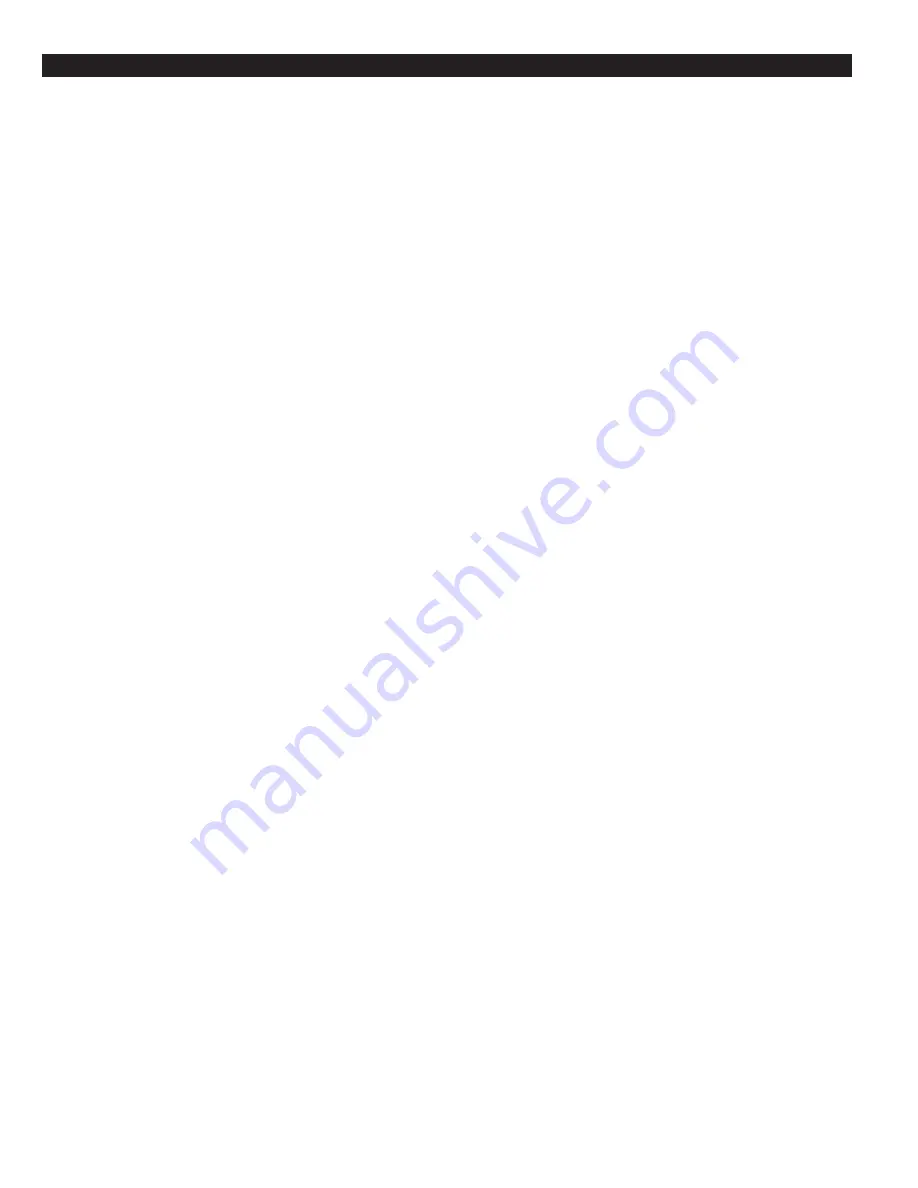
AS3000 Controller Troubleshooting
When enabling the controller presents a problem, make sure that the
following conditions are present:
DC voltage above 8VDC all the time
Good solid ground (-V battery) connected at the terminals in the
MGC2000 enclosure. A "daisy chained" ground that is looped from
battery to frame to starter to Ac alternator to ground rod to MGC2000 is
not a reliable installation. When dealing with a potential for high
current, it is imperative that the ground for the controller and the battery
be as close and resistance free as possible.
When the controller can’t be enabled
If the controller won’t run or if the starter is being re-engaged after the
controller is running, then one of two states exists: the speed signal
source - magnet pickup, AC voltage, or crank disconnect switch -
supplying the AS3000 is misconnected/not operating properly, or the
AS3000 has not been properly programmed. Verify that the speed signal
source is functional, and then if the problem persists, reset/recapture the
speed signal settings (See the AS3000 section on "controller
programming").
1.
If the controller is totally unresponsive check the following:
a.
Ground is applied to terminal 1.
b.
+V battery is applied to terminal 2
c.
The operation jumper is present between terminals 23 and
33 or if a key switch is in the system make sure that it is in
the run/on position
d.
+V battery is at least 8 volts.
2.
If the controller attempts to initiate start but either just
"bumps" the crank or resets without actually cranking:
Verify that the +V battery remains above 8 volts DC as
measured across terminals 1 and 2 when the crank cycle is
initiated.
3.
Verifying the LED’s actually work:
a.
Ground the LAMP TEST input (terminal 35 on the rear of
the User interface) to terminal 1
4.
If the starter will not disengage properly, or continues to cycle
crank even after the engine starts:
a.
If the application is using AC frequency for crank
disconnect and overspeed, then check the AC connections
to terminals 20 & 21. AC voltage MUST be present when
the engine is past crank disconnect speed.
b.
If the application is using magnetic pickup crank
disconnect/overspeed, make sure that the wiring is correct
and that the output is at least 3Vrms as measured at
terminals 17 & 19 (18 is the shield/screen wire)
c.
If the run signals are present when the genset is running and
it still cycle cranks, then the crank disconnect/overspeed
settings were captured wrong. See page "Speed calibration"
on page 6.
5.
If the system tries to immediately crank, without a proper start
signal:
Verify with a voltmeter that terminal 16 is connected to +V
battery, and that terminal 9 is not grounded.
6.
If AS3000 is consistently shutting down on overspeed when
there is:
a.
No ground signal applied to terminal 14 AND
b.
No overspeed condition is truly present, then either the
crank disconnect/overspeed settings were captured wrong,
(See page "Speed calibration" on page 6) OR
c.
There is a noise source on the speed input:
i.
For AC Speed driven units, this can take the form of ‘dirty’
loads on AC – like variable frequency drives, large
inductive loads etc – typically indicating a poorly grounded
AC side.
ii.
If the system is using a magnetic pickup, the shield is
improperly grounded (usually at both ends instead of just
one!)
iii.
If the system is spark ignited, the ignition system should
use resistive spark plugs and plug wires, and the magnetic
pickup wiring should be routed as far away from the plugs
and plug wires as possible.
7.
If the preheat, fuel, or crank outputs do not seem to be working
(not providing voltage out):
Disconnect the load from the suspect terminal(s), and while
measuring the voltage on the terminal, initiate a start. If the
voltage is there during this test, you have exceeded the current
rating of the FET output and must add a slave relay to get the
total current draw back under 2 (or 5) Amps per output.
8.
If the system tries to immediately crank, without a proper start
signal:
Verify with a voltmeter that terminal 16 is at +V battery, and
that terminal 9 is not grounded.
9.
If the engine consistently dies shortly after startup:
Make sure that the oil pressure and engine temperature fault
switches are operating properly.
MGC-02030N page 7 of 8
Controller Troubleshooting