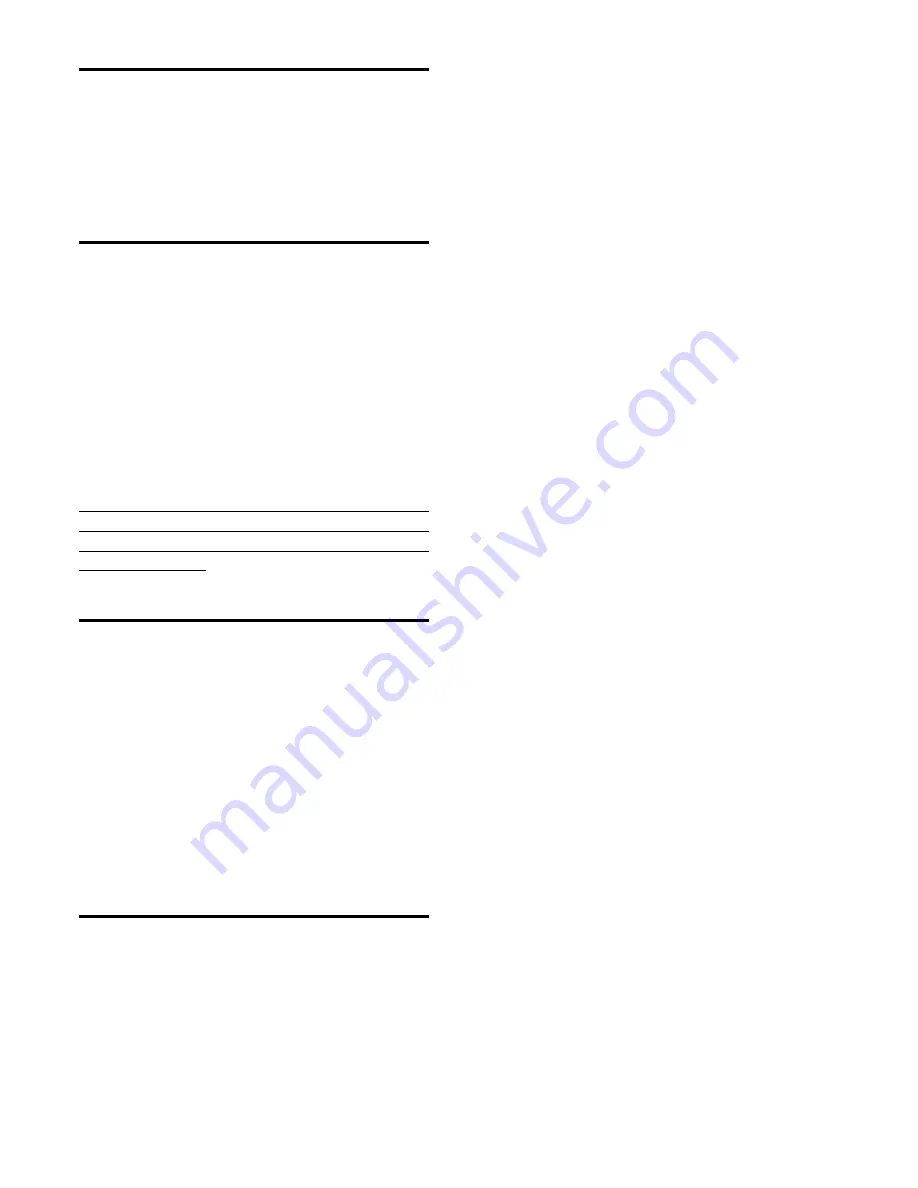
P Series Commissioning
Page D.2
IIIII
NDIVIDUAL
NDIVIDUAL
NDIVIDUAL
NDIVIDUAL
NDIVIDUAL
S
S
S
S
S
ETTING
ETTING
ETTING
ETTING
ETTING
R
R
R
R
R
ECORD
ECORD
ECORD
ECORD
ECORD
This manual contains commissioning sheets (Page
D.11) of essential information that should be
completed by the commissioning engineer with
individual details of the burner. These details
should be verified periodically and changed as
adjustments occur.
SSSSS
AFETY
AFETY
AFETY
AFETY
AFETY
IIt is essential that commissioning be undertaken
only by suitably qualified and experienced
personnel. In the case of P Series Burners,
commissioning engineers should be experienced
in commissioning forced draught, fully modulating
oil burners.
Nu-way can accept no responsibility for
consequential loss, damage or injury, which results
from a failure to follow the commissioning
instructions provided or from commissioning
procedures being undertaken by unqualified
personnel.
