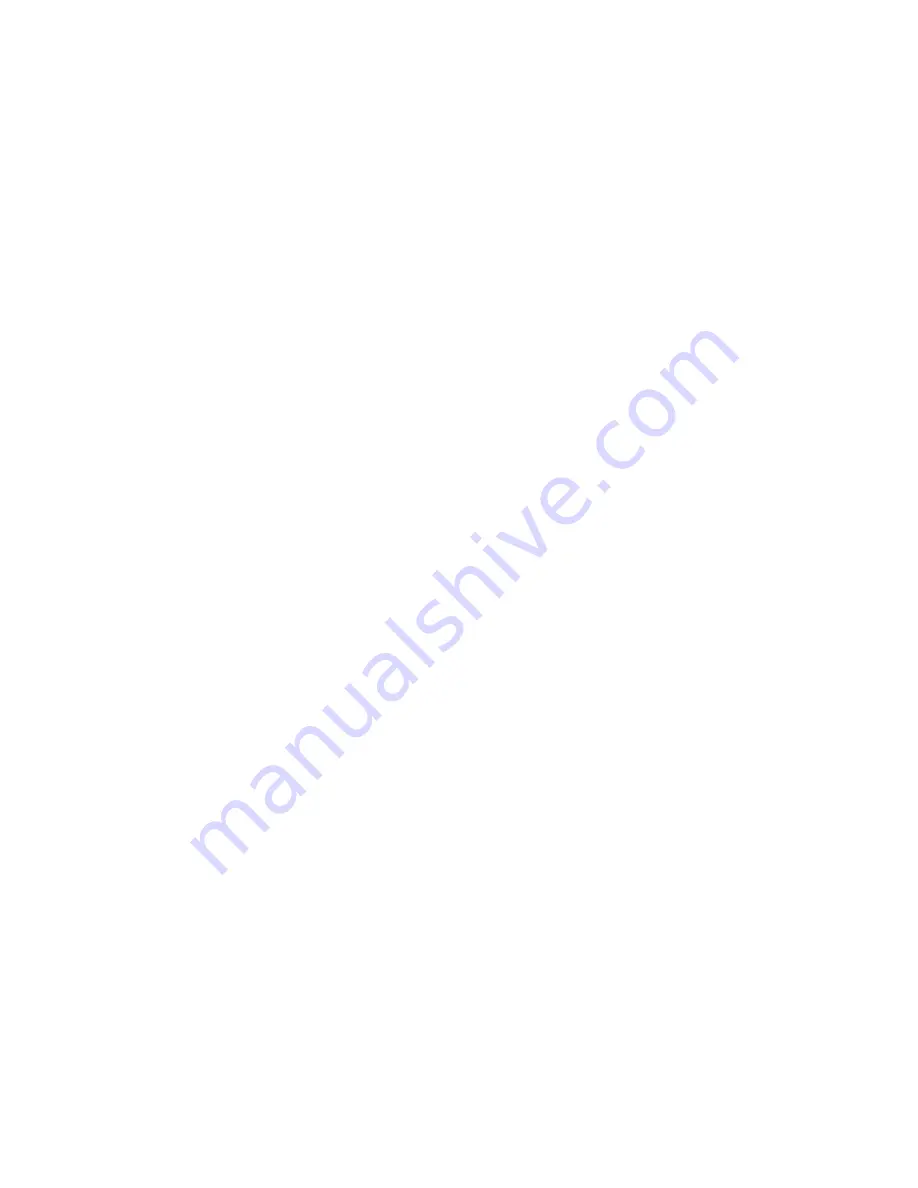
9
CAUTION: FOR ANY WORK ON PUMP OR
SWITCH, ALWAYS UNPLUG POWER
CORD. DO NOT JUST TURN OFF CIRCUIT
BREAKER OR UNSCREW FUSE.
TO REPLACE AUTOMATIC FLOAT
(1) Unplug the pump power cord from the back of the
piggyback float plug.
(2) Unplug the piggy-back float plug from the power
receptacle.
(3) Remove the pump from the sump if access to the tether
point is inaccessible.
(4) Disconnect the switch from its tether point and remove
from the discharge piping.
(5) Re-tether the new cord to the pump or discharge piping.
(6) Cable tie or tape the power and switch cords to the
discharge piping.
(7) Plug the switch into the power receptacle.
(8) Plug the power cord into the switch plug.
(9) Fill basin and test switch operation.
ALL PUMP REPAIRS SHOULD BE DONE AT AN AUTHO-
RIZED MYERS SERVICE CENTER.
TO REPLACE THE AUTOMATIC
VERTICAL FLOAT SWITCH
(1) Unplug the pump power cord from the back of the
piggy-back plug.
(2) Unplug the piggy-back plug from the power receptacle.
(3) Remove the two mounting screws in the switch bracket
that attached the switch assembly to the pump and
remove from the discharge piping.
