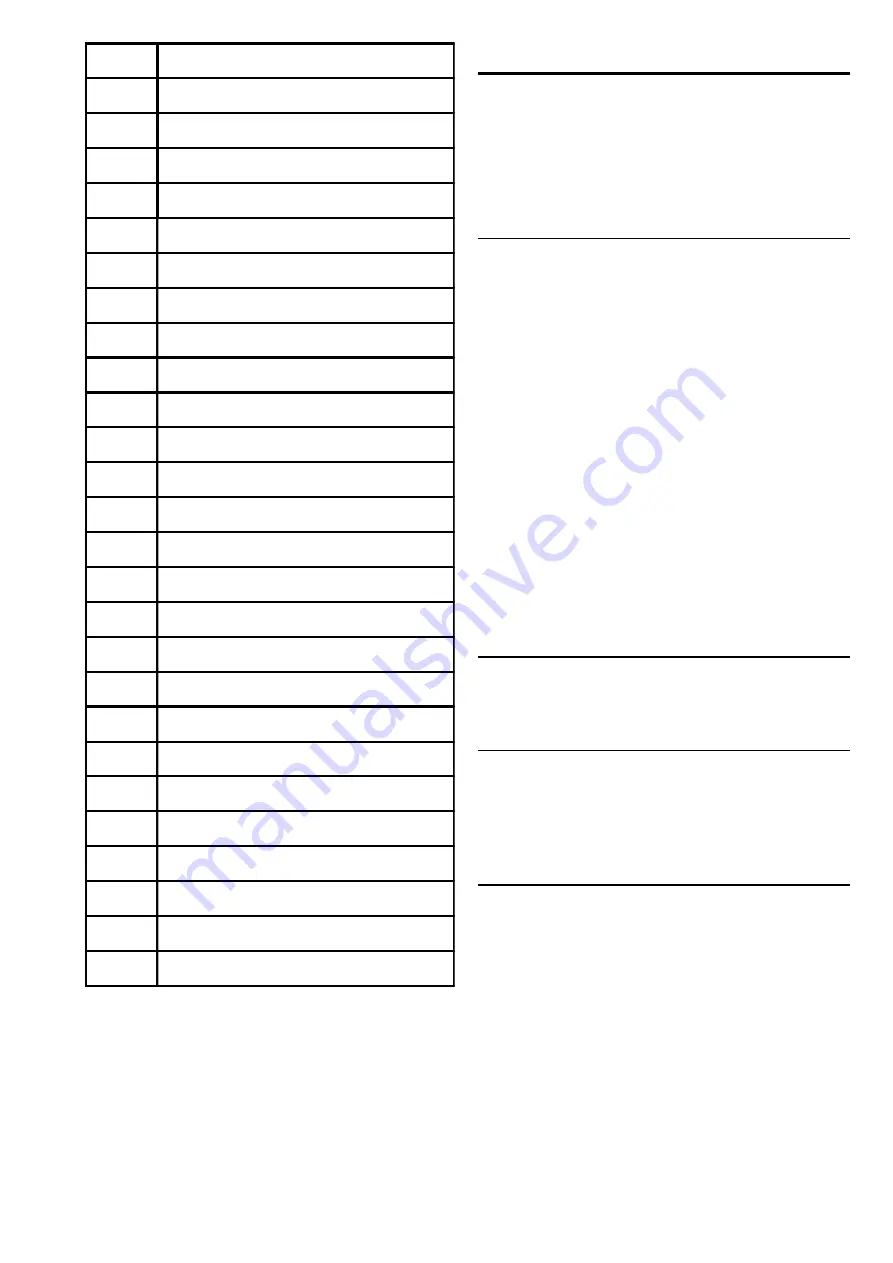
R
OUTINE
S
AFETY
C
HECKS
TO BE CARRIED OUT ONLY BY QUALIFIED AND
EXPERIENCED PERSONNEL.
Check that the plant room is ventilated at all times.
Frequently inspect the air inlet of the burner and
ensure that there are no obstructions to air flow.
Flame Detection System (IRD Cell)
•
With the system set for normal operation, pull
out the detector probe and cover it up to cut
off light. Both LED indicators must extinguish.
The control box should switch to lockout or
attempt to re-start the sequence.
•
Attempt to re-start with the flame detector
covered. There must be no indication from
the LED’s after the start impulse. The burner
control box must switch to lockout at the end
of the safety interval.
•
Attempt to start the burner with the detec-
tor exposed to stray light e.g. from fluores-
cent lighting, a cigarette lighter or light bulb
(not daylight or an electric torch): The con-
trol box should switch to lockout either im-
mediately or at the end of the pre-purge, as
a result of stray light.
R
OUTINE
M
AINTENANCE
Switch off electrical supply and gas supply to the
burner.
Combustion Air Fan
Clean the blades regularly with a stiff brush. Access
is obtained through the burner top cover. Care
should be taken to avoid damaging the fan blades.
Check that the air inlet into the fan is clean.
Inner Assembly
Open the hinged extension as follows: -
XGN450 to XGN1000. Remove the split pin from
the hinge pin adjacent the gas train and withdraw
the hinge pin form the hinged extension.
XGN1150 to XGN3000. Remove the 2 locking
nuts and washers securing the hinged extension.
Screen
Information
0
Air and gas setting point P0
1
Air and gas setting point P1
2
Air and gas setting point P2
3
Air and gas setting point P3
4
Air and gas setting point P4
5
Air and gas setting point P5
6
Air and gas setting point P6
7
Air and gas setting point P7
8
Air and gas setting point P8
9
Air and gas setting point P9
10
Most recent fault code
11
Second last fault code
12
Third last fault code
13
Fourth last fault code
14
Fifth last fault code
15
Sixth last fault code
16
Testing time Y2
17
Testing time Y3
18
Flame quality indication (1-4)
19
eBus address
21
Integrated valve test, on/off
22
Lower limit of modulation
23
Upper limit of modulation
24
Controller address
25
Motor speed
26
Motor rotation and reference
Содержание XGN Series
Страница 1: ...Page 1 XGN Handbook HANDBOOK Series XGN fully automatic burners Models XGN450 to XGN3000 Natural Gas...
Страница 4: ...XGN Handbook Page 4...
Страница 23: ...Page 23 XGN Handbook XGN450 23 XGN650 23...
Страница 24: ...XGN Handbook Page 24 XGN1000 25 XGN1150 38...
Страница 30: ...XGN Handbook Page 30 NOTES...
Страница 31: ...Page 31 XGN Handbook NOTES...