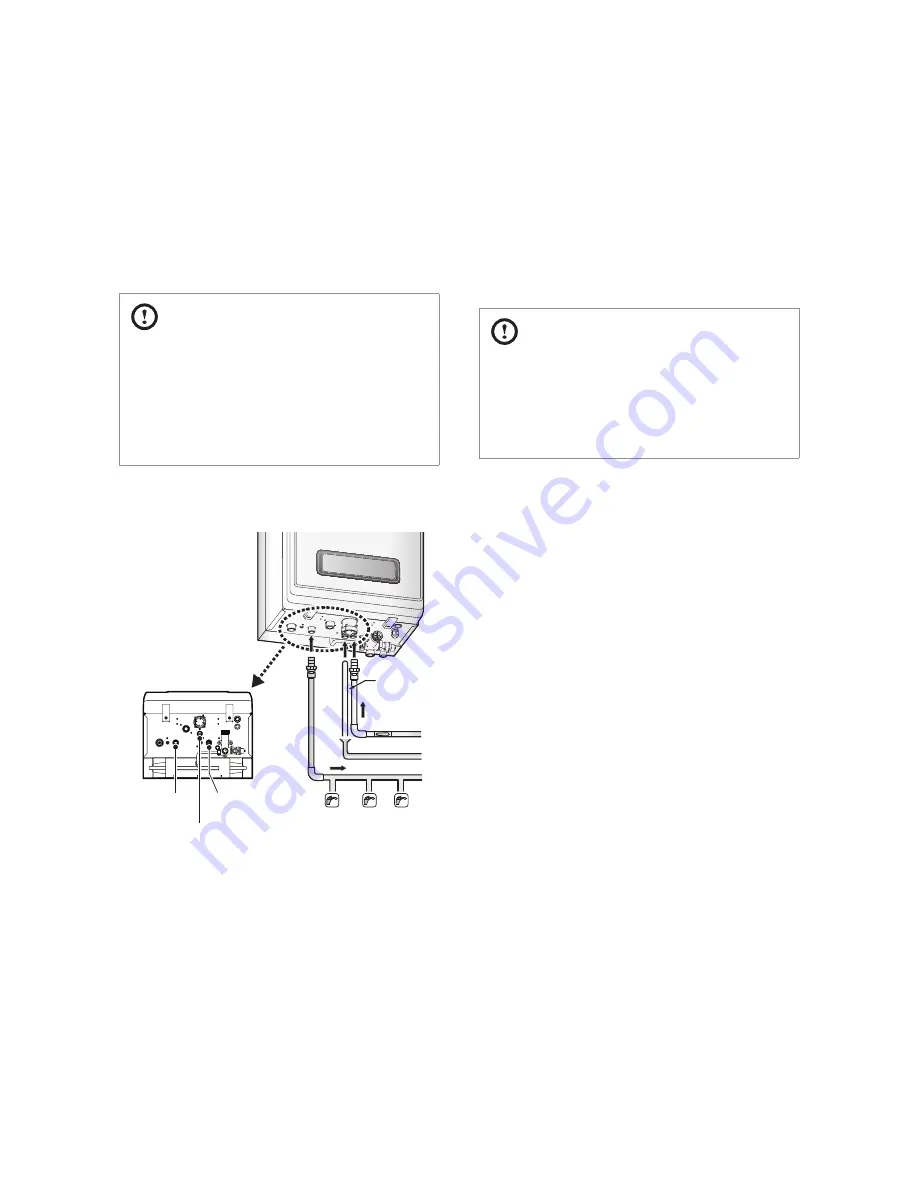
24 Installing the System Piping
3.2 Installing a Domestic Hot Water
(DHW) System
The Navien NCB LSWE boiler provides domestic hot water
continuously when flow is sensed by the flow sensor. This
method is the most efficient means of heating water by allowing
the boiler to operate at a lower return water temperature
by minimizing standby losses, thus increasing combustion
efficiency.
CAUTION
●
The installation must be made by sufficiently qualified
staff, authorised to do so.
●
For correct installation, all the requirements and
recommendations described in the Regulation for Heating
Installations in Buildings (RITE) must be complied with,
together with all other national and/or local regulations
applicable at the time of installation.
Refer to the following illustration for a typical DHW piping
example for the boiler.
Condensate
Drain Hose
Cold Water
Supply
Condensate Pipe
Hot Water Supply
Bottom View
DHW Outlet
Adaptor
Condensate
Outlet
Water Inlet
Adaptor
When installing the DHW system, follow these guidelines:
●
Use only pipes, fittings, valves, and other components (such
as solder), that are approved for use in potable water systems.
●
Tighten the connection valves with care to avoid damage.
●
Keep the hot water piping system as short as possible, to
deliver hot water to the fixtures more quickly.
●
After installing the boiler, clean the cold water inlet filter.
Then, test the boiler for proper DHW supply and inspect for
leaks.
3.3 Connecting the Condensate Drain
Line
The Navien NCB LSWE boiler creates condensation when it
operates. This condensation has an acidic pH of 3-5. Follow
all local codes and regulations when disposing of condensate
from the boiler. We recommend draining the condensate into
a laundry tub, as the alkali in laundry detergent will neutralize
the acid in the condensate. However, other suitable waste drain
locations may be used according to the local legislation.
CAUTION
●
Do not cap or plug the integrated condensate line. If
prevented from draining, condensate can damage the
boiler.
●
The condensate line must have a negative slope to drain
properly.
The requirements recommended for the condensate drain line
installation are as follows:
●
For correct condensate drain line installation, the tube must
have a minimum diameter of Ø22 mm.
●
The tube must be made of a material that can withstand
corrosion, e.g. PVC, PCV-U, ABS, PVC-C or PP. It must not be
made of metal.
●
For safety reasons, the end of the tube must be as close as
possible to the draining point.
●
When the condensate drainage is connected to a general
drain network inside the building, the effects of overpressure
that could occur inside it must be taken into account,
installing suitable pressure release and ventilation elements.
●
The length of the tubes outside the building must be as short
as possible. They must also be installed with as much tilt as
possible. The tubes must be insulated if they are exposed
to extremly cold weather or blizzards. If the tubes are not
insulated, they must have a diameter of at least Ø32 mm.
●
The drain tube must have a minimum tilt of 2.5° downstream
of the boiler.
●
For tubes with Ø22 mm, the maximum permitted length is 3
metres.
●
If the appliance is installed in a non-heated premises, the tube
system must be treated as if it was an outdoor installation.
●
To prevent the risk of tripping, the outdoor tubes must be
fixed to the walls.
Before connecting the condensate drain, choose one of the
following disposal options:
Содержание NCB-24LSWE
Страница 59: ...60 Appendixes 10 3 Wiring Diagram 0 9...
Страница 60: ...Appendixes 61 10 4 Ladder Diagram...