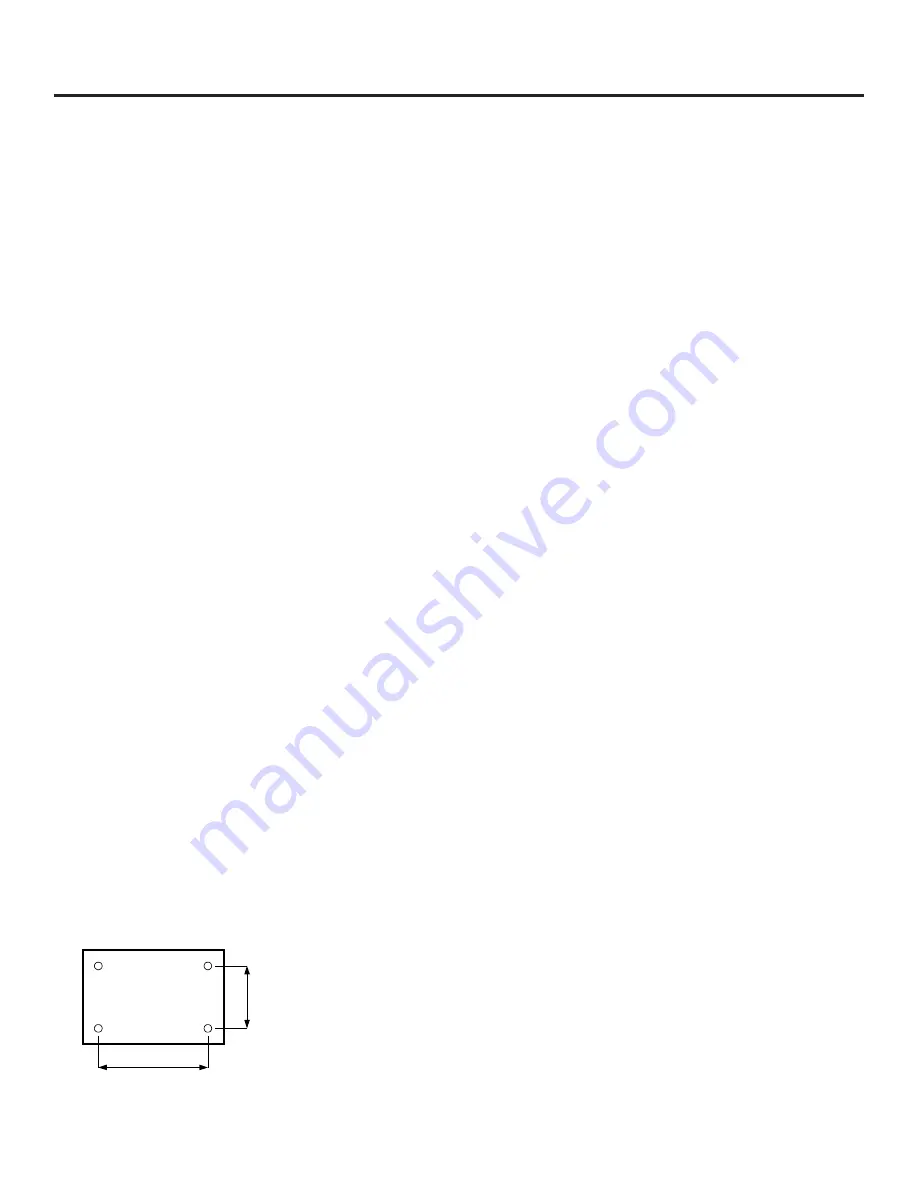
Page 5
OMNI by EconoHeat
Specifications
BTU
INPUT:
75,000
BTU
OUTPUT:
60,000
GALLONS PER HOUR:
0.5
REQUIRED
VOLTS:
115
AMPs
FULL
LOAD:
10.5
FAN
MOTOR
HP:
1/10
FAN MOTOR RPM:
1625 – 1550
CFM (FREE AIR):
1500 – 1400
EFFECTIVE AIR FLOW:
50 ft
FLUE
SIZE:
6"
WEIGHT:
150
lbs
L x W x H (including burner):
50” x 24” x 24”
SHIPPING WEIGHT:
260 lbs
SHIPPING DIMENSIONS (L x W x H): 60” x 34” x 30”
Notes:
1. All illustrations and specifications contained are based on the latest information available
at the time of publication approval. EconoHeat reserves the right to make changes
at any time without notice, in materials, specifications, and models or to discontinue
models.
2. These appliances are designed for commercial or industrial use only. Installation and
use of this waste-oil burning appliance shall be in accordance with the Standard for
the Installation of Oil Burning Equipment-ANS/NFPA 31-1987, and National Electric Code -
ANSI/NFPA 70-1990 and the requirements of the inspection authorities having jurisdiction.
3. Output depends on BTU content of oil used.
4. Furnace not to be used with air filters.
5. Intended maximum outlet air temp. 200 degrees F. (93 degrees C) or less.
6. Clearance from combustible materials on all models not to be less than:
TOP-
18”
BOTTOM-
18” SIDES-
18”
REAR-
18”
FRONT-
48”
FLUE
PIPE-
18”
Mounting Dimensions:
Heater (top)
32”
12.5”