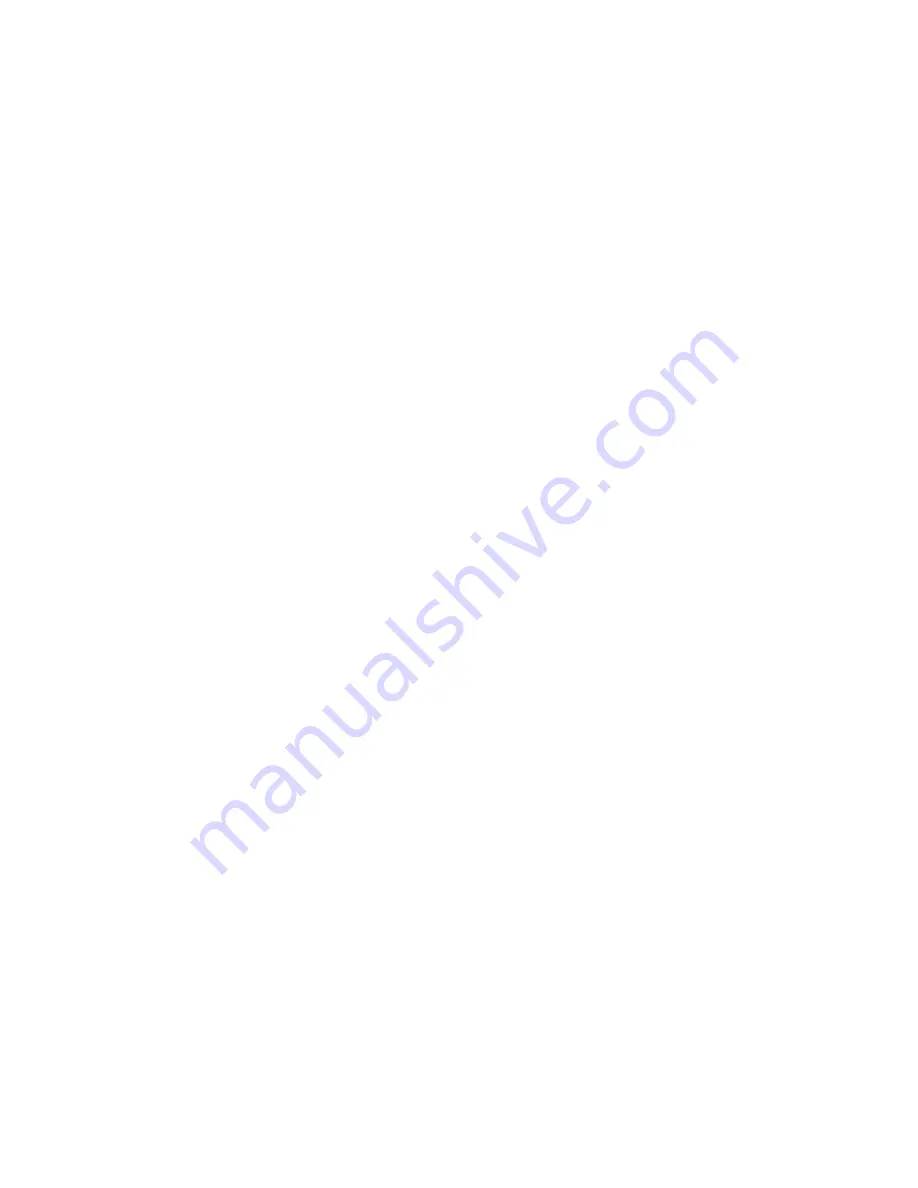
8
|
ni.com
|
NI 9751 User Manual
Working Voltage Requirement
The internal boost power supply can maintain a higher working voltage to drive the peak current
level in a shorter amount of time and provide quicker valve opening times and more predictable
fuel injection quantities over a given injection duration. The boost power supplies operate less
efficiently at higher voltages. The power supply must work harder to maintain a higher working
voltage. Typical times to reach 20 A in common-rail diesel injectors are on the order of 30 to
100
μ
s, with a working voltage of 100 V.
Frequency of Injection Events
The frequency of injection events is directly proportional to the work the power supply requires
to maintain the working voltage.
Injector Back-Boost
You can obtain a significant and useful back-boost charge from the injector solenoid at the end
of each injection event. This back-boost from the solenoid depends on the hold-current level
during the injection event and the working voltage of the boost power supply. If you correctly
configure the current profile, a small back-boost on the order of 5 V occurs to the power supply,
which reduces the work required to maintain the working voltage.
You might incorrectly configure the module to use very little of the high voltage supply for
driving the peak current while also setting a high hold-current level. This configuration can lead
to back-boosting the power supply over the required working voltage. Use the internal high
voltage supply to prevent this from happening. If the working voltage exceeds 190 V, a fault
occurs and shut down proceeds automatically.
Power Supply Faults and Protections
The following critical faults related to the operation of the internal power supply might cause all
operations of the module to shut down automatically. Two or more of these faults might occur
under certain conditions. For example, the power supply might be loaded such that the board
temperature reaches its limit before the overload integrator limit is reached. You can re-enable
the internal boost power supply and injection control by manually clearing the faults with
software.
Power Supply Charge Fault (PSCharge)
If the power supply is actively attempting to recharge and detects that the voltage is not rising,
the charge fault is set. This fault most likely occurs when an internal problem, such as a capacitor
failure, exists with the module.
Power Supply Overload Fault (PSOverLoad)
The NI 9751 maintains an integrator of power supply usage. An internal counter increments with
each power supply voltage boost and decrements according to a fixed time interval. If the
integrator winds up to 148,480 counts, an overload fault is set. This fault indicates that the
module temperature will soon rise beyond the maximum operating temperature unless stopped.
The module temperature fault might trip before the overload fault, depending on the actual
conditions.
Содержание NI 9751
Страница 1: ...SHC68 68 RDIO...