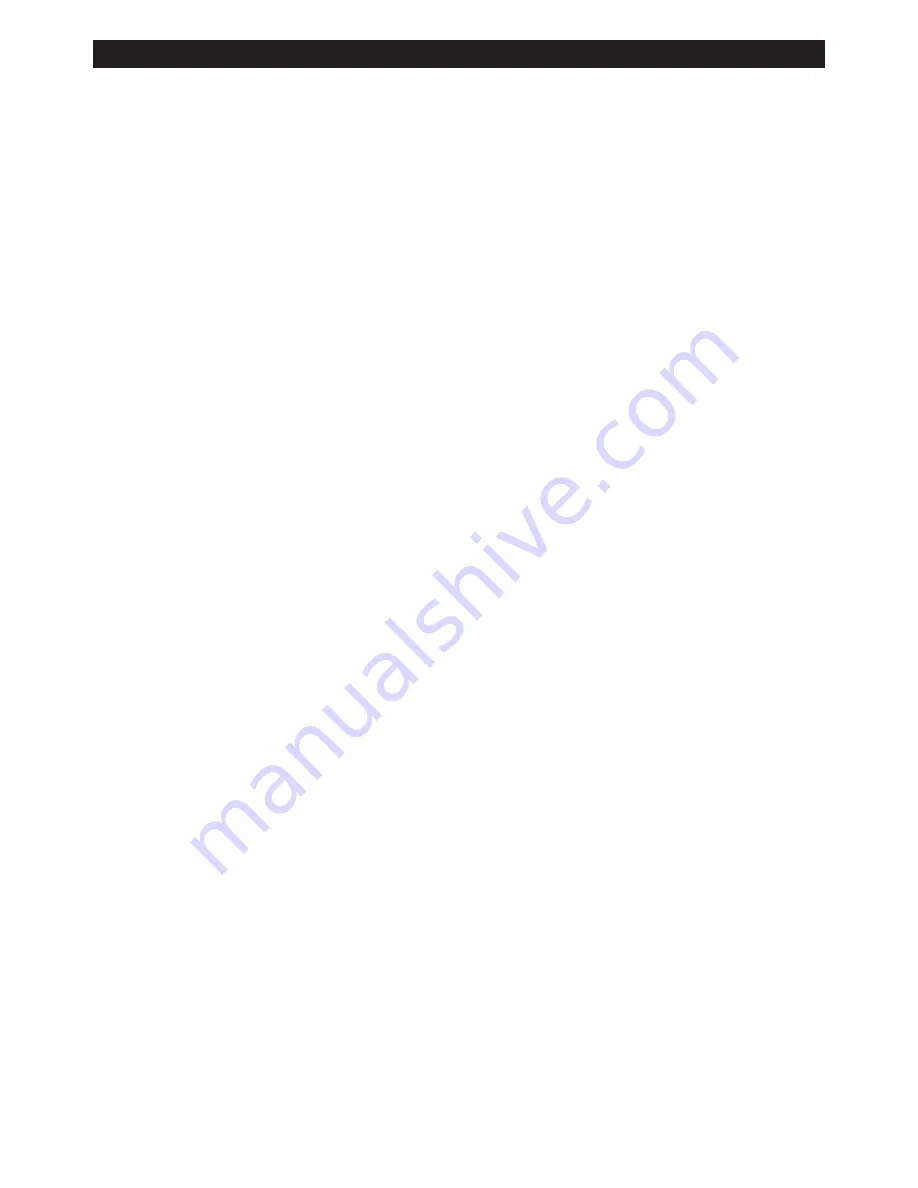
Immersion heaters
All indirect units are fitted with one immersion heater which is located behind the electrical box. With
the exception of the 100 litre all direct units have two immersion heaters.
Direct Units
Wiring instructions for the immersion heaters are located on the reverse side of the lid. Follow the
wiring instructions connecting the live, neutral and earth as indicated. The electrical connection to the
immersion heater must conform to current IEE wiring regulations. The unit must be permanently
connected to the electrical supply through a double-pole linked switch with a minimum break capacity
of 13 amps. All internal wiring is factory mounted. Each immersion heater has a working thermostat
adjustable between 40°C - 70°C. A safety cut-out is also incorporated within the thermostat and will
operate at 85°C ± 3°C. Should this happen, press the reset button.
Important: Before resetting the safety cut-out or altering the thermostat setting, isolate
electrical supply to the unit prior to removal of the lid. Ensure the lid to the electrical box is
replaced correctly and the retaining screw is fitted.
The lower immersion heater should be connected to the off peak supply (if available) whilst the top
immersion heater can be connected to the day tariff. The immersion heater can be connected to the
mains supply through a water heater controller (Contact your local electricity company if in doubt).
Indirect Units
Motorised valve
To comply with regulations governing the installation of indirect unvented cylinders, a motorised valve
must be fitted in the primary flow. Your OSO unit has been supplied with a two port motorised valve,
which will act as a positive energy cut-out should the safety cut-out operate. The motorised valve will
also control the temperature of the domestic stored water via the cylinder thermostat, which is located
in the electrical box. The unit should be installed on an “S” or “Y” plan system.
Please follow the
instructions carefully.
All electrical connections must conform to current IEE wiring regulations. The
working thermostat which controls the temperature of the domestic hot water (see fig. 2) is adjustable
between 40°C - 70°C. A safety cut-out is also incorporated within the thermostat and will operate at
85°C ± 3°C. Should the safety cut-out be brought into operation, the motorised valve will operate and
close down the primary flow to the cylinder. To reset the safety cut-out and the motorised valve the
reset button must be pressed in (see fig. 2). If using a 6-wire 28mm or
1'' BSP V4043H on either circuit
the white wire is not needed and must be made electrically safe.
OSO Hotwater (UK) Limited can not be responsible if alternative wiring plans are used.
Important: Before resetting the safety cut-out or altering the thermostat setting isolate
electrical supply to the unit before removal of the lid.
ELECTRICAL INSTALLATION
-7-