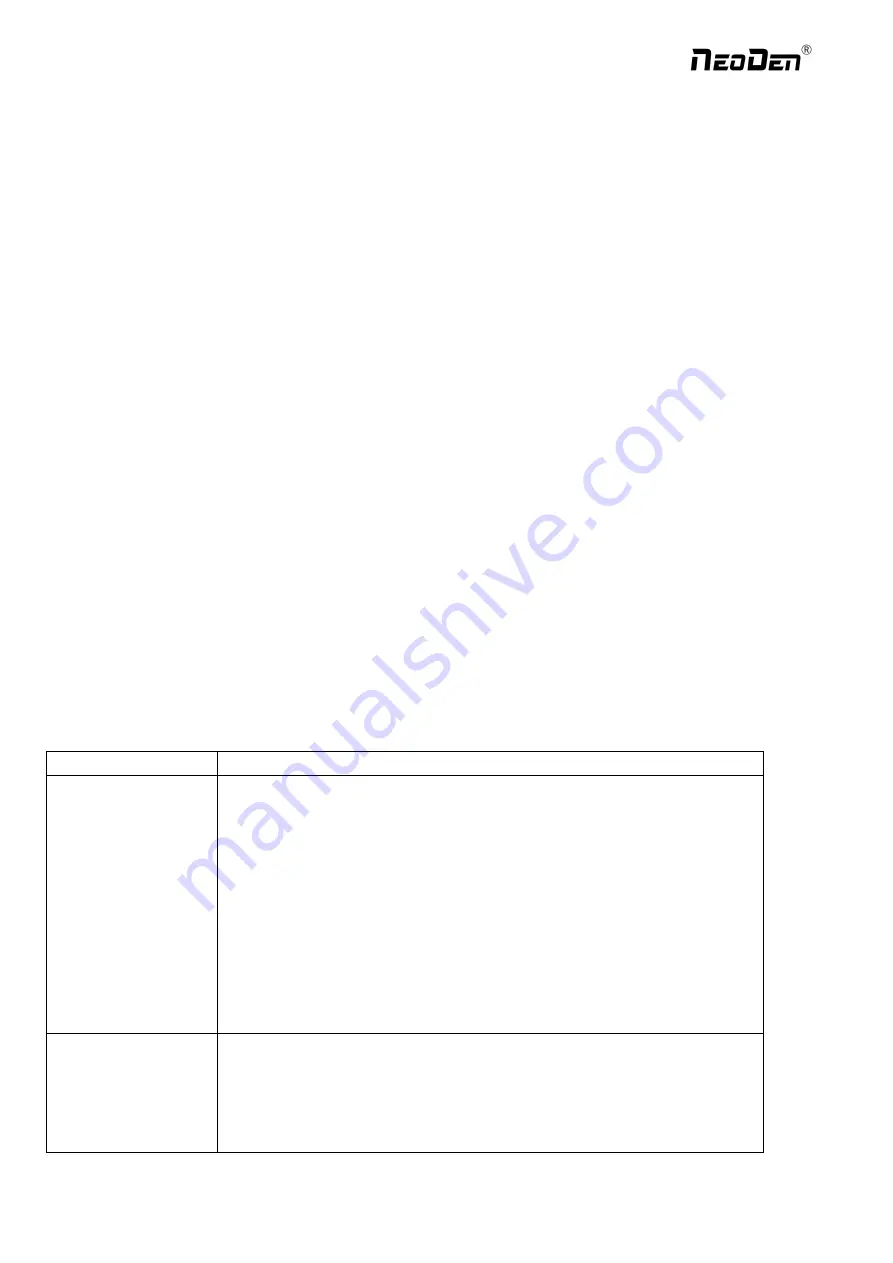
●Operating strictly against equipment's instruction. Don’t use machine with problems. Stop the machine once malfunction
appears and contact with the after-sales service staff, restart to work after problem solved.
●Operator should be concentrated
,
Observation-- to see whether there is abnormal situation, such as peel-box doesn’t work, plastic tape is broken etc.
Listening-- whether have strange sound, such as noise from placement head, sound of loss component, strange noise of
conveyor etc.
Handwork-- solve some small problems in time, such as install feeder, correction placement position etc. If the main
machine body or circuit problem, please consult after-sales staff. Formulate measures to reduce/ avoid big problem.
12.1.3 Formulate the measures to reduce/avoid big problem
The most easily appeared problem during work are placement wrong components and placement misaligned. Supply below
measures for ref.
①
It needs to check whether the components package is matched with related feeder. If not, please correct them.
②
As to tape reel feeder, when ran out of one reel, operator must check whether newly changed tape reel is correct or not.
③
After import the SMD file or edit chip list manually, please recheck each components No., nozzle rotation angle and
placement position to make sure correct.
④
Operator must check the first finished PCB of each file. If any problem, please find solutions such as revise program to
solve it.
⑤
To check the placement position misaligned or not, component loss problem in regular work. Find reason in time and
solve it.
⑥
Set pre-welding detection station (manual or AOI)
In sum, P&P machine's running speed and placement accuracy still has limit. Peoples work is important to run machine on
its proper role. So, it’s necessary to comply with effective measures to keep machine normal work, its placement quality and
efficiency.
12.2 Maintenance
Arrange regular inspection and maintenance system.
12.2.1 Daily Inspection
Items
Items check before
power on
①
Temperature& Moisture: Temperature 20
℃~
26
℃
, humidity 45~70%
②
Indoor environment: Air clean without aggregate air.
③
No clutters within the placement area and keep rails clean.
④
No spots on cameras and keep lens clean.
⑤
No obstacles around the head nozzles
⑥
Checking if nozzles are dirty, distorted; If so, please clean or change the
nozzle.
⑦
Checking if feeders are correctly installed in stacks and confirm no clutters
on stack.
⑧
Checking the connection of air connector and air hose
⑨
Checking air pressure.
Items
check
after
power on
①
Checking if the monitor display normally after system start up.
②
Checking if emergency button can work normally or not.
③
Checking if placement head can move back to the origin.
④
Checking if there’s abnormal noise while placement head move.
⑤
Checking all nozzles vacuum pressure.
50
Zhejiang
NeoDen Technology Co.,Ltd.
Содержание K1830
Страница 6: ...1 3Working Area Structure Figure 3 Top view of main mounting area 6 Zhejiang NeoDen Technology Co Ltd ...
Страница 7: ...Figure 4 X axis Beam Figure 5 Main Placement Head Camera 7 Zhejiang NeoDen Technology Co Ltd ...
Страница 35: ...8 2 Component Positions Setup 35 Zhejiang NeoDen Technology Co Ltd ...
Страница 44: ...11 Structure and maintenance instruction 11 1 Feeder Brief Introduction 44 Zhejiang NeoDen Technology Co Ltd ...