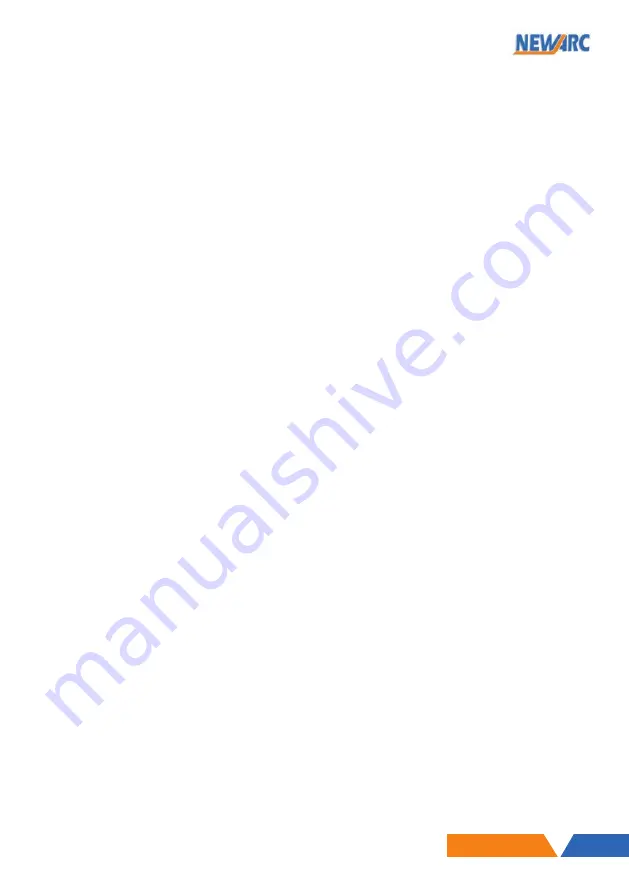
11
VIPER 2000
Gas Control
Gas pre-flow, the Viper 2000 provides pre and post timing of gas flow using an internal gas solenoid.
When the torch switch is operated for the first time there will be 0.25-second purge of shielding gas
before the contactor and arc ignition circuits are energized. This initial delay is to ensure that the argon
lines and welding torch are purged of air before welding commences.
NOTE!
For example, if the gas is already flowing after the end of a weld then both the contactor and
arc ignition circuits will energize immediately upon pressing the torch switch. If an arc is not struck
within 5 seconds of pressing the torch switch gas solenoid, contactor and arc ignition will be turned
off, releasing the torch switch will reset the sequence.
Gas post-flow, when the torch switch is released at the end of a weld the shielding gas will continue
to flow for approximately 15 seconds to allow an inert gas shield to be present whilst the weld cools
down. This prevents oxidization of the weld pool and contamination of the tungsten electrode.
Contactor
The internal contactor allows the welding current to be switched on and off by means of the torch
switch. If the tungsten electrode is inadvertently touched into the weld pool whilst welding then
the contactor will turn off the welding current. This reduces the possibility of tungsten inclusions
in the weld. To avoid further weld pool contamination during this period shielding gas coverage is
maintained until the torch switch is released.
Arc initiation
The arc ignition system used in the Viper 2000 displays a positive arc-striking characteristic over the full
input voltage range of the unit. This excellent striking characteristic is achieved by using state of the
art electronic techniques. As the arc ignition system does not require a spark gap for its operation it is
virtually maintenance free.