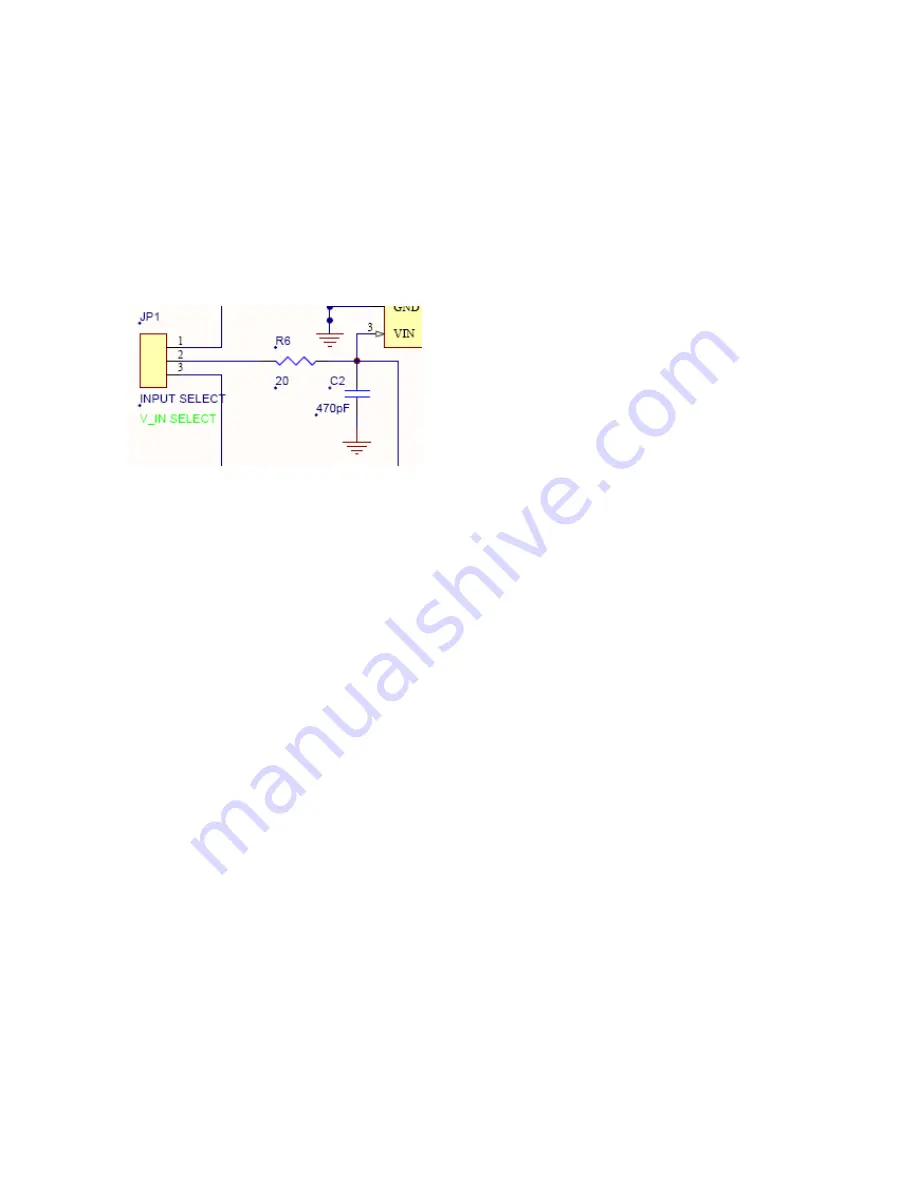
http://www.national.com
7
4.2 Analog Input Signal
There are three basic options for connecting an
input signal to the ADC. The three options
facilitate AC-coupled and DC-coupled input
signals.
The first way to apply an input signal to the ADC
is to connect it to pin 2 of JP1. The signal’s return
(GND) should be connected to TP5. This
configuration provides the input circuit seen in
Figure 8.
Figure 8: Unbiased input circuit.
The second way is to configure the board for an
AC coupled input. DC biasing is available for
inputs applied to J2 but is currently not populated
on the board. By adding DC bias resistors R1 and
R4 (value 4.99k
Ω
), and changing C1 to a 1.0uF
capacitor, the board can be used with an AC
coupled input signal (
Figure 3
). To improve the
signal integrity of the connection to the board, an
SMA connector should be stuffed at J2 (V_IN). If
the input source has a 50
Ω
output impedance, a
51
Ω
resistor can be installed at R3.
The third way to configure the input is by
incorporating the Amplifier into the signal path.
The LMP7731 Low-noise, Precision Operational
Amplifier is included on the board for convenient
buffering of the analog input. By default, it is
configured as a simple voltage follower (
Figure 4
).
Resistors R10 and R11 can be modified to add
non-inverting gain to the circuit. Adding
capacitance at C6 configures the amplifier as a
low-pass filter. To use the input buffer, simply
move the JP1 jumper to pins 2 & 3.
In any case, it is important that the signal stays
within the allowable input range of the ADC (0V to
V
A
). Dynamic input signals should be applied
through a bandpass filter to eliminate the noise
and harmonics commonly associated with signal
sources. To accurately evaluate the performance
of the ADC121C021, the source must be better
than -90dBc THD.
4.3 ADC Reference Circuitry
The ADC121C021 family is internally referenced.
Therefore, the Analog-to-Digital converter gets its
reference from the analog supply (V
A
). Hence, a
clean analog supply must be used to guarantee
the performance of the ADC.
4.4 I
2
C Interface
Please refer to section 1.7 of the ADC121C021
datasheet for a detailed description of the I
2
C
interface.
The board is designed with I
2
C pull-up resistors on
both the SDA and SCL lines (R8 & R9). These
resistors are enabled by a single jumper (JP2)
and can easily be added or removed from the I
2
C
bus. Also, footprints for series resistors are
designed into the board (R2 & R5). The board is
shipped with 0
Ω
resistors which can be modified
to provide series resistance if interfacing to a
noisy I
2
C bus.
The SDA signal is accessible by soldering to VIA1
or connecting to pin 1 of the WV4S connector
(J1). The SCL signal is accessible by soldering to
VIA2 or connecting to pin 5 of J1.
The on-board pull-up resistors can be powered
with an external supply by removing the jumper at
JP2 and connecting the supply to pin 2 of JP2 or
VIA6.
4.5 Alert Function
The ADC121C021 provides a programmable “out-
of-range” Alert function. At the end of every
conversion, the measured voltage is compared to
the values in the V
HIGH
and V
LOW
registers. If the
measured voltage violates either of these values,
an alert condition occurs. The Over Range Alert
flag in the Alert Status Register indicates the V
HIGH
limit has been violated. The Under Range Alert
flag indicated the V
LOW
limit has been violated. If
enabled, the alert condition is also propagated to
bit15 of the Conversion Result Register and the
ALERT output pin.
The Alert function is configured by writing to the
ADC’s internal registers. Refer to Section 1.6 of
the Datasheet for a detailed description of the
ADC’s internal Registers.
Refer to
Section 1.8
of the Datasheet for a
detailed description of the Alert function.