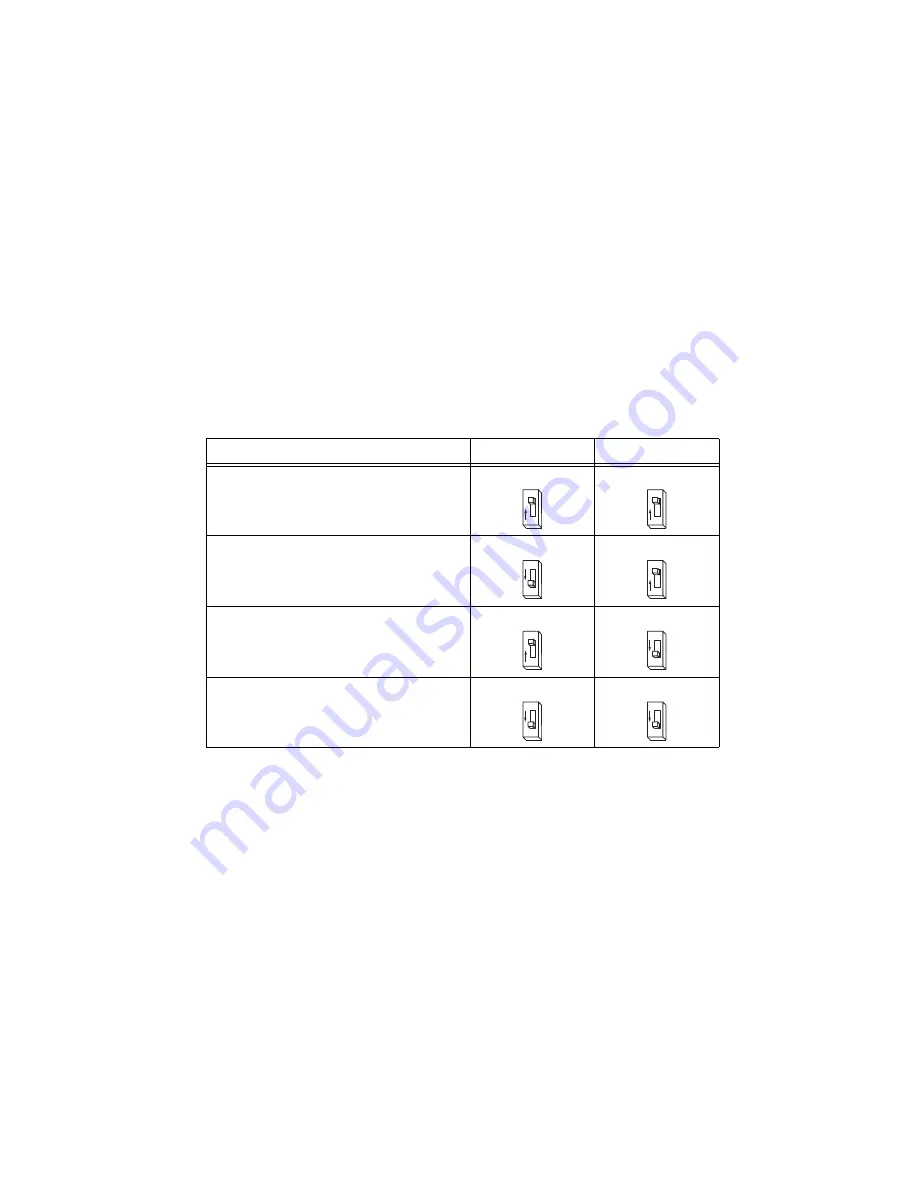
Getting Started with NI 9512 and P7000 Drives
|
© National Instruments
|
15
Dynamic Smoothing
Dynamic smoothing is a temporal filter (second-order, low-pass) applied to the command
sequence to reduce jerk. It helps reduce overshoot and lessens the excitation of mechanical
resonance in the system. It filters from slightly below the resonant frequency up to well above
resonance to remove spectral content that would be misrepresented in the motor output and may
also excite other parts of the machine.
Dynamic smoothing is a very powerful feature for achieving maximum torque from the motor.
However, it is difficult to optimize and is not necessary for the vast majority of applications.
Therefore, National Instruments recommends setting both DIP switches to OFF for minimal
smoothing.
Table 8 lists the dynamic smoothing switch settings.
Table 8.
Dynamic Smoothing DIP Switch Settings
Dynamic Smoothing
S2–8
S2–9
Minimal
OFF
OFF
Moderate
ON
OFF
Heavy
OFF
ON
Aggressive
ON
ON
8
O
F
F
9
O
F
F
8
O
N
9
O
F
F
8
O
F
F
9
O
N
8
O
N
9
O
N