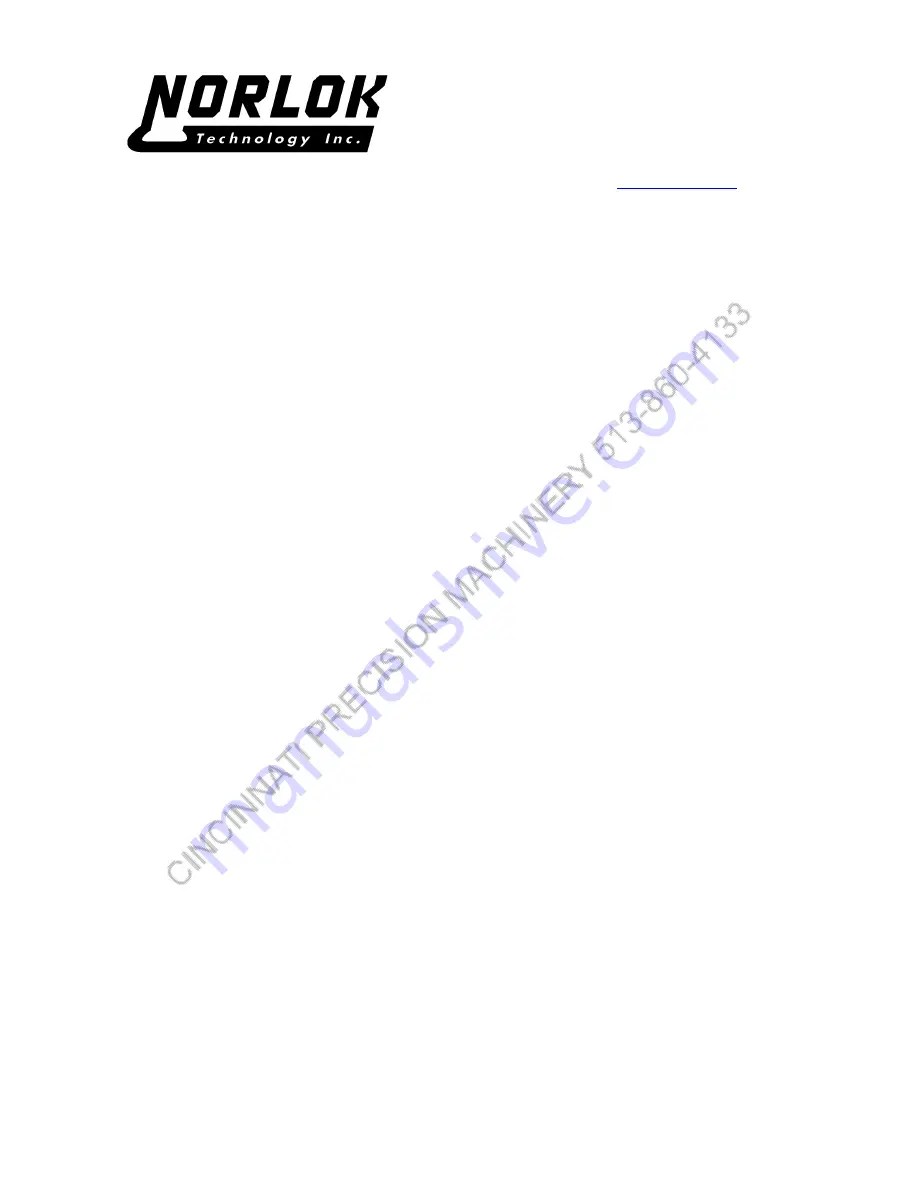
WARRANTY INFORMATION
Subject to the conditions below, and with the exception of punches and
dies, Norlok Technology Inc. ("Norlok") warrants to the first end user (the "Buyer")
that Norlok equipment and components are free from defects in material and
workmanship for one year from the date of purchase of the equipment or
components. Punches and dies are covered under the same warranty conditions
for a period of thirty days from purchase from Norlok Technology Inc.
Norlok will either repair, or replace defective components, including lowest transportation
costs, but not including installation or any similar charges, provided that;
1)
The buyer notifies Norlok in writing of the claimed defect within one year of the shipment
from the Norlok factory (thirty days in the case of punches and dies).
2)
Provides a complete explanation of the claimed defect, the application of the product, and
any other information as may be requested by Norlok.
3)
Returns the defective component to Norlok in accordance to Norlok's specific written
instructions and authorization obtained from Norlok prior to the return of the product.
4)
Norlok's inspection of the product confirms that the product was defective.
This warranty applies only if the product was;
a)
used in, and applied correctly under normal operating conditions and good engineering
practice,
b)
was installed, operated, and maintained in accordance with all instructions issued or
published by Norlok,
c)
was used within the stated pressure, and operating limitations published by Norlok,
d)
was not subject to abuse, misuse, or unauthorized modification.
THIS WARRANTY IS IN LIEU OF ALL OTHER WARRANTIES, EXPRESSED OR
IMPLIED, INCLUDING ANY IMPLIED WARRANTY OF MERCHANTABILITY OR FITNESS
FOR A PARTICULAR PURPOSE, not withstanding any disclosures to Norlok of the use for
which the product is to be put. The Buyer's SOLE AND EXCLUSIVE REMEDY on any
claim of any kind of loss or damage arising out of the use of Norlok equipment or
components shall be for the repair or replacement of any defective product as provided
herein.
IN NO EVENT SHALL NORLOK BE LIABLE FOR ANY SPECIAL,
INCIDENTAL OR CONSEQUENTIAL DAMAGES. There are no warranties expressed or
implied made by Norlok other than the warranty against defects in material and
workmanship set forth above, and Norlok neither assumes or authorizes any other person
or firm to assume for it any other obligations or liability.
26 ADAMS BOULEVARD
BRANTFORD, ON.
CANADA, N3S 7V2
Ph:
(519) 759 5896
Fx:
(519) 759 2948
ISO 9001 Registered
E-mail: nlmail @ norlok.com
Web:
www.norlok.com
Содержание Sure-Lok 24
Страница 7: ...SURELOK MANUAL 2002 6 ...
Страница 8: ...SURELOK MANUAL 2002 7 ...
Страница 9: ...SURELOK MANUAL 2002 8 ...
Страница 23: ...SURELOK MANUAL 2002 22 ...
Страница 28: ...SURELOK MANUAL 2002 27 ...