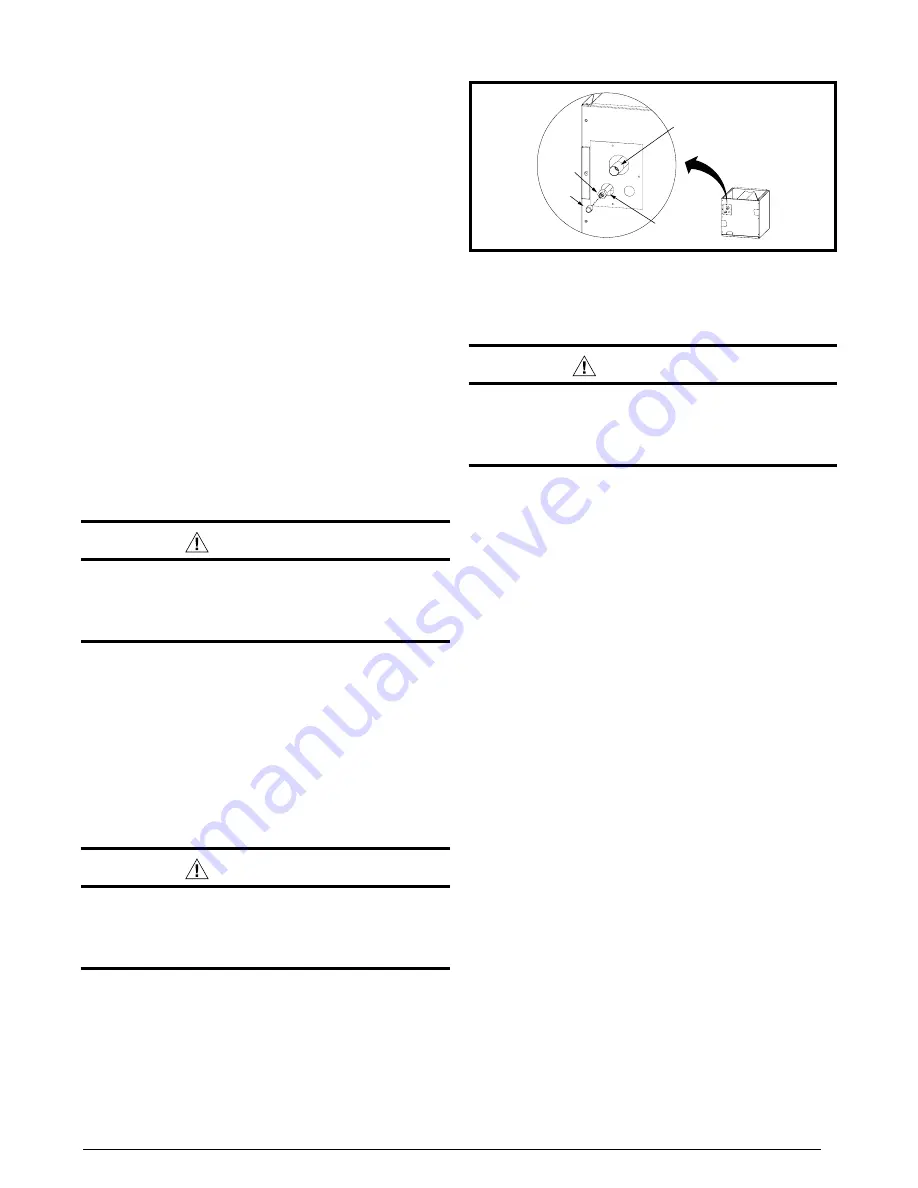
3
Suction
Line
Liquid
Line
Cap
Schrader
Valve
Figure 1. Suction & liquid line locations
1. Disconnect all electrical power to the furnace or air handler.
2. Remove system refrigerant per industry standard practices.
3. Disconnect and remove existing evaporator coil.
System Depressurization
1. Remove the cap (Figure 1) from the end of the liquid line.
2. Verify pressurization by depressing the Schrader valve
on the end of the liquid line. Listen for any escaping gas.
If there is no pressure, test the coil for leakage.
