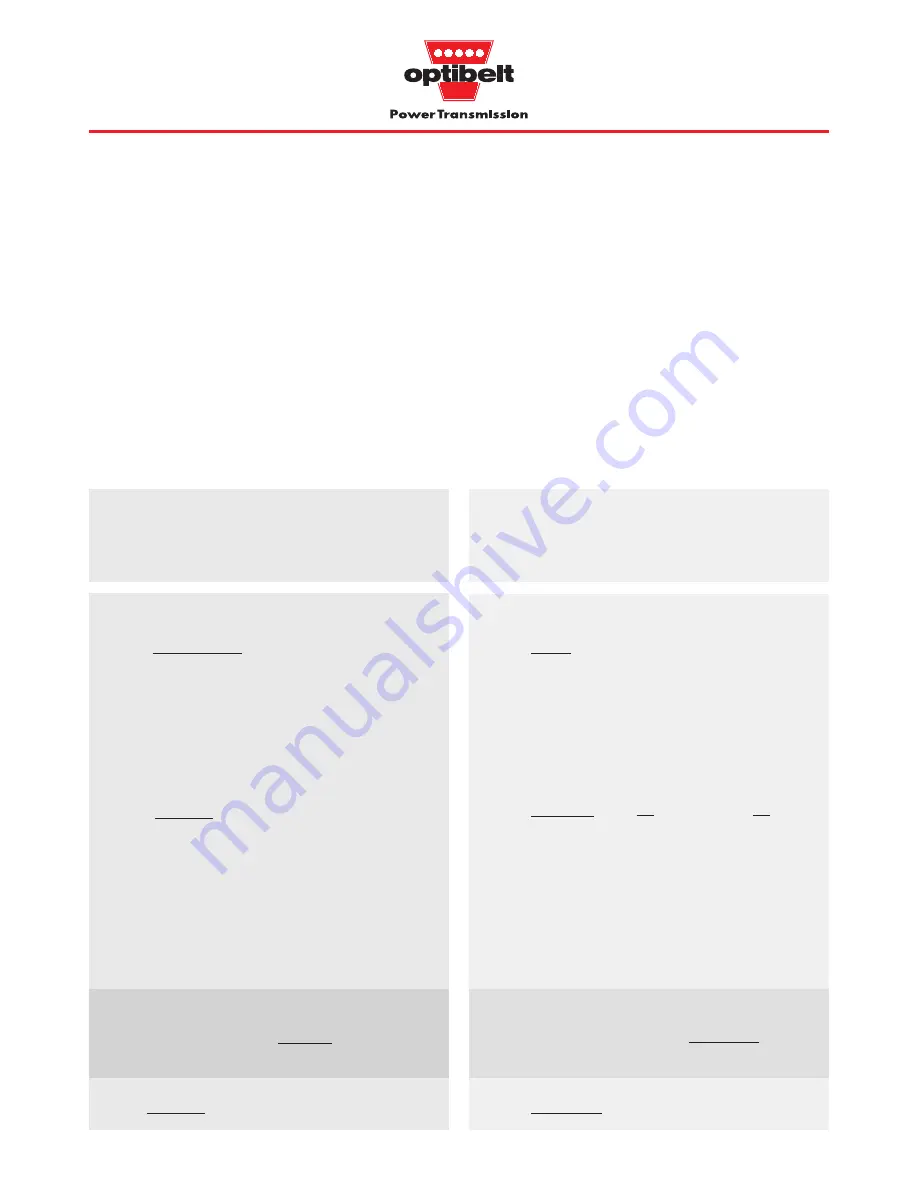
34
Driver and driven details
Type of drive:
vertical positioning* by means of an
open-ended timing belt
Mass moved:
m
≤
8.0 kg, sliding and conveying
Required
speed of travel:
v
= 3.3 m/s
Starting/stopping distance: s
≥
320 mm
Prime mover:
DC motor
Starting torque:
M
A
= 2 M
N
Input drive speed:
n
1
= 950 min
-1
4.3 ZRL-M drive design
Drive design of open-ended
optibelt
ZRL-M
timing belting for linear drive
systems, e
max
= 12
Operating conditions, geometry
Daily operating time:
max. 24 hours
Starts/stops per day:
approx. 2000
Type of start:
under load
Type of load:
medium shock load
Ambient conditions:
room temperature,
cutting oil contamination
Required centre distance:
a = 3236 mm
Overall width:
b
1
, B as required
Clearance diameter:
≤
90 mm
* For lifting and inclined conveyor systems where the failure of the belt could cause damage or injury due to the release of the conveyed
material, special care should be taken.
Formulae
Example
Timing belt load
c
2
= 1.7 + 0 + 0.3 = 2.0
c
0
= 1.7
c
6
= 0
c
8
= 0.3
extremely high start/stop frequency
S
Bn3
= 2.0 · 214.5 = 429 N
S
n3
=
= 214.5 N
Friction can be neglected here
S
n3tot
= 136.0
+ 78.5
+ 0 = 214.5 N
S
n3tot
= 8.0 · 17.0 + 8.0 · 9.81 · sin 90
°
+ 0 · 8.0 · 9.81 · cos 90
°
m
tot
= 8 kg
a
1
=
= 17.0
g = 9.81
For special belt constructions, see pages 9 to 11
µ
tot
=
0
µ
1
=
0
µ
2
=
0
friction of guide is neglected!
α
= 90
°
, vertical conveyor
M
Bth
= 2.0 · 7.1 = 14.2 Nm M
Abth
=
= 7.1 Nm
d
w1th
=
= 66.4 mm
Calculation using centrifugal force S
Bn3
S
Bn3
= c
2
· S
n3
S
n3
=
Force due to acceleration F
B
, force due to weight G and friction force F
R
S
n3tot
= F
B
+ G · sin
α
+ F
R
· cos
α
S
n3tot
= m
tot
· a
1
+ m
tot
· g · sin
α
+
µ
tot
· m
tot
· g · cos
α
Total mass m
tot
m
ges
= m
1
+ m
2
+ . . . + m
n
Acceleration a
1
and g
a
1
=
g = acceleration due to gravity
Coefficient of friction
m
µ
ges
=
µ
1
+
µ
2
µ
,
µ
0
see Table
1.6,
page 10
Sliding friction and frictional grip
,
µ
1
for belt/conveyed material
Sliding friction and frictional grip
,
µ
2
for belt/support rail or
guide
Angular deviation
a
from the horizontal
α
= 0
°
, vertical movement,
sin 0
°
= 0, cos 0
°
= 1
α
= 90
°
, horizontal movement, sin 90
°
= 1, cos 90
°
= 0
Alternative: calculation using torque
Theoretical design torque M
Bth
M
Bth
= c
2
· M
Abth
M
Abth
=
If M
Ab
is not known:
M
B
= c
2
· M
An
formulae see page 13
Theoretical pitch diameter d
w1th
d
w1th
=
214.5
1
S
n3tot
number of belts
3.3
2
· 10
3
2 · 320
v
2
· 10
3
2 · s
m
s
2
m
s
2
19100 · v
n
1
S
n3
· d
wth
2000
19100 · 3.3
950
Overall drive service factor c
2
c
2
= c
0
+ c
6
+ c
8
Basic drive service factor
c
0
Table 2.1, page 12
Pulley and idler correction factor
c
6
Table 2.2, page 13
Start/stop under load factor
c
8
Table 2.2, page 13
214.5 · 66.4
2000
Содержание ZRL
Страница 54: ...53 ...
Страница 95: ...94 ZRM ZRP Data Sheet Notes ...