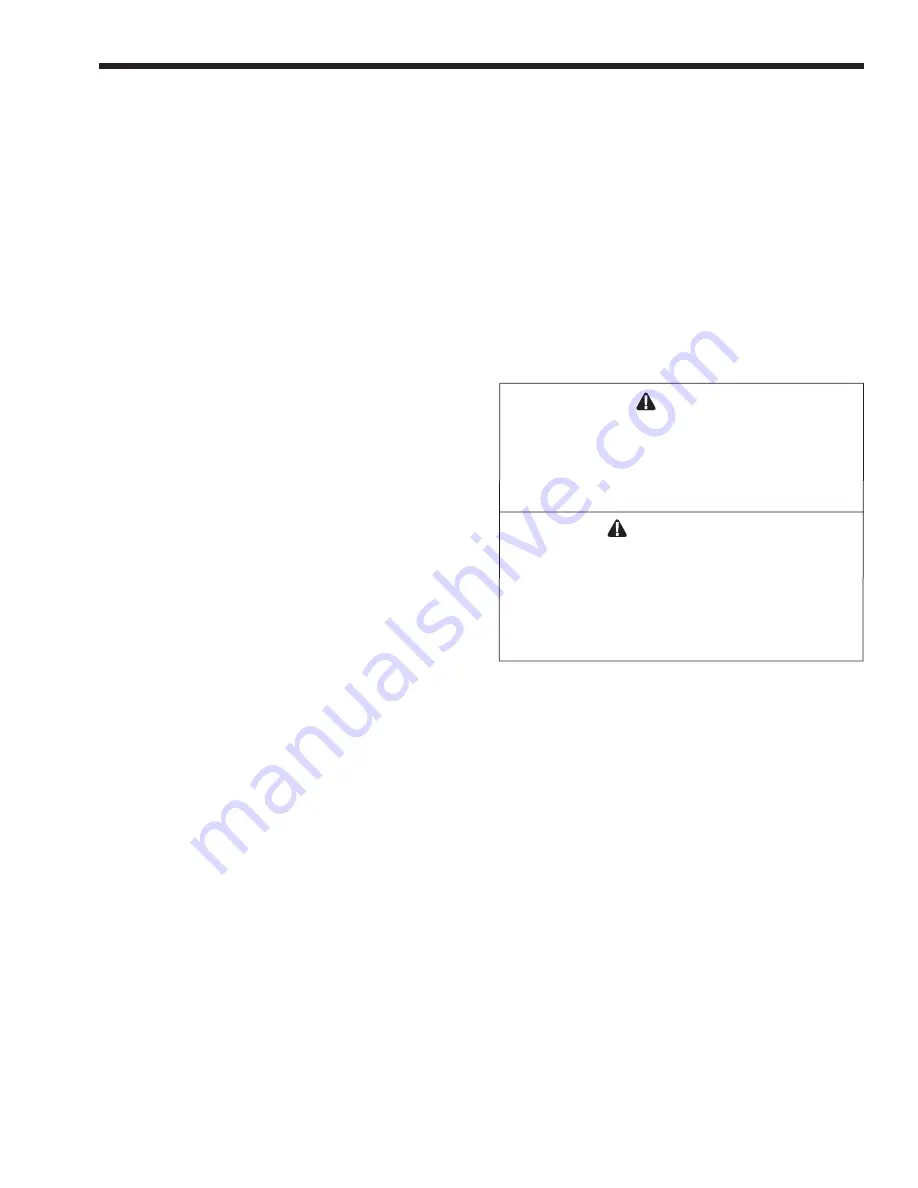
Fire Coil 85
(200, 300, 400)
Page 29
SECTION 6.
Operating Instructions
6.1 Filling the Boiler System
1.
Ensure the system is fully connected. Close all
bleeding devices and open make-up water valve.
Allow system to fi ll slowly.
2.
If make-up water pump is employed, adjust
pressure switch on pumping system to provide
a minimum of 12 psi (81.8 kPa) at the highest
point in the heating loop.
3.
If a water pressure regulator is provided on the
make-up water line, adjust the pressure regulator
to provide at least 12 psi (81.8 kPa) at the highest
point in the heating loop.
