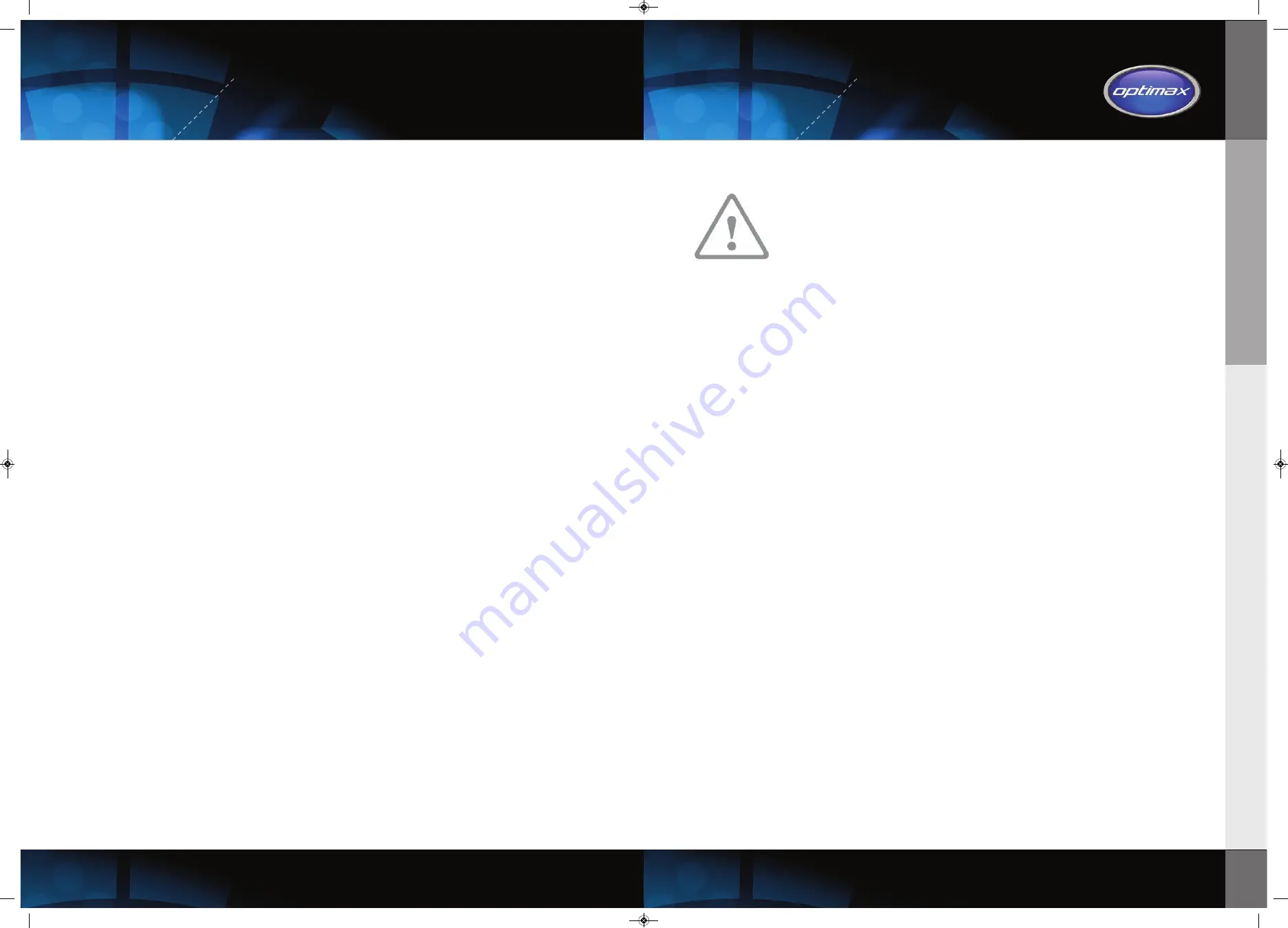
®
OPTIMUM QUALITY MAXIMUM RELIABILITY
TM
7
6
C
P
4
2
2
S
2
4
M
M
-
3
P
H
O
P
E
R
A
T
IN
G
I
N
S
T
R
U
C
T
IO
N
S
Important Operating Instructions
>
This machine is suitable for processing paper materials exceeding
60gsm and corrugated cardboard up to 15mm thick.
>
Use of unsuitable materials may result in operator injury, damage to
the machine and accelerated wear or damage of the cutting blades.
>
If processing waste packaging material, always ensure that no hard
objects are concealed in folds or carton flaps.
>
If processing cartons containing staples, where possible feed the
cartons through the machine so that the stapled areas fall outside
the feed path and discard these sections.
>
Individual staples cannot cause damage to the cutting mechanism, but
risk damage to packaged contents or injury if left in packaging material.
Safety
Operating Instructions should be readily available and must be complied with at all times.
Care must be taken to prevent long hair, loose clothing and jewellery from becoming
caught in the mechanism.
Defects and malfunctions which endanger the safety of the employees must be repaired and the
machine must be put out of operation until these hazards have been eliminated.
Maintenance and service
The machine must be thoroughly checked at least once a year by an authorised person.
All safety features must be checked every 2-3 months to confirm they have not been
removed or disabled and to identify signs of wear or malfunction.
The cutting mechanism must be regularly checked and kept clean (see instructions on
page 3 of this manual).
The cutting rollers must be lubricated periodically, by spraying light oil such as WD40 onto
them through the feed inlet (7) whilst the machine is running.
Operation
Connect to power supply. Release emergency stop button (9) by rotating it anticlockwise.
When the green light shows (8) the machine is operational. Press the green button (5) to
commence operation.
Feed cardboard material into the feed aperture (1) until the mechanism grips it. Large
pieces of cardboard may require additional support, but hands must be kept well clear of
the feed aperture at all times.
If the thickness of cardboard fed into the machine is too thick and it jams, press the
emergency stop button to stop the machine, then the reverse button (3) to remove the
cardboard from the machine.
An automatic safety device will activate if a blockage is not detected by the operator, and
will switch off the machine for 2-3 minutes before resetting. The blockage should be
removed using the reverse button as above before resuming operation.
Padding flap
The flap attached at the rear of the machine converts the processed cardboard into high-bulk
void fill.
If separate strips are required, disconnect the two springs situated either side of the flap (10).
Caution
– ensure that processed cardboard can freely exit the outlet channel at all times.
OPTIMAX ECOPAX CP422S24MM-3PH INSTRUCTIONS A4_Layout 1 29/03/2016 10:21 Page 7