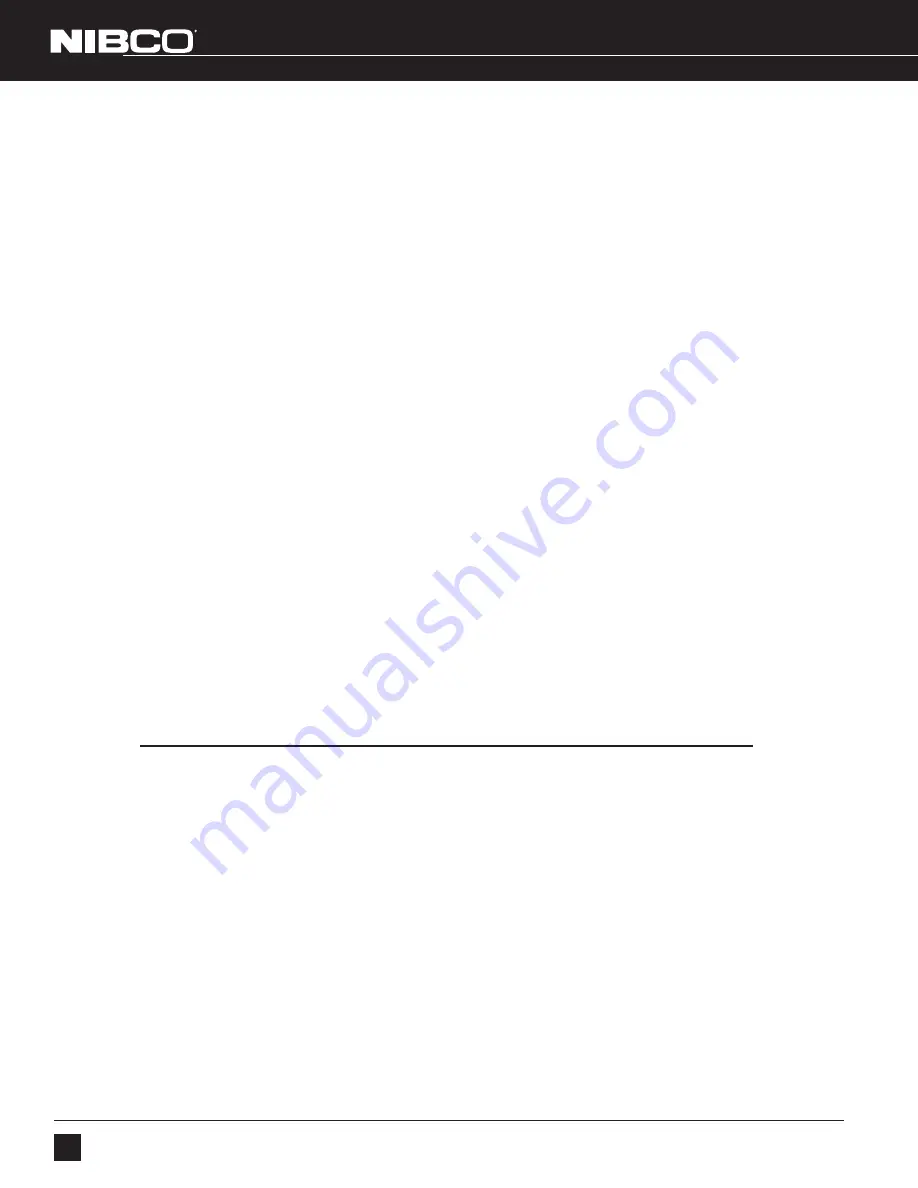
84
NIBCO INC. WORLD HEADQUARTERS • 1516 MIDDLEBURY ST. • ELKHART, IN 46516-4740 • USA • PH: 1.800.234.0227
TECH SERVICES PH: 1.888.446.4226 • FAX: 1.888.336.4226 • INTERNATIONAL OFFICE PH: +1.574.295.3327 • FAX: +1.574.295.3455
www.nibco.com
Visit our website for the most current information.
www.nibco.com
A H E A D O F T H E F L O W
®
PRESSURE TESTING:
NIBCO recommends the following leak testing procedures when installing NIBCO Press System with the leak detection feature. These test procedures allow
the installer to find un-pressed connections while the system is being tested under pressure.The uniquely designed EPDM o-ring allows fluids or gases to flow
past the seal and leak when the fitting has not yet been pressed. When the fitting has been pressed, the o-ring will create a water tight seal around the tube.
AIR LEAK TESTING:
1. Pressurize system up to 15 psi maximum using dry, oil free compressed air, carbon dioxide, or nitrogen.
2. Allow system pressure to stabilize for a minimum of 2 hours.
3. If system pressure has dropped, add more air to bring entire system up to 15 psi maximum. If system pressure increases above 15 psi, bleed off excess
pressure to ensure system is at a maximum pressure of 15 psi.
4. If the system pressure continues to drop, inspect all joints for un-pressed fittings. The NIBCO Press System press fittings with the leak detection feature
are designed to leak in an un-pressed condition.
5. Check all press joints for air leaks using a commercially available leak test solution or a soap and water mixture. Do not use a soap that contains Mineral
Spirits or a Hydrocarbon/ petroleum that might attack the EPDM O-rings.
6. Once the system has been confirmed to be leak free, pressure can be increased to the recommended working pressure to verify system integrity.
WATER LEAK TESTING:
1. Pressurize system up to 50 psi maximum using potable water.
2. Allow system pressure to stabilize for a minimum of 2 hours.
3. If system pressure has dropped, add more water to bring entire system up to 50 psi maximum. If system pressure increases above 50 psi, bleed off
excess pressure to ensure system is at a maximum pressure of 50 psi.
4. If the system pressure continues to drop, inspect all joints for un-pressed fittings. The NIBCO Press System press fittings with the leak detection feature are
designed to leak in an un-pressed condition.
5. Check all press joints for leaking water.
6. Once the system has been confirmed to be leak free, water pressure can be increased to the recommended working pressure to verify system integrity.
SYSTEM INTEGRITY TESTING*:
Once a system has been confirmed to be properly installed and no press connections have been left uncrimped
, the system is recommended for
testing up to the maximum non-shock working pressure of 200 psi hydrostatic.
NOTE: While NIBCO Press System products are tested to pressures as high as 600 psi, the product system rating limitation of 200 psi is in place to ensure a safety
factor of three-times proof-testing according to ASME B16.51 Copper and Copper Alloy Press-Connect Pressure Fittings.
SYSTEM INTEGRITY TESTING AT HIGHER PRESSURES*:
NIBCO Press System products can be tested at hydrostatic pressures higher than 200 CWP, not exceeding a maximum pressure of 300 psi hydrostatic for a
maximum test duration of 24 hours, when assembled and tested according to the methods prescribed above.
CAUTION:
These testing parameters and protocols apply only to NIBCO products as detailed above: NIBCO accepts no responsibility or liability for any other
manufacturer’s products that may be damaged as a result of such testing.
*System integrity testing applies to leak detect and non-leak detect fittings and valves.
NIBCO
®
Press System — Crimp Integrity Testing
Instructions for Fittings & Valves
Revised 2/28/2020