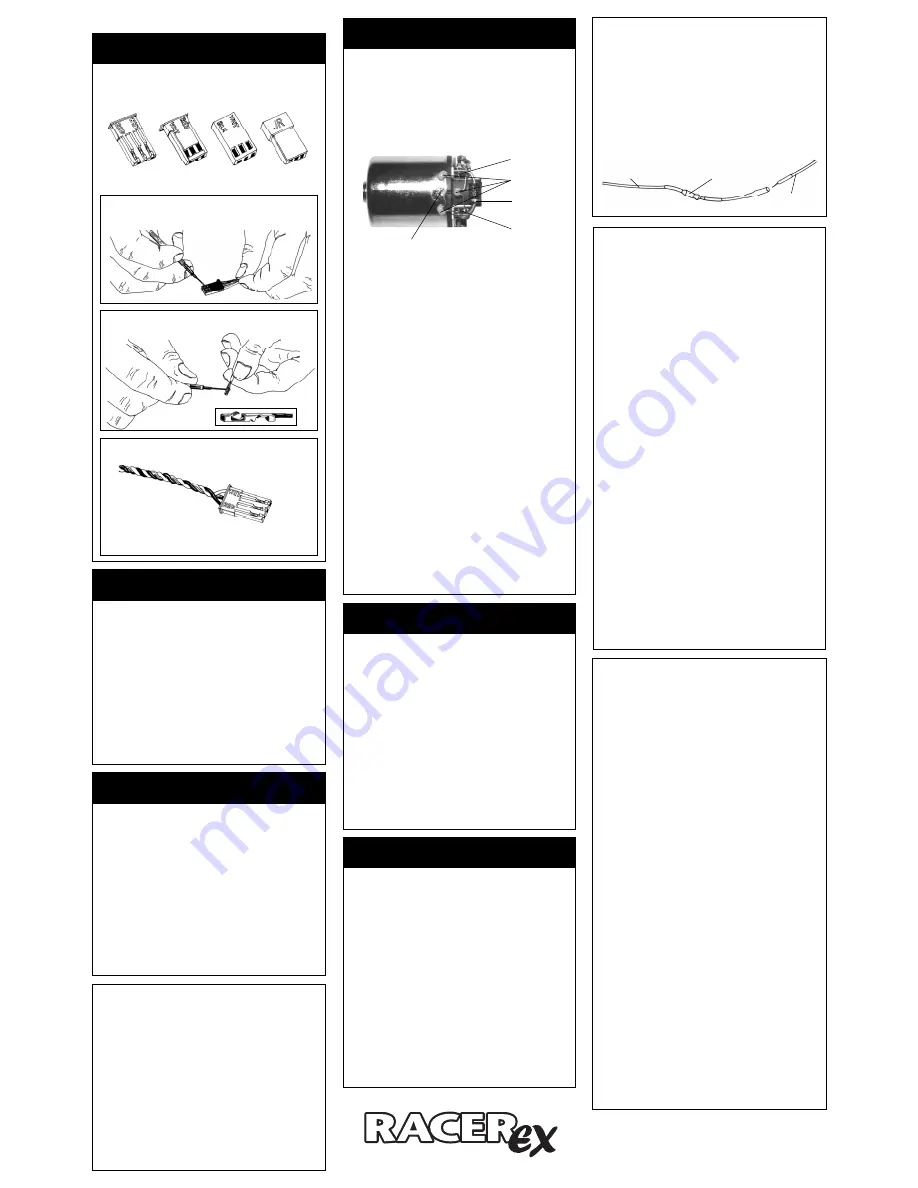
DETAILED INSTRUCTIONS
(STEPS 1-6)
(Refer to photos on front page)
USING A RECEIVER BATTERY PACK
The Racer-EX does not require an external receiver battery pack
for most racing situations. Built-in Radio Priority Circuitry™
provides complete control of the steering servo even after the
main battery pack has "dumped" and can no longer provide the
power required to operate the motor. However, applications
using multiple high-powered servos, and/or main battery packs
with 8 or more cells require the use of an external receiver
battery pack to prevent overloading of the ESC’s voltage
regulator. Failure to use a receiver battery pack in these
applications may result in damage to the voltage regulator and
will void the product warranty.
