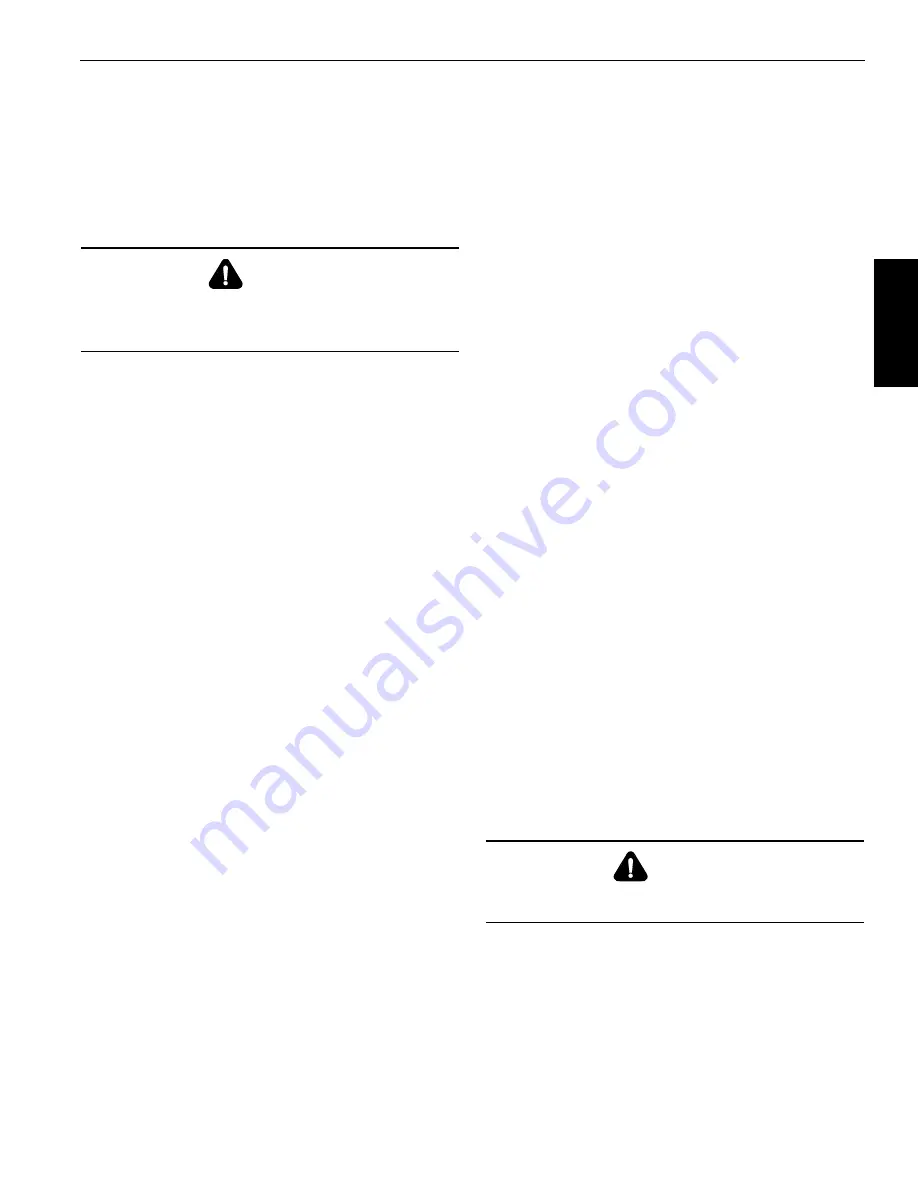
10
3
NATIONAL CRANE
08-19-2022 Control # 092-13
3-9
600H ELECTRIC
SYSTEM
Never allow any operation until the operator has read all
instructions and has become completely familiar with the
total system. Should
anything
happen unexplained,
unpredicted, or incorrect operation, immediately shut down
the complete system and investigate! This includes shutting
down all electronics, hydraulics, power take-offs, and
engines.
Never
resume operation until the problem has been
corrected!
Before attempting to start truck with remote control make
sure the drive train is in neutral.
When not using the remote control, disconnect power to the
remote control system with the selector switch installed in the
truck cab. This will prevent inadvertent operation of the crane
if the hand control is operated. Protect and monitor the hand
control unit to prevent damage and unplanned operation.
Always turn the truck ignition off and start the unit using the
remote hand control. This will allow the truck engine to be
turned off with the remote hand control. If the truck ignition is
on, the stop and emergency stop functions will not function.