• If leakage is found, clearly mark the location of the leak
and return the coil to the distributor for processing.
• If no leaks are found, the coil may be installed.
3. Depress the valve to relieve all pressure from the coil.
4. Proceed to the appropriate lineset connection for
installations with factory installed orifice. See pages 4 - 5.
• Go to
Changing the Orifice
section if your installation
is with a different orifice.
• Go to
Installing a TXV kit
if your installation is equipped
with a TXV.
Changing the Orifice
NOte:
Before proceeding, perform steps 1 - 3 in the System
Depressurization section and confirm that the restrictor
orifice size meets the requirements outlined in the outdoor
unit installation manual. Factory supplied orifice sizes are
listed in Table 2 (page 4). If the orifice must be replaced,
follow steps 1 - 5.
CAUtiON:
to prevent damage to the unit or internal
components, it is recommended that two
wrenches be used when loosening or tightening
nuts. Do not over tighten!
1. Using two wrenches, loosen the nut and distributor body
as shown in Figure 2. Turn the assembly nut counter-clock-
wise until the orifice body halves are separated.
2. Insert a light-gauge wire hook between the distributor body
and the restrictor orifice while being careful not to scratch
either part. Carefully remove the restrictor orifice from the
distributor body. See Figure 3.
3. Check the actual size of the new orifice. The size is stamped
on its side. Do not use pin gauges to measure the orifice
diameter.
4. Insert the new orifice into the distributor body, rounded
end down. See Figure 4.
CAUtiON:
to prevent damage to the unit or internal
components, it is recommended that two
wrenches be used when loosening or tightening
nuts. Do not over tighten!
5. Realign the assembly nut on the distributor body and hand
tighten both components. Mark a line on both bodies and
then tighten an additional 1/4 turn using two wrenches. The
movement of the two lines will show how much the nut is
tightened. If a torque wrench is used, tighten to 10-12 ft.
lbs. or 14-16 Nm.
6. Proceed to the appropriate lineset connection section. See
pages 4 - 5.
Installing a TXV Kit
A separate TXV kit and C5 replacement tube kit are required.
See Tables 3 - 5 (page 5) for proper kit part numbers.
CAUtiON:
to prevent damage to the unit or internal
components, it is recommended that two
wrenches be used when loosening or tightening
nuts. Do not over tighten!
1. Using two wrenches, loosen the distributor and liquid line
body halves. Turn the assembly nut counter-clockwise.
2. Discard the removed liquid line.
3. Insert a light-gauge wire hook between the distributor body
and the restrictor orifice while being careful not to scratch
either part. Carefully remove the restrictor orifice from the
distributor body. See Figure 3.
4. Connect the distributor to the outlet side of the valve.
5. Braze the new liquid line from the C5 replacement tube
kit and liquid line stub & screen (included in TXV kit) with
dry nitrogen flowing through the joints.
IMPORTANT: Brazing operation should be performed
before connecting assembly to the TXV. This protects
the TXV from heat. Liquid nitrogen prevents internal
oxidation and scaling from occurring.
NOte:
The liquid line is sold separately, see Table 3 (page
5) for appropriate part number.
6. Connect the liquid line to the inlet side of the valve.
7. Realign the assembly nut on the distributor body and hand
tighten both components. Mark a line on both bodies and
then tighten an additional 1/4 turn using two wrenches. The
movement of the two lines will show how much the nut is
tightened. If a torque wrench is used, tighten to 10-12 ft.
lbs. or 14-16 Nm.
8. Using two wrenches, tighten both ends of the valve.
9. Secure the sensing bulb to the suction line using the clamp
supplied with the kit.
10. Wrap the bulb, clamp, and suction line together with tar
tape or other insulating material.
impOrtANt NOteS:
• The sensing bulb must be located flush against the
suction line for optimum heat transfer.
• Avoid attaching the sensing bulb to the lowest part of
the suction line where condensate may accumulate.
• Do not locate the sensing bulb on vertical sections of
the lineset.
• For horizontal lines, the bulb should not be located at
12 or 6 o’clock position of the suction line. the best
location is at 4 or 8 o’clock.