1. Plug an external 5-cell nickel cadmium (1.2 VDC/cell) re-
ceiver battery pack into the battery slot of the receiver.
2. Leave the ESC’s ON/OFF switch in the OFF position. This
switch is not used with this configuration.
3. Use the ON/OFF switch on the external receiver battery
pack to turn the system power on and off.
STEP 5
TRANSMITTER ADJUSTMENTS
For proper ESC operation, the basic transmitter throttle adjust-
ments are:
HIGH ATV, EPA
—Controls the amount of throw from neutral
to full throttle.
Set to maximum setting.
LOW ATV/EPA/ATL
—Controls the amount of throw from
neutral to full brakes.
Set to maximum setting.
EXP
or
EXPO
—Controls the linearity of the throttle channel.
Set to zero or middle setting
.
SUB TRIM
—Usually used to center a servo.
Set to zero or
middle setting
.
TH TRIM or COAST BRAKE
—Controls
coast brakes of the ESC.
Set it to middle setting.
MECHANICAL ADJUSTMENT
—Adjusts throw of throttle trig-
ger.
Set the throw for 2/3 throttle, 1/3 brake.
THROTTLE REVERSING SWITCH
—
Set in either position.
Do
not change the setting after ESC Set-Up.
See ONE-TOUCH SET-UP NOTES on front page
If the factory-installed Futaba J style plug installed on the ESC is
not compatible with your receiver, follow Figures 1-3 to change
the input plug. The Novak Input Plug System
TM
will convert the
ESC's input plug for use with Airtronics, KO, Kyosho, & JR radios.
STEP 1
CHANGING THE INPUT PLUG
Airtronics (A)
KO
Kyosho (KYO)
JR*
*JR plug can be used in place of Airtronics "Z" Connector
FIGURE 3
Insert each pin into the correct plug slot. Each
pin should "click" into place.
CAUTION
Improper installation of these wires may cause
damage to the receiver, servo, and ESC.
0.1
µ
F Capacitors
Negative (-)
motor tab
Positive (+)
motor tab
Ground*
Schottky diode,
silver stripe
closest to (+).
1. INSTALLING MOTOR CAPACITORS
Motors generate ra-
dio noise that can cause radio problems.
Capacitors must
be used at all times on every motor to prevent damage
to the ESC.
Solder the included three 0.1
µ
F, 50 V, non-polarized, ce-
ramic capacitors between:
•
POSITIVE
(+) motor tab &
NEGATIVE
(-) motor tab.
•
POSITIVE
(+) motor tab &
GROUND
tab*.
•
NEGATIVE
(-) motor tab &
GROUND
tab*.
Extra 0.1
µ
F capacitors are available in Novak kit #5620
Extra Schottky diodes are available in Novak kit #5640
2. INSTALLING THE SCHOTTKY DIODE
Solder the included
Schottky diode between
POSITIVE
(+) motor tab &
NEGA-
TIVE
(-) motor tab. The diode is polarized and must be
installed with the silver stripe (+) closest to the POSITIVE
motor tab.
3. PLUGGING INTO THE RECEIVER
Plug the ESC into
CHANNEL 2 (or THROTTLE CHANNEL) of the receiver. Plug
the servo into CHANNEL 1. Nothing should be plugged into
the BATTERY CHANNEL.
4. BATTERY & MOTOR CONNECTIONS
Solder the included
extra piece of red wire from BATTERY POSITIVE (+) to
MOTOR POSITIVE (+).
Splice the ESC red wire into the extra red wire and insulate
the solder joint with heat shrink tubing.
Solder the ESC blue wire to MOTOR NEGATIVE (-).
Solder the ESC Black wire to BATTERY NEGATIVE (-).
5.
USING PLUGS FOR BATTERY & MOTOR CONNECTION
High-quality/low-resistance connector plugs, such as
Dean’s Ultra Plugs, can also be used to connect the
Racer-EX. While these connectors make component
changes quick and easy, the connection will never have
the low resistance of a good solder joint.
Use connectors that can not be connected backwards,
as this will damage the ESC and void the warranty.
It is good practice to use a female connector on battery
to keep from short-circuiting on conductive surfaces.
