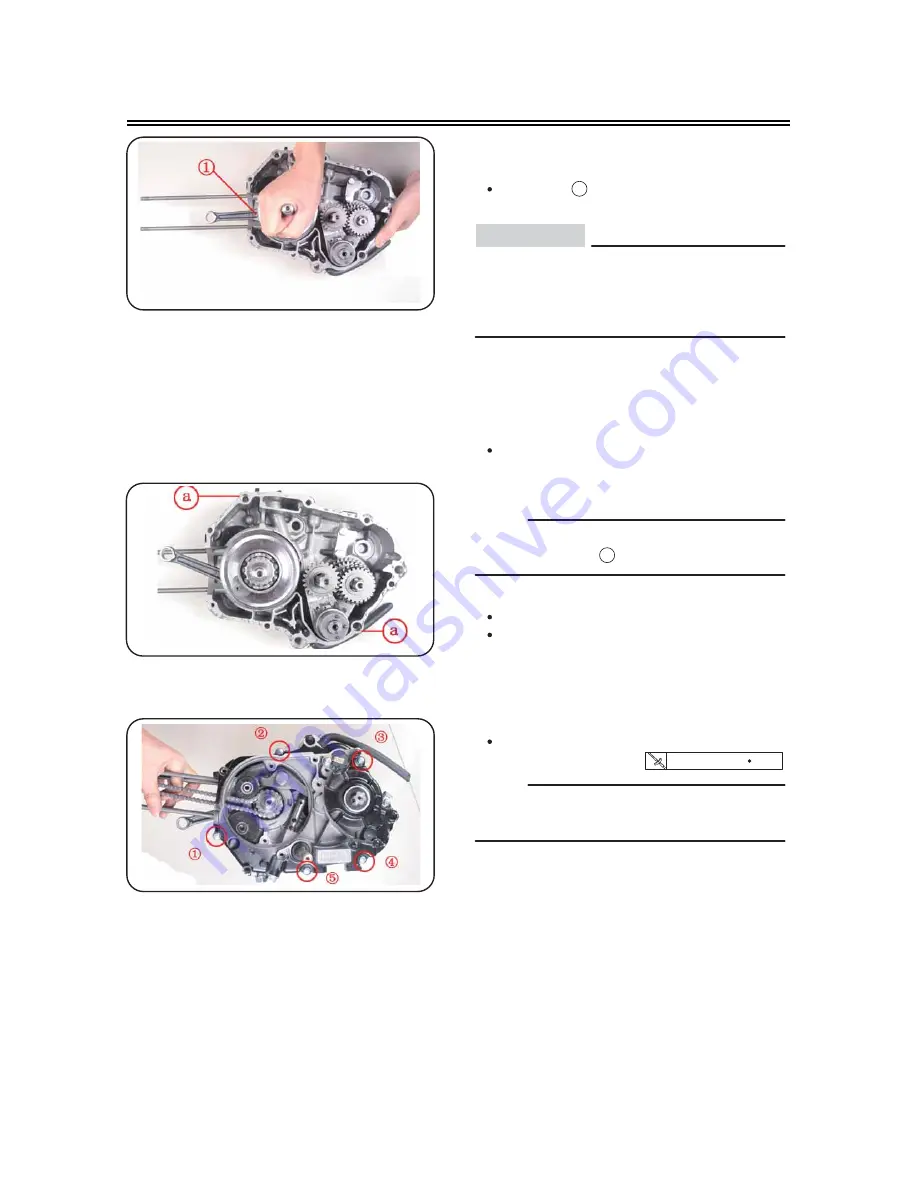
4 - 55
CRANKSHAFT
CAUTION:
NOTE:
10 Nm (1.0 m kg)
NOTE:
INSTALLING THE CRANKSHAFT
1. Install:
crankshaft
1
To avoid scratching the crankshaft and to
ease
the
installation
procedure, apply
grease onto the oil seal lips and apply en-
gine oil onto each bearing.
ASSEMBLING THE CRANKCASE
1. Thoroughly clean all the gasket mating sur-
faces and crankcase mating surfaces.
2. Apply:
sealant
(onto the crankcase mating surfaces)
Do not allow any sealant to come into contact
with the oil gallery
a
.
3. Install:
dowel pins
right crankcase
4. Tighten:
crankcase right half
Tighten the screws in decreasing numerical or-
der (see numbers on the illustration).
Содержание AGB-21G
Страница 1: ...AGB 21G SERVICE MANUAL ...
Страница 2: ......