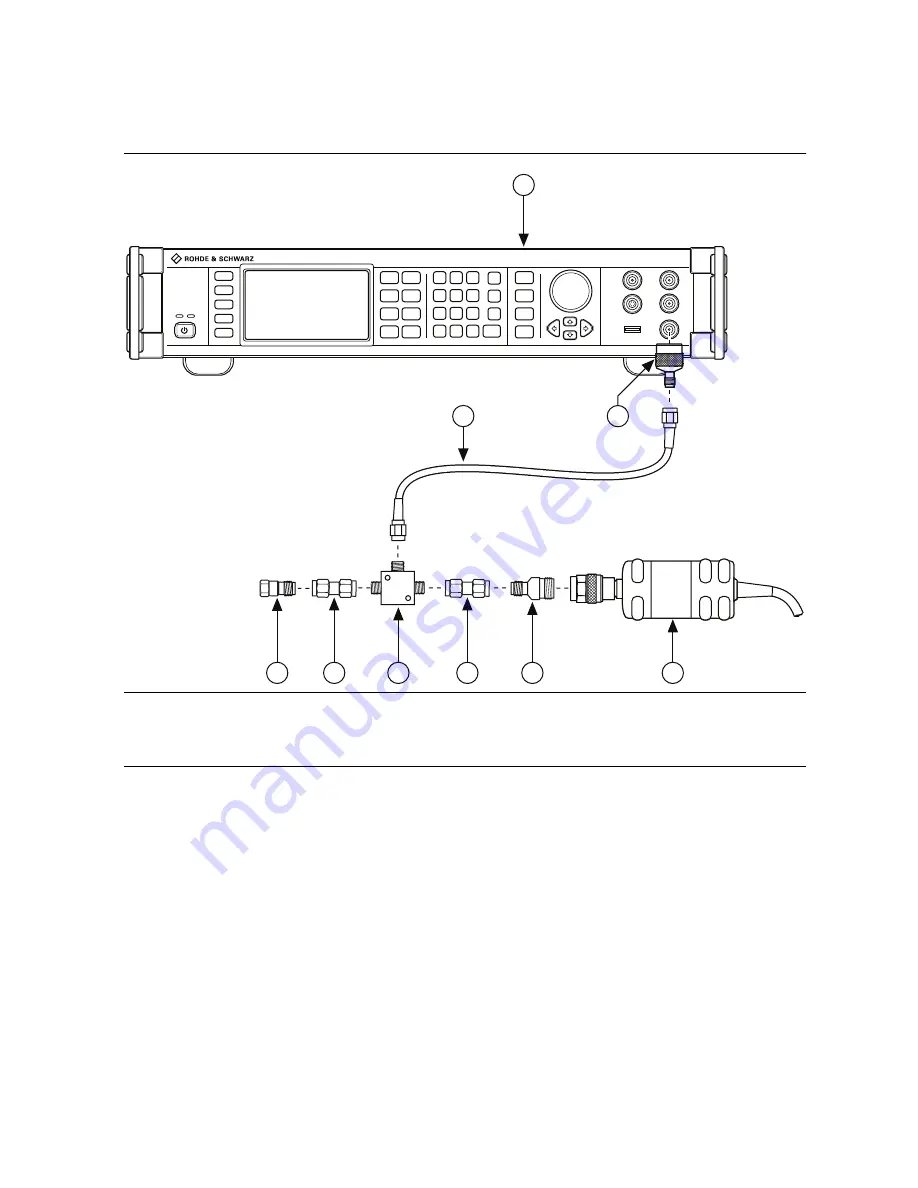
PXIe-5185/5186 Calibration Procedure
|
© National Instruments
|
9
7.
Connect the power sensor to splitter output 2.
The following figure illustrates the hardware setup.
Figure 1.
Connection Diagram for Measuring at Splitter Output 2 (SMA)
8.
Configure the signal generator to generate a sine waveform with the following
characteristics:
•
Frequency: the Test Point Frequency value from Table 2
•
Amplitude level: the Test Point Amplitude value from Table 2
9.
Configure the power sensor to correct for the Test Point Frequency value using the power
sensor frequency correction function.
10. Use the power sensor to measure the power in dBm.
11. Repeat steps 8 through 10 for each configuration in Table 2, recording each result as
splitter output 2 power
, where each configuration has a corresponding value.
12. Disconnect the power sensor and 50
Ω
SMA terminator (f) from splitter output 2 and
splitter output 1.
1
Signal Generator
2
SMA (f)-to-N (m) Adapter
3
SMA (m)-to-SMA (m) Cable
4
50
Ω
SMA Terminator (f)
5
SMA (m)-to-SMA (m) Adapter
6
Power Splitter
7
SMA (f)-to-N (f) Adapter
8
Power Sensor
1
6
4
5
3
7
8
2
5