If you use connector plugs for battery and motor, use a
male connector on the ESC battery wires and a female
connector on the motor wires. Doing this, will avoid
plugging the battery into the motor output of the ESC.
STEP 4
HOOK-UP INSTRUCTIONS
*Stock motors do not have ground tabs, solder to the can of the motor.
STEP 3
MOUNTING INSTRUCTIONS
1. MOUNTING THE ESC
Use the included mounting tape to
mount the ESC in a location that provides maximum airflow
through the heat sinks. For off-road cars, the ESC should be
mounted on the chassis.
Mount the ON/OFF switch in a convenient place with a
piece of mounting tape or screw.
2. MOUNTING THE RECEIVER
To minimize glitching, mount
the receiver and antenna away from the ESC, motor, servo,
power wires, or any large piece of metal (such as a chassis)
or graphite.
If you must mount the receiver on the chassis, mount it on its
side with the crystal & antenna as far above the chassis as
possible to reduce the chances of radio interference.
Mount the antenna as close to the receiver as possible.
Follow the receiver manufacturer’s instructions for recom-
mended antenna routing and mounting.
STEP 2
HEAT SINK INSTALLATION
The included heat sinks will make the ESC run cooler and faster
when they are properly installed.
1. INSTALLING THE LARGE HEAT SINK
Place the ESC on a flat
surface and press the large heat sink onto the row of 5
transistors on the left side of the ESC.
2. INSTALLING THE SMALL HEAT SINK
Press the small heat
sink onto the row of 3 transistors on the right side of ESC.
The heat sinks should press onto the transistors with a
snug fit. If they are installed upside-down or shifted off-
center, the fit will be either too tight or too loose.
To prevent damage to the components under the transistors,
never use a vise or pliers to force the heat sinks onto the
transistors
. Do not use glue to attach heat sinks.
To prevent short-circuits,
never allow the heat sinks to
touch each other or any exposed metal or graphite.
The locking tab must not
extend outside the
plastic plug housing.
(Airtronics plug shown)
WHT
=
White wire (signal)
BLK
=
Black wire (negative)
RED
=
Red wire (positive)
FIGURE 1
Using a small standard screwdriver, press each
of the three metal locking tabs and remove each pin from
the plug.
FIGURE 2
Using the screwdriver, carefully bend each
of the metal locking tabs to the angle shown.
STEP 6
SPEED CONTROL SET-UP
Speed control should be connected to receiver and to a
charged battery pack, and the transmitter adjusted.
1. TURN ON THE TRANSMITTER
2. TURN ON THE SPEED CONTROL
3. PRESS AND HOLD SPEED CONTROL’S SET BUTTON
With transmitter throttle at neutral, press and hold the
ESC
SET
button until the status
LED
turns solid red
.
4. RELEASE ESC SET BUTTON WHEN LED IS RED
5. PULL TRANSMITTER TRIGGER TO FULL THROTTLE
Hold it there until the status
LED
turns solid green
.
NOTE: The motor will not run during programming even if
it is connected to the speed control.
6. PUSH TRANSMITTER THROTTLE TO FULL-BRAKE
Hold it there until the status
LED
blinks green
.
7. RETURN TRANSMITTER THROTTLE TO NEUTRAL
Status
LED
will
turn solid red
, indicating that throttle is
at neutral and proper programming has been completed.
Speed control is programmed & ready to race!
If transmitter settings are changed, it will be necessary to com-
plete the programming sequence once again.
If you experience any problems during programming, turn off
the speed control and repeat programming.
©1998 Novak Electronics, Inc. • All Rights Reserved
No part of these operating instructions may be reproduced without the written permission
of Novak Electronics, Inc.
All Novak ESCs are designed and manufactured in the U.S.A.
Racer-EX ESC, One-Touch Set-Up, Solid State RVP, Radio Priority Circuitry, CLC II, and Input
Plug System are trademarks of Novak Electronics, Inc.
Printed in the U.S.A. 6/98
IM-1750-2
FET SERVO CONNECTION
The Racer-EX is wired for connecting a FET Servo. This type of
servo requires a fourth wire connection. The fourth wire from
the servo is connected to the
small, blue 24-gauge silicone
wire
coming out of the ESC. In the Racer-EX, this wire supplies
6 volts of power to the servo and is controlled by the speed
control’s ON/OFF switch.
