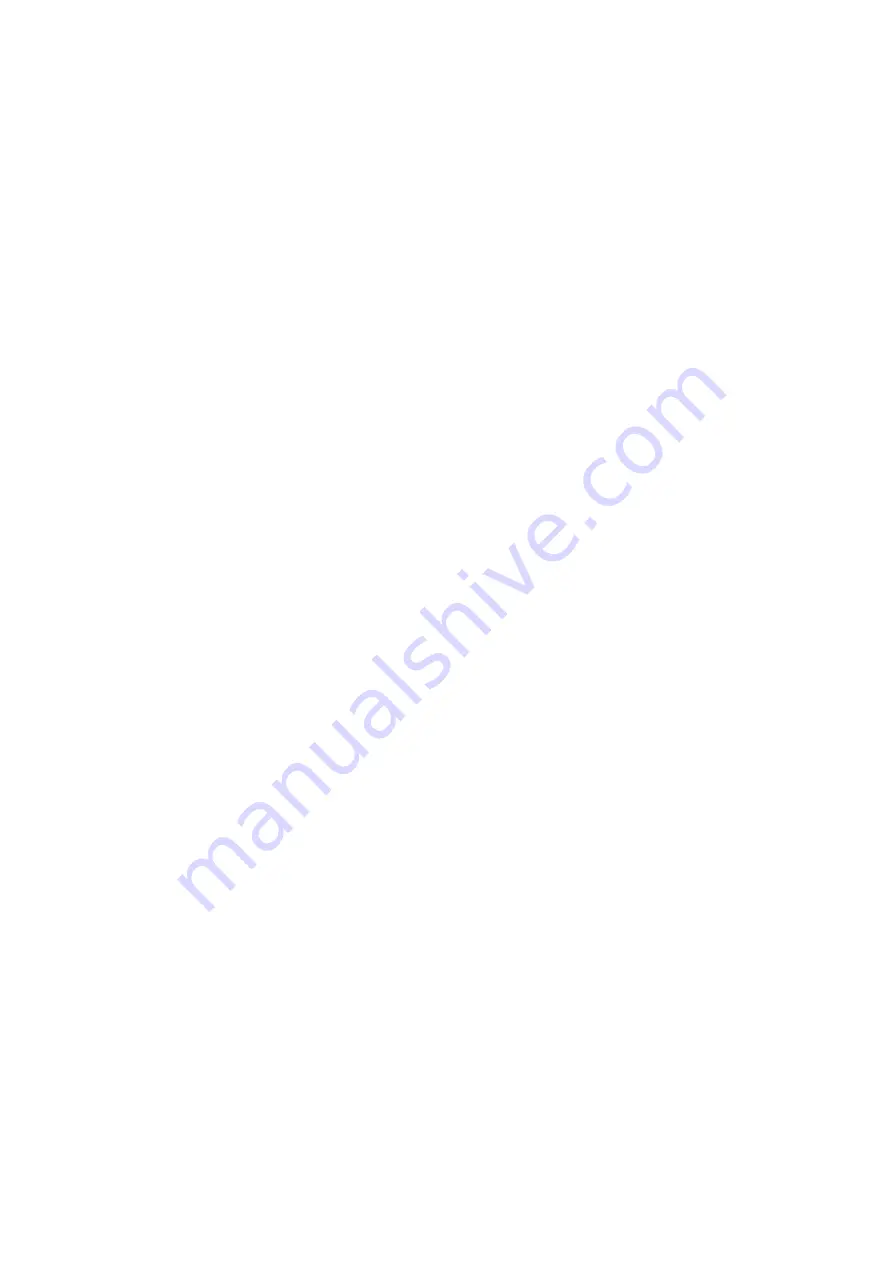
TEC-B-01 User Manual
____________________________________________________________________________________________________________________________
__________________________________________________________________________________
version 1.1
page 32
The proportional gain of the clamp system can be calculated as follows (Froehr, 1985; Polder, 1984):
K = C
m
/ 4 * T
e
Linear optimum (LO), aperiodic response, no overshoot
K = C
m
/ 2 * T
e
Modulus optimum (MO or AVO, respectively), 4% overshoot, fastest rise time
The optimal gain for a VC experiment is in between these two values. The overshoot can be reduced
by low-pass filtering of the command pulse.
The speed of response of the clamp in case of the modulus optimum can be calculated as:
T
r
= 4.7 * T
e
, T
s
= 8.4 * T
e
with
T
r
- time until the membrane potential reaches for the first time 100% of the command pulse
T
s
- time to reach steady state within a tolerance of 2%.
T
s
is roughly the duration of the capacitive transient. For a system with dampened overshoot
T
r
approaches T
s
.
From these formulas, it is clear that the performance of the clamp is determined by T
e
. T
e
is
determined by the time constant of the current injecting electrode i.e. by the electrode resistance, stray
capacities, cable capacities etc. Shielded cables have capacities of 60 - 110 pF / m, connectors and
pipette holders add a few picofarads. The potential electrode is equipped with a driven shield and a
capacity compensation circuit. Therefore, this time constant is always much smaller than the time
constant associated with the current electrode. The time constants of the operational amplifiers are
small and can be neglected.
Example
A cable of 10 cm has a capacity of approximately 10 pF, with the stray capacities in the headstage and
an electrode resistance of 1 M
(cell model). This gives a time constant of 10 – 30 µs (corner
frequencies of 5 – 15 kHz). With C
m
= 100 nF and T
e
= 20 µs (8 kHz bandwidth), the gain can be
calculated as:
LO: K = 1.25 mA / V
MO: K = 2.5 mA / V
The standard TEC current source has a calibration of 10 µA / V. This means that the gain stages
related to the GAIN control on the front panel must provide a gain between 125-250. In the TEC
system the gain amplifier is composed of two stages: x10 (fix) and 1 - 100 (variable). The maximum
gain of the variable gain stage can be set with an internal trim potentiometer.
If a command step of 150 mV is applied, the output of the first stage is 1.5V, while the second stage
goes into saturation if the gain values calculated above are used. Therefore, the capacitive transients
will have large nonlinear components.
A response with no saturation effects is obtainable only with command signals below 100 mV. With
larger membrane capacities the saturation effects start even earlier, because a higher gain is required.
In this situation, systems with higher output compliance and / or headstage with x2, x5 or x10 ranges
must be used to improve clamp response. In this case the saturation effect of the gain amplifier is
avoided (Polder and Houamed, 1994; Greeff and Polder, 1997; Polder et al., 1997).