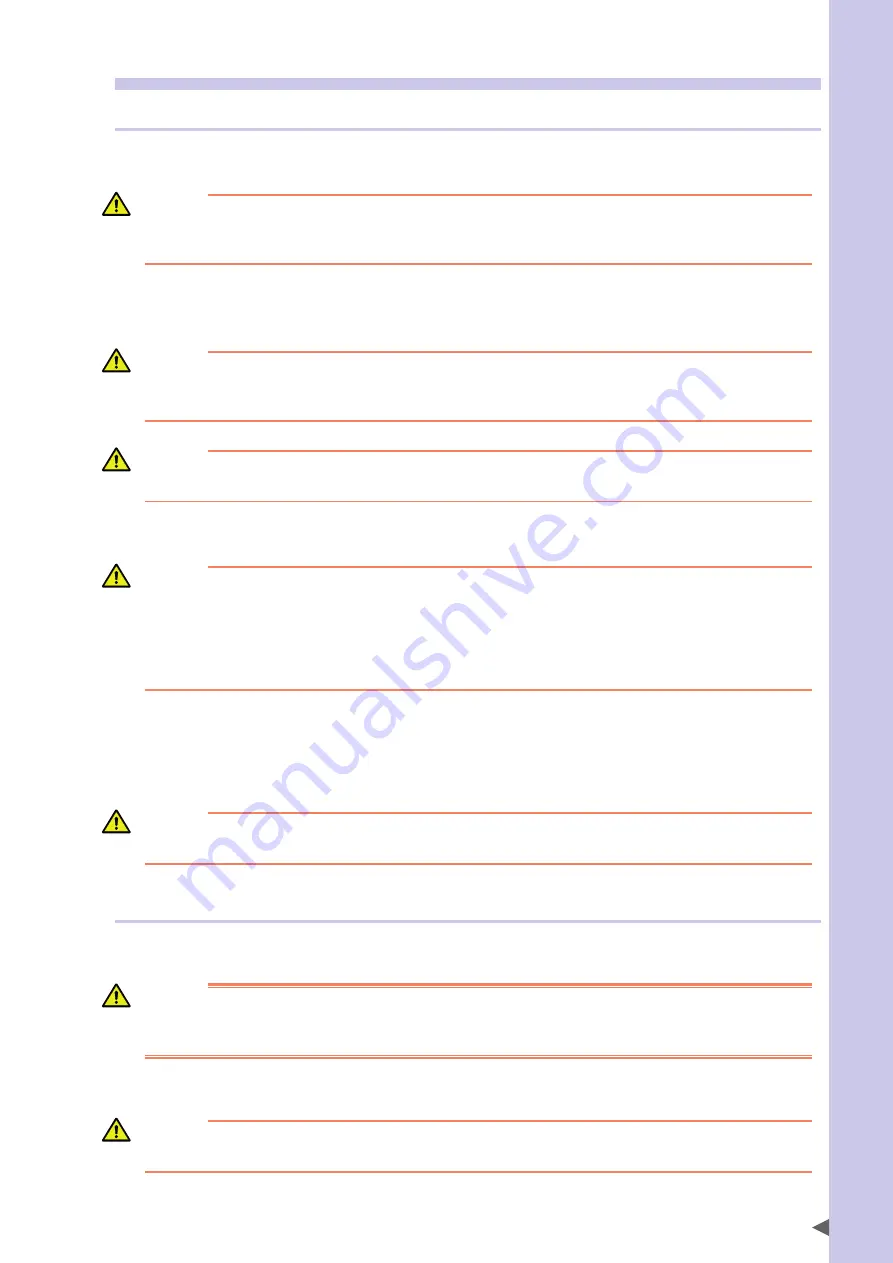
Safety Instr
uctions
S-9
4.2 Design
4.2.1 Precautions for robots
1.
Restricting the robot moving speed
WARNING
RESTRICTIon on THE RoboT movInG SpEEd IS noT A SAFETY-RELATEd FUnCTIon.
To REdUCE THE RISK oF CoLLISIon bETWEEn THE RoboT And WoRKERS, THE USER mUST TAKE THE
nECESSARY pRoTECTIvE mEASURES SUCH AS EnAbLE dEvICES ACCoRdInG To RISK ASSESSmEnT bY THE USER.
