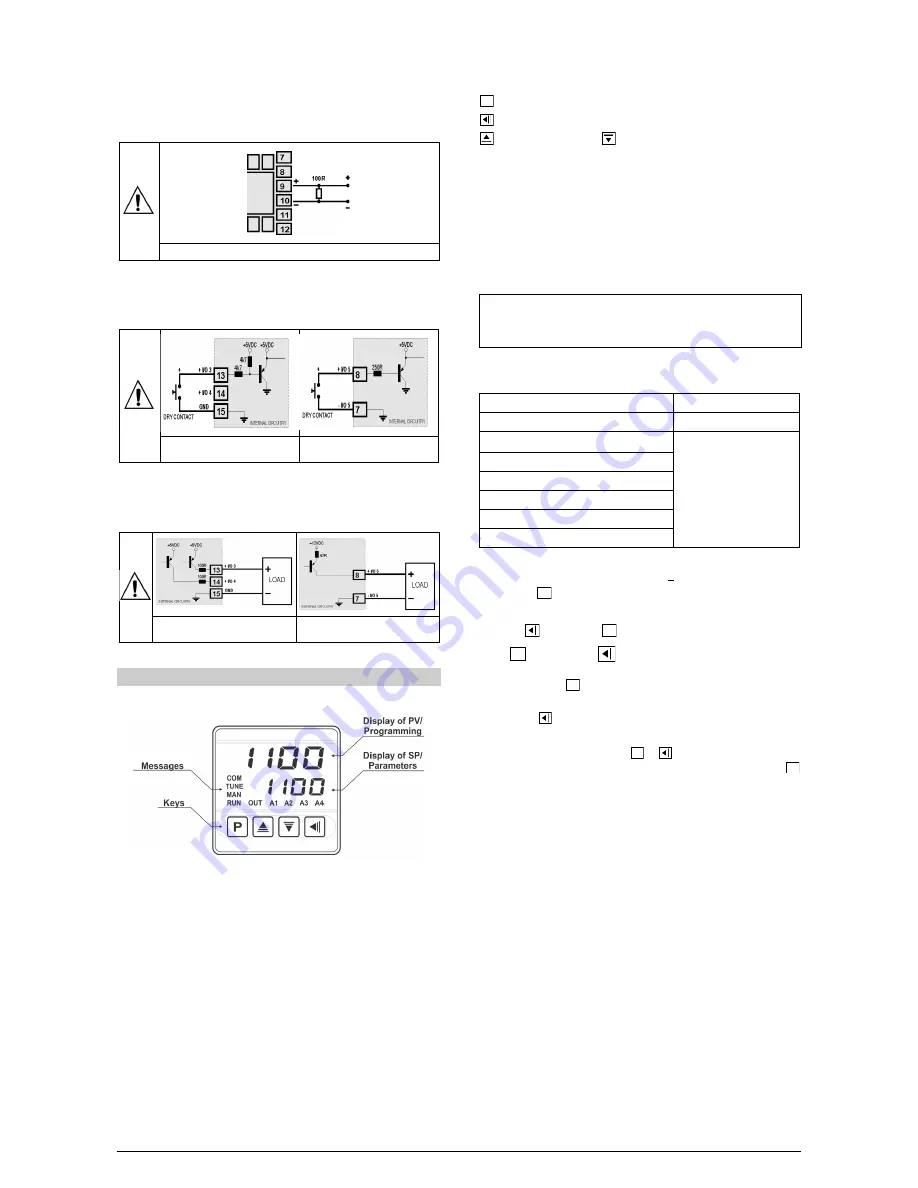
N1100 Controller
NOVUS AUTOMATION
5/11
Remote Setpoint
Feature available in the controller's terminals 9 and 10. When the
Remote SP input signal is 0-20 mA or 4-20 mA, an external
100
Ω
shunt resistor of must be connected to terminals 9 and 10 as
indicated in Figure 4c.
Figure 4c – Connection for remote SP
Digital Input Connections
Figures 5a and 5b show switches (Dry Contact) driving I/O3 (or
I/O4) and I/O5.
Figure 5a – I/O3 or I/O4 as Digital
Input
Figure 5b – I/O5 as Digital Input
Connection of Outputs
The I/O channels, when configured as outputs, must have their load
limit capacities observed, according to the product specifications.
Figure 6a – I/O3 or I/O4 with output
pulse for SSR.
Figure 6b – I/O5 with output pulse
for SSR.
OPERATION
The controller's front panel, with its parts, can be seen in the Figure 7:
Figure 7 - Identification of the parts referring to the front panel
Display of PV/Programming: Displays the current value of PV
(Process Variable). When in configuration mode, it shows the
parameters names.
Display of SP/Parameters: Displays the value of SP (Setpoint).
When in configuration mode, it shows the parameters values.
COM indicator: Flashes to indicate communication activity in the
RS485 interface.
TUNE indicator: Stays on while the controller is in tuning process.
MAN indicator: Signals that the controller is in the manual control
mode.
RUN indicator: Indicates that the controller is active, with the control
output and alarms enabled.
OUT indicator: For relay or pulse control output; it reflects the actual
state of the output. If an analog output is assigned for control (0-20
mA or 4-20 mA), the OUT indicator lights continuously.
A1, A2, A3 and A4 indicators: signalize the occurrence of alarm
situation.
P
P Key used to walk through the menu parameters.
Back Key: used to retrocede parameters.
Increment key and
- Decrement key: allow altering the
values of the parameters.
When the controller is powered on, its firmware version is presented
for 3 seconds, after which the controller starts normal operation. The
values of PV and SP are displayed and the outputs are enabled.
In order to operate appropriately, the controller needs a configuration
that is the definition of each one of the several parameters presented
by the controller. The user must be aware of the importance of each
parameter and for each one determine a valid condition or a valid
value.
Note: Since many parameters depend on the input type chosen, it
is recommended that the parameter
TYPE
be the first one to be
configured.
The parameters are grouped in levels according to their functionality
and operation easiness. The 7 levels of parameters are:
LEVEL
ACCESS
1- Operation
Free access
2-
Tuning
Reserved access
3- Programs
4- Alarm
5- Scale
6- I/Os
7- Calibration
Tabele5 – Cycles of Parameters
The parameters in the operation level (1
st
level) are easily accessed
through the
P
key. The access deeper levels use the combination
of Keys:
(BACK) and
P
(PROG) pressed simultaneously
Press
to advance or
to retrocede parameters within a level.
At the end of each level, the controller returns to the operation level.
Keep pressing the
P
key to move fast forward in the level.
Alternatively, the controller returns to the operation level after
pressing the key for 3 seconds.
All configuration parameters are stored in protected memory. The
values are saved when the keys or are pressed after changing
a parameter value. The value of SP is saved upon pressing the
key or every 25 seconds.
P
P
P