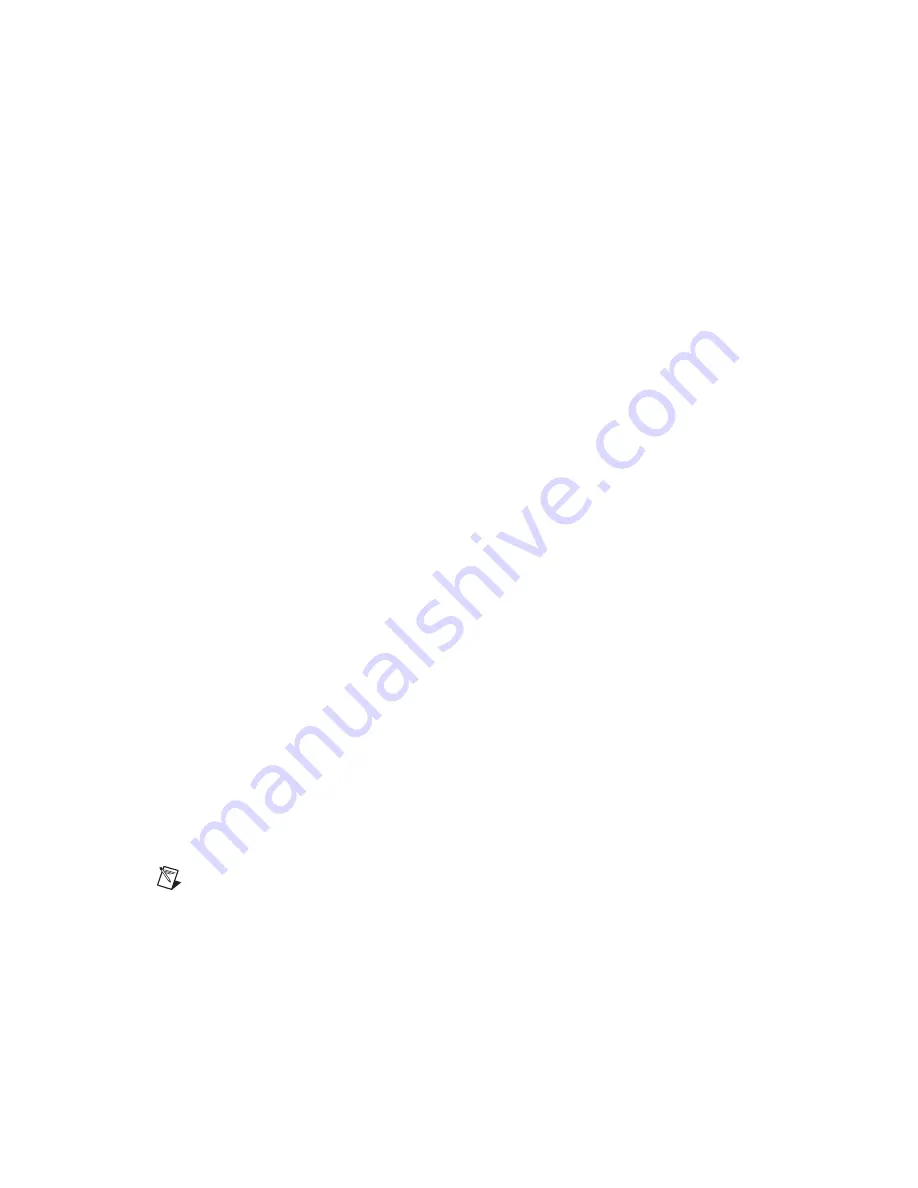
Chapter 4
Connecting Signals
4-20
ni.com
Programmable Function Input Connections
You can externally control 13 internal timing signals from the PFI pins.
The source for each of these signals is software selectable from any PFI
when you want external control. This flexible routing scheme reduces the
need to change the physical wiring to the device I/O connector for different
applications requiring alternative wiring.
You can individually enable each of the PFI pins to output a specific
internal timing signal. For example, if you need the STARTSCAN signal as
an output on the I/O connector, software can turn on the output driver for
the PFI7/STARTSCAN pin. Be careful not to drive a PFI signal externally
when it is configured as an output.
As an input, each PFI can be individually configured for edge or level
detection and for polarity selection, as well. You can use the polarity
selection for any of the timing signals, but the edge or level detection
depends upon the particular timing signal being controlled. The detection
requirements for each timing signal are listed within the section that
discusses that individual signal.
In edge-detection mode, the minimum pulse width required is 10 ns.
This setting applies for both rising-edge and falling-edge polarity settings.
Edge-detect mode does not have a maximum pulse-width requirement.
In level-detection mode, the PFIs themselves do not impose a minimum or
maximum pulse-width requirement, but the particular timing signal being
controlled can impose limits. These requirements are listed later in this
chapter.
DAQ Timing Connections
The DAQ timing signals are TRIG1, TRIG2, STARTSCAN, CONVERT*,
AIGATE, SISOURCE, SCANCLK, and EXTSTROBE*.
Posttriggered data acquisition allows you to view only data that is acquired
after a trigger event is received. A typical posttriggered DAQ sequence is
shown in Figure 4-12.
Note
On the NI 6115/6120, each STARTSCAN pulse initiates one CONVERT* pulse,
which simultaneously samples all channels.