2.
Restricting the movement range
See “7.1 Movement range” in “Safety instructions” for details on the robot’s movement range.
WARNING
SoFT LImIT FUnCTIon IS noT A SAFETY-RELATEd FUnCTIon InTEndEd To pRoTECT THE HUmAn bodY.
To RESTRICT THE RoboT movEmEnT RAnGE To pRoTECT THE HUmAn bodY, USE THE mECHAnICAL SToppERS
InSTALLEd In THE RoboT (oR AvAILAbLE AS opTIonS).
CAUTION
If the robot moving at high speed collides with a mechanical stopper installed in the robot (or available as option), the robot may be
damaged.
3.
Provide safety measures for end effector (gripper, etc.)
WARNING
• End EFFECToRS mUST bE dESIGnEd And mAnUFACTUREd So THAT THEY CAUSE no HAZARdS (SUCH AS A
LooSE WoRKpIECE oR LoAd) EvEn IF poWER (ELECTRICITY, AIR pRESSURE, ETC.) IS SHUT oFF oR poWER
FLUCTUATIONS OCCUR.
• IF THE obJECT GRIppEd bY THE End EFFECToR mIGHT poSSIbLY FLY oFF oR dRop, THEn pRovIdE
AppRopRIATE SAFETY pRoTECTIon TAKInG InTo ACCoUnT THE obJECT SIZE, WEIGHT, TEmpERATURE, And
CHEmICAL pRopERTIES.
4.
Provide adequate lighting
Provide enough lighting to ensure safety during work.
5.
Install an operation status light
WARNING
InSTALL A SIGnAL LIGHT (SIGnAL ToWER) AT An EASY-To-SEE poSITIon So THAT THE opERAToR WILL bE AWARE
oF THE RoboT STop STATUS (TEmpoRARILY SToppEd, EmERGEnCY STop, ERRoR STop, ETC.).
4.2.2 Precautions for robot controllers
1.
Emergency stop input terminal
DANGER
EACH RoboT ConTRoLLER HAS An EmERGEnCY STop InpUT TERmInAL To TRIGGER EmERGEnCY STop. USInG
THIS TERmInAL, InSTALL A SAFETY CIRCUIT So THAT THE SYSTEm InCLUdInG THE RoboT ConTRoLLER WILL
WoRK SAFELY.
2.
Maintain clearance
CAUTION
Do not bundle control lines or communication cables together or in close to the main power supply or power lines. Usually separate
these by at least 100mm. Failure to follow this instruction may cause malfunction due to noise.
Содержание R6YXG500
Страница 1: ...ZX T Series Cat No I155E EN 03A R6Y XG series INSTALLATION MANUAL SCARA Robots XG Series...
Страница 2: ......
Страница 10: ......
Страница 36: ......
Страница 38: ......
Страница 39: ...Contents Before using the robot Be sure to read the following notes i Introduction v Introduction...
Страница 40: ......
Страница 46: ......
Страница 48: ......
Страница 56: ......
Страница 169: ...2 Installation 2 111 Installing the extension shaft Extension shaft 1 Upper nut Bolt 2 6 Go out of the safety enclosure...
Страница 174: ......
Страница 176: ......
Страница 220: ......
Страница 221: ...Chapter 4 Periodic inspection Contents 1 Overview 4 1 2 List of inspection items 4 2...
Страница 222: ......
Страница 226: ......
Страница 227: ...Chapter 5 Harmonic drive replacement period Contents 1 Overview 5 1 2 Replacement period 5 2...
Страница 228: ......
Страница 232: ......
Страница 238: ......
Страница 239: ...Chapter 7 Torque limit designated Z axis pushing action Contents 1 Torque limit designated Z axis pushing action 7 1...
Страница 240: ......
Страница 244: ......
Страница 246: ......
Страница 323: ...8 Specifications 8 77 1 3 Robot inner wiring diagram Robot inner wiring diagram R6YXG500...
Страница 330: ...Cat No I155E EN 03A Note Specifications subject to change without notice Authorized Distributor Printed in Europe...