(4) Mount new switch assembly to pump. Be sure to install
plastic tie provided and re-tether to mounting screw.
(5) Cable tie or tape the power and switch cords to the
discharge piping.
(6) Plug the piggy-back switch in the power receptacle.
(7) Plug power cord into the piggy-back switch plug.
(8) Fill basin and test switch operation.
SSM33/SSM33I SHAFT SEAL REPLACEMENT
(1) Remove the oil fill plug located on the top of the motor
housing and drain the oil in the housing. Properly
dispose of the used oil. Do not reuse old oil since it
may contain water from seal failure.
(2) Lay the pump on its side. Remove the six screws
holding the suction bottom onto the volute case.
Remove the suction bottom.
(3) Insert a slotted screwdriver through the center of the
impeller hub into the slot in the shaft. With a rubber
mallet, carefully tap the impeller in a counter rotating
direction while holding the shaft with the screwdriver.
(4) Remove the rotating portion (ceramic) of the seal with
fingers. Pry on the stationary portion (carbon) with a
pair of slotted screwdrivers to remove from volute
casing. Discard the old seal assembly parts. NEVER
USE OLD SEAL PARTS, REBUILD PUMP WITH ONLY
NEW SEAL ASSEMBLY.
(5) Thoroughly clean the shaft and volute casing with a
clean cloth. If the drained oil showed signs of water,
then the motor should be air dried for several days to
remove any remaining moisture.
(6) Carefully remove the new seal assembly from the
package. Add a film of new oil to the rubber O.D. on the
stationary portion (carbon), and insert into the seal
cavity on the volute casing. Using a pushing tool (a
piece of PVC pipe works well), push on the rubber
portion of the stationary seal until it is evenly seated
into the seal cavity. With a clean cloth, carefully wipe
the seal face.
(7) Remove the rotating portion (ceramic) from the package
and carefully wipe with a clean cloth. Add a film of new
oil onto the motor shaft. Slide the rotating portion over
the shaft with the rubber surface of the seal facing away
from the stationary seal face. Center the seal on the
shaft.
(8) Place the impeller onto the shaft. Screw the impeller
clockwise onto the shaft using a screwdriver to hold the
shaft from turning and tighten impeller. Check to see
that the impeller spins freely after tightening.
(9) Replace the suction bottom onto the volute casing and
retain with the six screws. Evenly tighten screws.
(10) Replace oil in the motor housing using only Myers
submersible transformer oil. The level should be 3/4”
below the top of the motor housing. Check with dip stick
to assure that the pump is properly filled.
(11) Plug pump into grounded receptacle to test operation.
Pump must run quiet and free of vibration.
SRM4 SHAFT SEAL REPLACEMENT
(1) Remove the oil fill plug located on the top of the motor
housing and drain the oil in the housing. Properly
dispose of the used oil. Do not reuse old oil since it may
contain water from seal failure.
(2) Remove the three cap screws holding the volute case
onto the seal plate. Lift the motor assembly up and out
of the volute case.
(3) Lay the motor assembly on its side. Insert a slotted
screwdriver into the slot in the center of the shaft. With
a rubber mallet, carefully tap the impeller in a counter
rotating direction while holding the shaft with the
screwdriver.
(4) Remove the rotating portion (ceramic) of the seal with
fingers. Pry on the stationary portion (carbon) with a
pair of slotted screwdrivers to remove from volute
casing. Discard the old seal assembly parts. NEVER
USE OLD SEAL PARTS. REBUILD PUMP WITH ONLY
NEW SEAL ASSEMBLY.
(5) Thoroughly clean the shaft and volute casing with a
clean cloth. If the drained oil showed signs of water,
then the motor should be air dried for several days to
remove any remaining moisture.
(6) Carefully remove the new seal assembly from the
package. Add a film of new oil to the rubber O.D. on the
stationary portion (carbon), and insert into the seal
cavity on the volute casing. Using a pushing tool (a
piece of PVC pipe works well), push on the rubber
portion of the stationary seal until it is evenly seated into
the seal cavity. With a clean cloth, carefully wipe the
seal face.
(7) Remove the rotating portion (ceramic) from the package
and carefully wipe with a clean cloth. Add a film of new
oil into the motor shaft. Slide the rotating portion over
the shaft with the rubber surface of the seal facing away
from the stationary seal face. Center the seal on the
shaft.
(8) Place the impeller onto the shaft. Screw the impeller
clockwise onto the shaft using a screwdriver to hold the
shaft from turning and tighten impeller. Check to see
that the impeller spins freely after tightening.
(9) Place the pump motor assembly upright and set it into
the volute case. Replace the four cap screws and
tighten.
(10) Replace oil in the motor housing using only Myers
submersible transformer oil. The level should be 3/4”
below the top of the motor housing. Check with dip stick
to assure that the pump is properly filled.
(11) Plug pump into grounded receptacle to test operation.
Pump must run quiet and free of vibration.
13800A991