4.
Open bleeding devices on all radiation units
at the high points in the piping throughout
the system, unless automatic air bleeders are
provided at such points.
5.
Run system circulating pump for a minimum of
30 minutes with the boiler shut off.
6.
Open all strainers in the circulating system,
check fl ow switch operation, and check for
debris. If debris is present, clean out to ensure
proper circulation.
7.
Recheck all air bleeders as described in Step 4.
8.
Check liquid level in expansion tank. With the
system full of water and under normal operating
pressure, the level of water in the expansion tank
should not exceed ¼ of the total, with the balance
fi lled with air.
9.
Start up boiler according to the procedure in this
manual. Operate the entire system, including the
pump, boiler, and radiation units for one (1) hour.
10. Recheck the water level in the expansion tank. If
the water level exceeds ¼ of the volume of the
expansion tank, open the tank drain, and drain to
that level.
11. Shut down the entire system and vent all
radiation units and high points in the system
piping, as described in Step 4.
12. Close make-up water valve and check strainer in
pressure reducing valve for sediment or debris
from the make-up water line. Reopen make-up
water valve.
13. Check gauge for correct water pressure and also
check water level in the system. If the height
indicated above the boiler insures that water is at
the highest point in the circulating loop, then the
system is ready for operation.
14. Refer to local codes and the make-up water
valve manufacturer’s instructions as to whether
the make-up water valve should be left open or
closed.
15. After placing the unit in operation, the ignition
system safety shutoff device must be tested.
First, shut off the manual gas valve, and call
the unit for heat. After the pre-purge and ignitor
heat-up time, the main gas terminals will be
energized, attempting to light, for seven (7)
seconds, and then will de-energize. The unit will
attempt to light two more times, and then will go
into lockout mode. Second, turn the power off
and then on again, open the manual gas valve
and allow the unit to light. While the unit is
operating, close the manual gas valve and ensure
that power to the main gas valve has been cut.
16. Within three (3) days of start-up, recheck all air
bleeders and the expansion tank as described in
Steps 4 and 8 above.
Important: The installer is responsible for identifying
to the owner/operator the location of all emergency
shutoff devices.
WARNING
Do not use this appliance if any part has been
under water. Immediately call a qualified service
technician to inspect the appliance and to replace
any part of the control system and any gas control
that may have been under water.
AVERTISSEMENT
N’utilisez pas cet appareil si l’une de ses pièces est
passée sous l’eau. Appelez tout de suite un technicien
en entretien et en réparation pour inspection de
l’appareil et remplacement des pièces du système de
commande, et des pièces de commande du circuit
gaz, qui sont passées sous l’eau.
6.2 Operating Temperature Control
(Note: F85 may be ordered with either an on/off
or 2-stage aquastat.)
To utilize the boiler's on-board controller, be sure
to have the “Local/Remote” selector switch to “Local”.
Set the controller to the desired operating set point.
The controller has an interstage differential that can be
adjusted from 3°F to 10°F. This allows the user to have
some control over how stage 2 and stage 1 call for heat
(see Figure 19).
Because the Fire Coil 85 controller senses inlet
water and the manual reset high limit senses outlet
water, the high limit should be set 40-50°F higher than
the controller, to avoid nuisance lockout of the manual
reset high limit.
6.3 External Boiler Operations
If controlling the stages of the F85 from an
external source (multiple boiler control, BAS, etc) the
“Local/Remote” selector switch above the terminal
strip must be placed in the “Remote” position. In this
mode, the controller that is mounted on the F85 will no
longer have control of the unit. The 24V from the unit
waits at the input terminal, and the external control
switches this 24V from the input terminal to the stage
terminal. The input for stage 1 is initiated by closing
the circuit between the 2 terminals on the terminal
Содержание F85H Fire Coil 85 200
Страница 26: ...National Combustion Co Inc Page 26 Figure 15 Wiring Diagram ON OFF Boiler or Water Heater ...
Страница 27: ...Fire Coil 85 200 300 400 Page 27 Figure 16 Wiring Diagram 2 STAGE Boiler or Water Heater ...
Страница 43: ...Fire Coil 85 200 300 400 Page 43 Figure 24 Control Panel Components ...