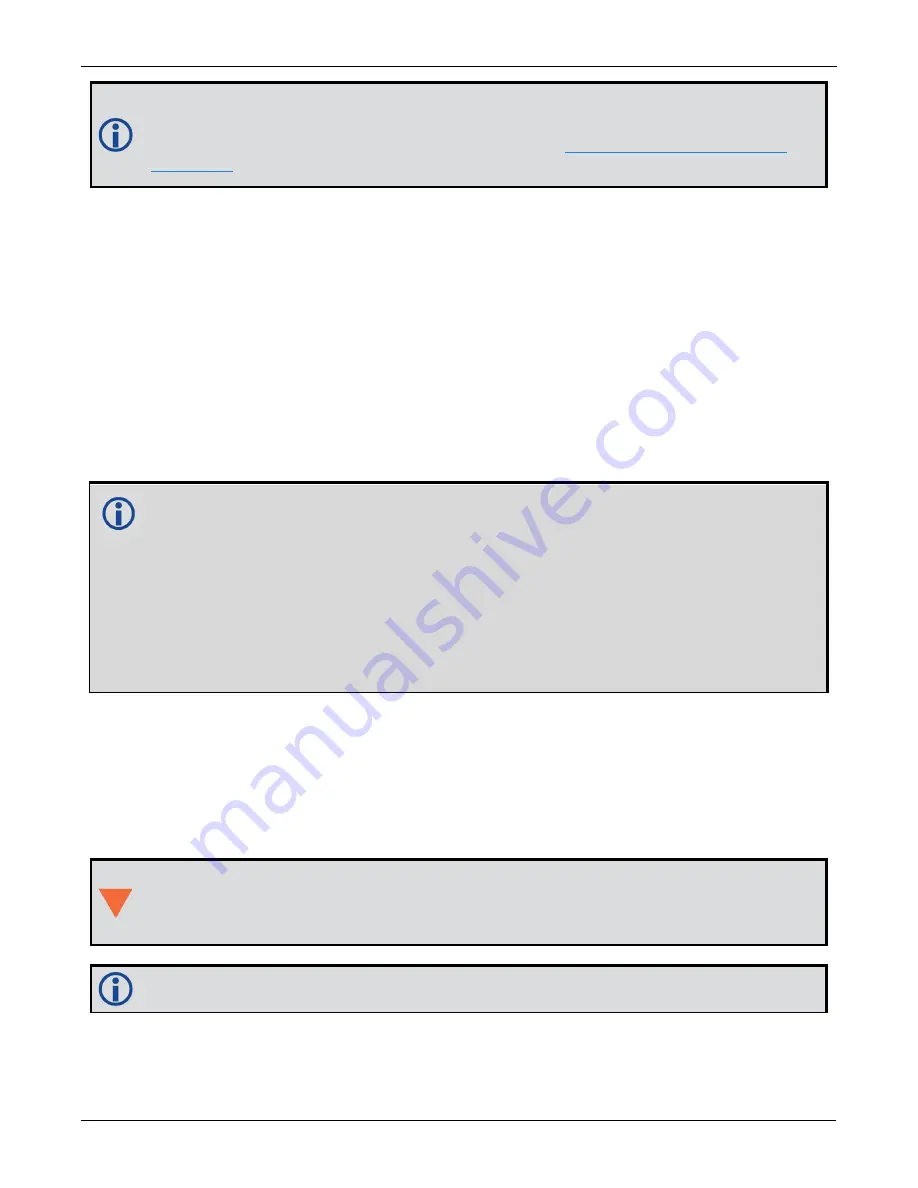
Chapter 2 SPAN Installation
OEM7 SPAN Installation and Operation User Manual v14
34
If a short circuit or other problem causes an overload of the current supplied to the antenna, the receiver
hardware shuts down the power supplied to the antenna. To restore power, power cycle the receiver.
The Receiver Status word, available in the
RXSTATUS
log (see
), provides more information about the cause of the problem.
2.1.4 Mount the IMU
Mount the IMU in a fixed location where the distance from the IMU to the GNSS antenna phase center is con-
stant. Ensure that the orientation with respect to the vehicle and antenna is also constant.
For attitude output to be meaningful, the IMU should be mounted such that the positive Z-axis marked on the
IMU enclosure points up and the Y-axis points forward through the front of the vehicle, in the direction of track. If
the IMU is not mounted in this orientation, a rotational offset must be applied. See
for more information.
Also, it is important to measure the distance from the IMU to the antenna (the Antenna Lever Arm), on the first
usage, on the axis defined on the IMU enclosure. See
on page 101. See also
on page 134 for dimensional drawings of the IMU enclosures.
Ensure the IMU cannot move due to dynamics and that the distance and relative direction between the antenna
and the IMU is fixed. See
SPAN Configuration for Receiver Cards
The closer the antenna is to the IMU, particularly in the horizontal plane, the more accurate the position
solution.
Also, your measurements entered using the
SETINSTRANSLATION
command must be as accurate
as possible, or at least more accurate than the GNSS positions being used.
For example, a 10 cm
error in recording the antenna offset will result in at least a 10 cm error in the output.
Millimeter accuracy is preferred.
The offset from the IMU to the antenna, and/or a user point device, must remain constant especially for
RTK or DGPS data. Ensure the IMU, antenna and user point device are bolted in one position perhaps
by using a custom bracket.
Securing the IMU Enclosure
The IMU Enclosure (IMU-ISA-100C, IMU-ENC-LN200, IMU-HG1900 and IMU-µIMU-IC) can be secured dir-
ectly to the mounting surface or can be secured using the IMU Enclosure Mounting Plate.
To secure the IMU Enclosure directly to the mounting surface, use four M6 screws that pass through the mount-
ing surface and into the bottom of the IMU Enclosure. For the location and spacing of the mounting holes, refer to
the mechanical drawings of the IMU in
The optimal screw penetration into the IMU Enclosure mounting holes is 5.0 to 6.0 mm deep. When
selecting screws for mounting the IMU Enclosure, ensure the screw penetration does not exceed 6
mm. Using excessively long screws can damage the IMU Enclosure.
The mounting screws should be torqued to 42 to 45 in-lbs.
For information about securing the IMU Enclosure using the mounting plate, refer to