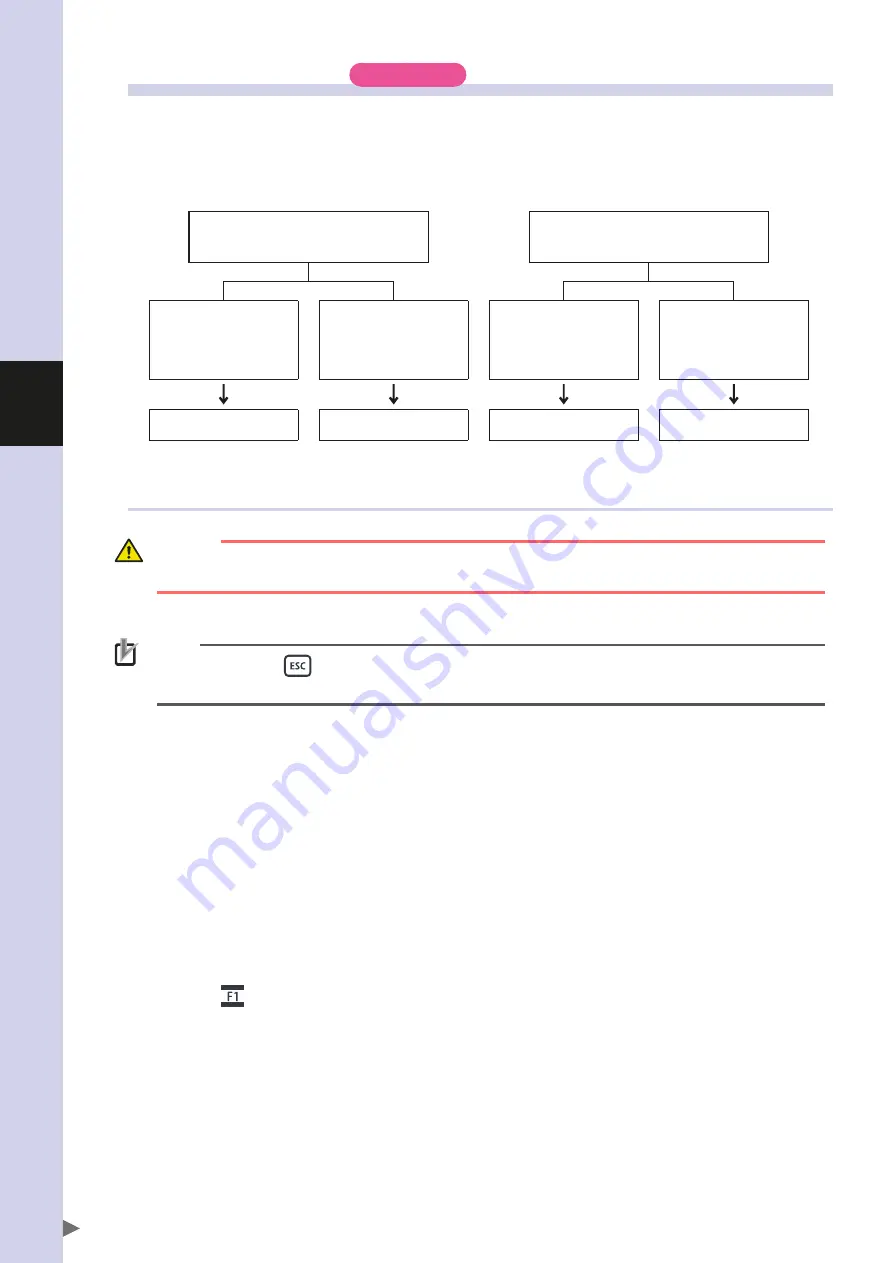
4
Adjusting the or
ig
in
4-10
1.3 Mark method
R6YXE400
The absolute reset in the mark method is classified into four groups according to the conditions as shown in
the flowchart below.
Since each operating procedure varies, refer to relevant portion.
■
Absolute reset flowchart
(*)
The origin is performed at the same
position as the previous absolute reset
position.
The origin is performed at a position
different from the previous absolute
reset position.
The origin position mark
can be seen from a
position beyond the robot
movement range.
The origin position mark
cannot be seen from a
position beyond the robot
movement range.
The robot can be guided
to the new origin position
by the servo drive from a
position beyond the robot
movement range.
The robot cannot be
guided to the new origin
position by the servo
drive from a position
beyond the robot
movement range.
To “1.2.1 absolute reset in
servo on state (re-reset)”
To “1.2.2 absolute reset in
servo off state (re-reset)”
To “1.2.3 absolute reset in
servo on state (new reset)”
To “1.2.4 absolute reset in
servo off state (new reset)”
(*) To perform the absolute reset for the first time, refer to
this portion.
1.3.1 Absolute reset in servo on state (re-reset)
WARNING
Serious injury might occur from physical contact with the robot during operation. Never enter within the robot
movement range during absolute reset.
The operation procedure using the PBEX is described below.
NOTE
• When pressing the
key on the execution confirmation screen, the execution of the absolute reset is canceled.
• For details about how to operate the robot controller, see the "OMRON Robot Controller User's Manual".
Step1
Turn on the controller.
Check that no one is inside the safety enclosure, and then turn on the controller.
Step2
Place a sign indicating the robot is being adjusted.
Place a sign indicating the robot is being adjusted, to keep others from operating the controller or
operation panel.
Step3
Move to a position where the origin position sticker can be seen.
Move to a position where the origin position sticker can be seen while holding the PBEX. At this time,
never enter the robot movement range.
Step4
Display the "ORIGIN RTN (TRQ/SENS)" screen on the PBEX (operation
→
return-
to-origin).
Step5
Display the "ORIGIN RTN (MARK)" screen.
Press
(MARK) on the "ORIGIN RTN (TRQ/SENS)" screen.
Содержание SCARA R6Y XE Series
Страница 1: ...7 6HULHV DW 1R 1 5 VHULHV 0 17 1 1 0 18 6 5 5RERWV VHULHV...
Страница 2: ......
Страница 6: ......
Страница 8: ......
Страница 10: ......
Страница 14: ......
Страница 16: ......
Страница 20: ......
Страница 30: ......
Страница 50: ......
Страница 90: ......
Страница 92: ......
Страница 104: ......
Страница 108: ......
Страница 110: ......
Страница 124: ......
Страница 135: ...Chapter 10 Robot cable replacement Contents 1 Robot cable replacement 10 1...
Страница 136: ......
Страница 139: ...Chapter 11 Maintenance parts Contents 1 Consumable parts 11 1 2 Basic specification 11 2...
Страница 140: ......
Страница 144: ...DW 1R 1 XWKRUL HG LVWULEXWRU 3ULQWHG LQ XURSH...