Operation
General
The system consists of a Modulator/Transmitter) unit and a
receiver/decoder (Receiver) unit.’The system operates on
the 5 RF channels in accordance with FCC Subpart D -
Lower Power Communications Devices, Part 15.117. Use of
this device is subject to the provisions of FCC Part 15.103. A
license is NOT required to operate this system.
Transmitter
The transmitter generates an RF signal which is FM
modulated. The Modulation is a 120 bit data stream with start
and stop bits, information concerning the selected switch
being activated, and a specialized algorithm developed to
ensure the validity of the transmission. Also transmitted are
address information to enable it to “talk” to its associated
receiver. This address information is set at the factory so no
two devices will be the same. There may be over 20000 units
in the same vicinity without any cross activation.
Receiver
The receiver receives the signal transmitted by the
transmitter, decodes the data stream and checks for validity
of the address and the start and stop bits of the received
data. If this is correct, a proprietary software algorithm is
performed to accept or reject the information to be passed on
to the outputs. If for any reason this test fails, no output will
be allowed to function. Once this test has passed, the
appropriate output will be activated.
Single Proportional Control
The radio system is designed with its own amplifier circuit
th at s up plie s a puls e widt h mod ulat io n o ut pu t. (An
i n d e p e n d e n t a m p l i f i e r c a r d i s n o t r e q u i r e d f o r t h e
proportional valve.)
Input Voltage ............................. 10-30 VDC
Output Voltage .......................... Same as input voltage
Output Current .......................... 5 amps maximum
Proportional Setting .................. Independent low end /
high end settings
The independent proportional low and high end settings
match the potentiometer travel with the proportional valve’s
working voltage and range.
The proportional valve is remote mounted between the
hydraulic reservoir and the existing valve bank. A trigger
controlled potentiometer is mounted in the grip of the hand
held control that is spring loaded. This creates a single
control, “metering” fluid to all the valves mounted on a
manifold.
Electrical Circuit Description
Receiver Electrical Supply
1.
Positive 12 VDC power is supplied from the battery to a
15 amp thermal circuit breaker then to plug letter “A” in
the receptacle.
2.
When the receiver cord is plugged in, +12 VDC power
becomes available to the receiver.
Hand Control Circuitry
1.
The hand control (transmitter) is activated by turning the
power switch to the ON position. The radio transmits ten
seconds to “initialize” the receiver.
This switch should
be placed in the OFF position when not using the
remote controls.
Failure to do so will greatly reduce the
life of the 9 volt battery in the hand control (transmitter).
2.
OFF-START switch in “CENTERED” position.
a.
Ignition circuit not energized until truck is started.
3.
OFF-START switch in “START” position (Momentary).
a.
“L” (Ignition) circuit energized and stays energized
when switch returns to central position.
DANGER
Starting truck engine with drive train engaged will cause
death or serious injury.
Do not start truck engine unless drive train is in neutral.
DANGER
Failure to do so could cause inadvertent operation of the
crane.
REFERENCE ONLY
Содержание 600H
Страница 1: ...Service Manual National Crane 600H R E F E R E N C E O N L Y...
Страница 6: ...THIS PAGE BLANK R E F E R E N C E O N L Y...
Страница 38: ...INTRODUCTION 600H SERVICE MANUAL 1 26 08 19 2022 Control 092 13 THIS PAGE BLANK R E F E R E N C E O N L Y...
Страница 54: ...HYDRAULIC SYSTEM SERVICE MANUAL 600H 2 16 08 19 2022 Control 092 13 THIS PAGE BLANK R E F E R E N C E O N L Y...
Страница 136: ...BOOM 600H SERVICE MANUAL 4 62 08 19 2022 Control 092 13 R E F E R E N C E O N L Y...
Страница 138: ...HOIST 600H SERVICE MANUAL 5 2 08 19 2022 Control 092 13 THIS PAGE BLANK R E F E R E N C E O N L Y...
Страница 168: ...OUTRIGGERS 600H SERVICE MANUAL 7 18 08 19 2022 Control 092 13 THIS PAGE BLANK R E F E R E N C E O N L Y...
Страница 182: ...LUBRICATION 600H SERVICE MANUAL 8 14 08 19 2022 Control 092 13 THIS PAGE BLANK R E F E R E N C E O N L Y...
Страница 226: ...CRANE INSTALLATION 600H SERVICE 9 44 08 19 2022 Control 092 13 THIS PAGE BLANK R E F E R E N C E O N L Y...
Страница 228: ...SCHEMATICS 600H SERVICE MANUAL 10 2 08 19 2022 Control 092 13 THIS PAGE BLANK R E F E R E N C E O N L Y...
Страница 231: ...R E F E R E N C E O N L Y...
Страница 232: ...R E F E R E N C E O N L Y...