NOTE: Do not allow the blue FET servo wire to come in contact
with the chassis or battery terminal, as this may damage the
power switch, switch wires and the speed control’s PC board,
consequently voiding the product warranty.
If you experience radio glitching with the installation of the FET
servo, try installing a 10
µ
H inductor (usually supplied with
servo) in series with the blue wire.
Blue Wire from
speed control
10
µ
H inductor
Wire from
FET servo
TROUBLE-SHOOTING GUIDE
ESC Will Not Program Properly
• Too little transmitter throw––Increase ATV/EPA setting.
• Make sure ESC is plugged into the throttle channel of
receiver. Check throttle channel operation with a servo.
• ESC SET button not held long enough––Press and hold
SET button until status LED turns solid red.
• Make sure metal sockets on Input Harness are locked in
place in plastic plug.
• Check to be sure transmitter and receiver crystals are a
matched set
• Possible transmitter, receiver, or crystal problem.
Steering Channel Works But Motor Will Not Run
[Status
LED
is
solid RED
at all throttle positions]
• No signal from receiver––Make sure speed control is
plugged into throttle channel of receiver. Check throttle
channel operation with a servo. Check the wiring color
sequence & metal socket insertion of receiver harness.
Steering Channel Works But Motor Will Not Run
[Status
LED
is
RED at neutral
/
GREEN at full
throttle]
• Check motor connections. Check motor and brushes.
• Not programmed––Repeat programming.
• Thermal Shutdown––Allow to cool/Check for adequate
airflow through heat sinks.
• Check wiring and connections––Check operation of sys-
tem without speed control.
Receiver Glitches/Throttle Stutters During Acceleration
• Motor capacitors broken or missing––Refer to Step 4.
• Receiver or antenna too close to speed control, power
wires, battery, or motor––Refer to Step 2.
• Bad connections––Check wiring and connectors.
• Graphite or Aluminum Chassis––Refer to Step 2.
• Excessive current to motor––Use a milder motor or a
smaller pinion gear.
ESC Is Melted Or Burnt/ESC Runs With Switch Off
• Internal damage––Refer to Service Procedures.
*For more help call our Customer Service Department.
SERVICE PROCEDURES
Before sending your speed control in for service, review the
Trouble-Shooting Guide and Instructions. The speed control
may appear to need service when other problems exist in
the system such as a problematic transmitter, servo, battery,
connectors or motor.
PLEASE NOTE:
Speed controls that operate normally
when received will be charged a minimum service fee
and return shipping costs.
WHAT TO SEND: Fill out all of the requested information on
the enclosed
ESC SERVICE CARD
and return it with your re-
ceiver. Service cards can also be downloaded from our
website at www.teamnovak.com.
WARRANTY WORK: For warranty service work, you MUST
CLAIM WARRANTY on the
ESC SERVICE CARD
and include a
valid, dated, cash register receipt, or an invoice from previ-
ous service work. If any warranty provisions have been
voided there will be a service charge.
SERVICE COSTS: Customer is responsible for service costs
(parts, labor and shipping/handling charges). ESCs are
returned UPS/COD CASH ONLY. See
ESC SERVICE CARD
for
other payment and shipping options.
ADDITIONAL NOTES:
• Hobby dealers/distributors are not authorized to replace
speed controls thought to be defective.
• If a hobby dealer sends your speed control for service, sub-
mit a completed
ESC SERVICE CARD
to the dealer and make
sure it is sent with the speed control.
• Novak Electronics, Inc. does not make any electronic com-
ponents (transistors, resistors, etc.) available for sale.
• To provide the most efficient service possible to our cus-
tomers, it is not our policy to contact customers by
phone or mail.
FOR SERVICE, SEND ESCs TO:
Novak Electronics, Inc.
Attn: Service Department
18910 Teller Ave., Irvine, CA. 92612 USA
CUSTOMER SERVICE HOURS (PST):
M-Th: 8am-5pm; F: 8am-4pm (Closed every other Friday)
(949) 833-8873 • FAX (949) 833-1631
Visit us at www.teamnovak.com