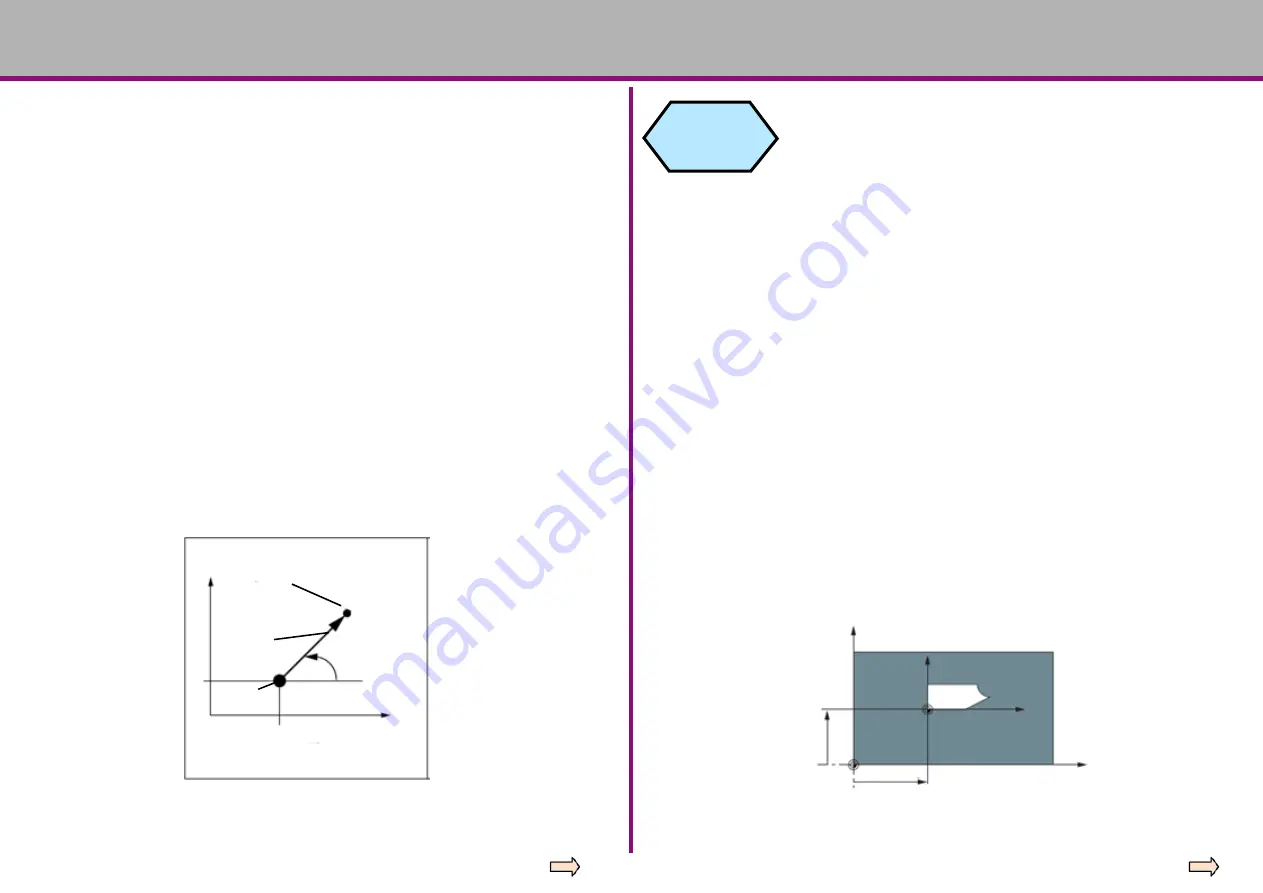
OPTIMUM
M A S C H I N E N - G E R M A N Y
808D
Page 367
Additional Information Part 2
Brief instruction 808D Milling
Operating and Programming — Milling
Basic Theory
G110
Pole specification relative to the setpoint position last programmed (in the plane,
e.g. with G17: X/Y)
(when using G110, please always take the current position of the tool as the
reference point to specify the new pole)
G111
Pole specification relative to the origin of the current workpiece coordinate
system (in the plane, e.g. with G17: X/Y)
G112
Pole specification, relative to the last valid pole; retain plane
Programming example
The programmable workpiece offsets TRANS and ATRANS can be used in the following
cases:
For recurring shapes/arrangements in various positions on the workpiece.
When selecting a new reference point for dimensioning.
This results in the current workpiece coordinate system.
N10 G17
; X/Y plane
N20 G111 X17 Y36
; pole coordinates in the current workpiece
AP=45 RP=50
coordinate system
...
N80 G112 X35.35 Y35.35
; new pole, relative to the last pole as a
AP=45 RP=27.8
polar coordinate
N90 ... AP=12.5 RP=47.679
; polar coordinate
N100 ... AP=26.3 RP=7.344 Z4
; polar coordinate and Z axis(= cylinder coordinate)
Point defined by RP, AP
Y
X
Example G17: X/Y plane
RP=...
Pole
AP=...
+
TRANS X...Y... Z...
; programmable offset(absolute)
ATRANS X...Y... Z...
; programmable offset, additive to existing offset
(incremental)
TRANS
; without values, clears old commands for offset
Programming example
N20 TRANS X20.0 Y15.0
programmable offset
L10
subprogram call
Machine
coordinate
system
Additive
workpiece
offsets
TRANS Y
Y
W
TRANS X...
X
Y
X
L10