It is the commissioning engineer’s responsibility
to ensure that all settings are in accordance with
the appropriate local standards and applicable
codes of practice.
EEEEE
MERGENCY
MERGENCY
MERGENCY
MERGENCY
MERGENCY
I
I
I
I
I
NSTRUCTIONS
NSTRUCTIONS
NSTRUCTIONS
NSTRUCTIONS
NSTRUCTIONS
P Series Burners are designed and constructed to
meet all applicable European Directives.
When used in accordance with the instructions
provided, P Series Burners are unlikely to produce
a hazardous condition. If, however, such a
condition should arise in connection with the
burner, the appliance or any instrument, machine
or service in the vicinity of the burner, the
FUEL
AND ELECTRICITY SUPPLIES SHALL BE
ISOLATED IMMEDIATELY
and they shall remain
isolated until the fault has been identified and
rectified.
IIIII
NSPECTION
NSPECTION
NSPECTION
NSPECTION
NSPECTION
Before commissioning is started it is important to:
-
Check that the electrical wiring is complete
and complies with all applicable Codes and
Standards.
-
Ensure that the fuses are fitted and are of the
correct ratings.
-
Check electrical earthing.
-
Verify that the oil pipework is correctly sized
and that it has been checked for leakage.
-
Check that the appropriate modulating
detector which is supplied loose with each
burner, is fitted correctly to the appliance.
(Technical Specification Pages C.2).
-
Make all personnel involved in the
commissioning aware of the location of the
emergency oil and electricity isolation points.
-
Check that the appliance's ventilation and
flueing arrangements are adequate.
-
Ensure that any warning notices appropriate
to the commissioning procedure are in
position.
-
Ensure that all necessary tools and test
equipment are available and ready for use.
Essential items include temperature
measuring instruments for measuring flue gas
and appliance water temperatures, and a
means of analysing the flue products for
carbon dioxide (CO
2
), oxygen (O
2
), carbon
monoxide (CO) and smoke.
-
Check that all relevant documentation is
available, including, where appropriate:
-
The agreed plant performance
specification.
-
Plant drawings and pipework layouts.
-
Electrical logic and wiring diagrams.
-
Certificates confirming satisfactory
completion of procedures such as
soundness testing, purging and
electrical safety tests.
-
Commissioning, operating, emergency
shutdown and maintenance
instructions for the plant.
-
Establish that the operation of plant other
than that being commissioned will not have
an adverse effect on the operation of the
plant to be commissioned, and similarly, that
the operation of the plant to be
commissioned will not have an adverse effect
on other plant.
-
Confirm that the operation of adjacent plant
and machinery will not constitute a hazard
to the personnel involved in commissioning.
-
Establish that the appliance is in an
appropriate and safe condition to be fired;
for example, that there is water in the boiler.
-
Set the appliance controls to call for heat.
Содержание PO160
Страница 5: ...Page B 1 PO Series General Information GENERAL INFORMATION ...
Страница 14: ...Page B 9 PO Series General Information ...
Страница 15: ...PO Series General Information Page B 10 AAD PFinal B_Gen PO B_Gen pmd 250504A ...
Страница 16: ...Page C 1 PO Series Technical Specification TECHNICAL SPECIFICATION ...
Страница 24: ...Page C 9 PO Series Technical Specification O O O O OIL IL IL IL IL P P P P PUMPS UMPS UMPS UMPS UMPS ...
Страница 34: ...Page C 19 PO Series Technical Specification ...
Страница 35: ...PO Series Technical Specification Page C 20 AAD PFinal C_Tech Po RWF40 C_Tech pmd 250504A ...
Страница 36: ...Page D 1 P Series Commissioning COMMISSIONING ...
Страница 42: ...Page D 7 P Series Commissioning ...
Страница 44: ...Page D 9 P Series Commissioning AAD PFinal C_Tech Po RWF40 D_Comm pmd 250504A ...
Страница 45: ...P Series Page 10 ...
Страница 46: ...Page E 1 PO Series Operation And Maintenance E OPERATION AND MAINTENANCE ...
Страница 51: ...PO Series Operation And Maintenance Page E 6 ...
Страница 52: ...Page E 7 PO Series Operation And Maintenance ...
Страница 53: ...PO Series Operation And Maintenance Page E 8 N N N N NOTES OTES OTES OTES OTES ...
Страница 54: ...Page E 9 PO Series Operation And Maintenance N N N N NOTES OTES OTES OTES OTES ...
Страница 55: ...PO Series Operation And Maintenance Page E 10 N N N N NOTES OTES OTES OTES OTES ...