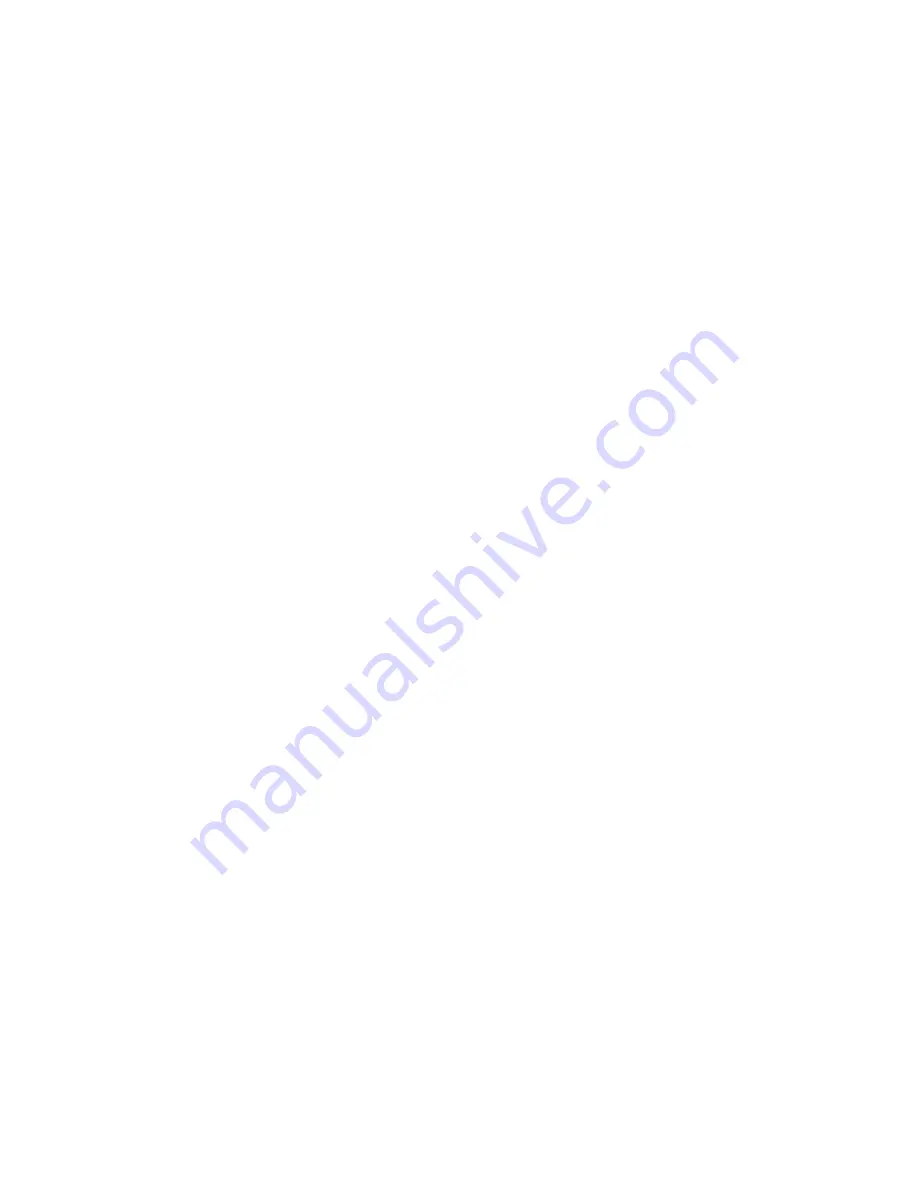
307UM0100_01 May 2016
PD17x User Manual
Page 15 of 31
5.2.2
Crosstalk
When two loop configurations are in close proximity, the magnetic fields of one can overlap and disturb the field of
another loop. This phenomenon, known as crosstalk, can cause false detects and detector lock-up.
Should the loops be connected to the same dual channel detector, crosstalk will not occur as sequential polling of the
loops takes place, resulting in only one loop being energised at a given time.
Crosstalk between adjacent loops operating from different detector modules can be eliminated by:
1.
Careful choice of operating frequency. The closer together the two loops, the further apart the frequencies of
operation must be.
2.
Separation between adjacent loops. Where possible a minimum spacing of 2 metres between loops should be
adhered to.
3.
Careful screening of feeder cables if they are routed together with other electrical cables. The screen must be
earthed at the detector end only.
4.
Running feeder cables in their own slots, separated by at least 300 mm.
For additional information on Crosstalk refer to the section “Crosstalk Prevention” in the DU100 Diagnostic Unit User
Manual Nortech Document No. 895UM0001.
For information about resolving Crosstalk refer to the “Theory of Application” section in Diagnostic Unit DU100 User
Manual Document No. 895UM0001.
5.2.3
Reinforcing
The existence of reinforced steel below the road surface has the effect of reducing the inductance, and therefore the
sensitivity of the loop detection system. Where reinforcing exists, 2 turns should be added to the normal loop, as
referred to in section 5.4.
The ideal minimum spacing between the loop and the cable and steel reinforcing is 150mm, although this is not
always practically possible. The slot depth should be kept as shallow as possible, taking care that no part of the loop or
the feeder remains exposed after the sealing compound has been applied.
5.3
Loop and Feeder Material Specification
Extensive studies have been undertaken over the years by various agencies around the world in order to ascertain the
optimum loop installation materials.
As an insulated conductor is a prerequisite PVC covered cable has been used for many years as a first choice, but tests
have shown that this is unsuitable for long term installations. The PVC tends to become porous with the result that
adjacent loops become electrically coupled to one another, with resultant crosstalk implications. Instability and
susceptibility to electrical interference can also result.
The insulation must withstand wear and abrasion from the shifting streets, moisture and attack by solvents and oils, as
well as withstand the heat of high temperature sealants.
Silicone insulated cable has emerged as one of the preferred insulation materials. Other insulation materials are rubber,
thermoplastic, synthetic polymer and cross linked polyethylene.
Stranded loop wire is preferred over solid wire due to its mechanical characteristics, a stranded wire is more likely to
survive bending and stretching over a solid wire.
A heavy gauge conductor is desirous in order to maintain the loop Q-factor. The loop and feeder should preferably
constitute a single length of insulated multi-stranded copper conductor, with no joints and the copper having a
minimum cross section 1.5 mm
2
. The feeder is twisted to minimise the effect of electrical noise.
Joints in the loop or feeder are not recommended. Where this is not possible, joints are to be soldered and terminated
in a waterproof junction box. This is extremely important for reliable detector performance. Other forms of joins such
as those available in kits, where the joint is properly sealed against moisture, are also permitted