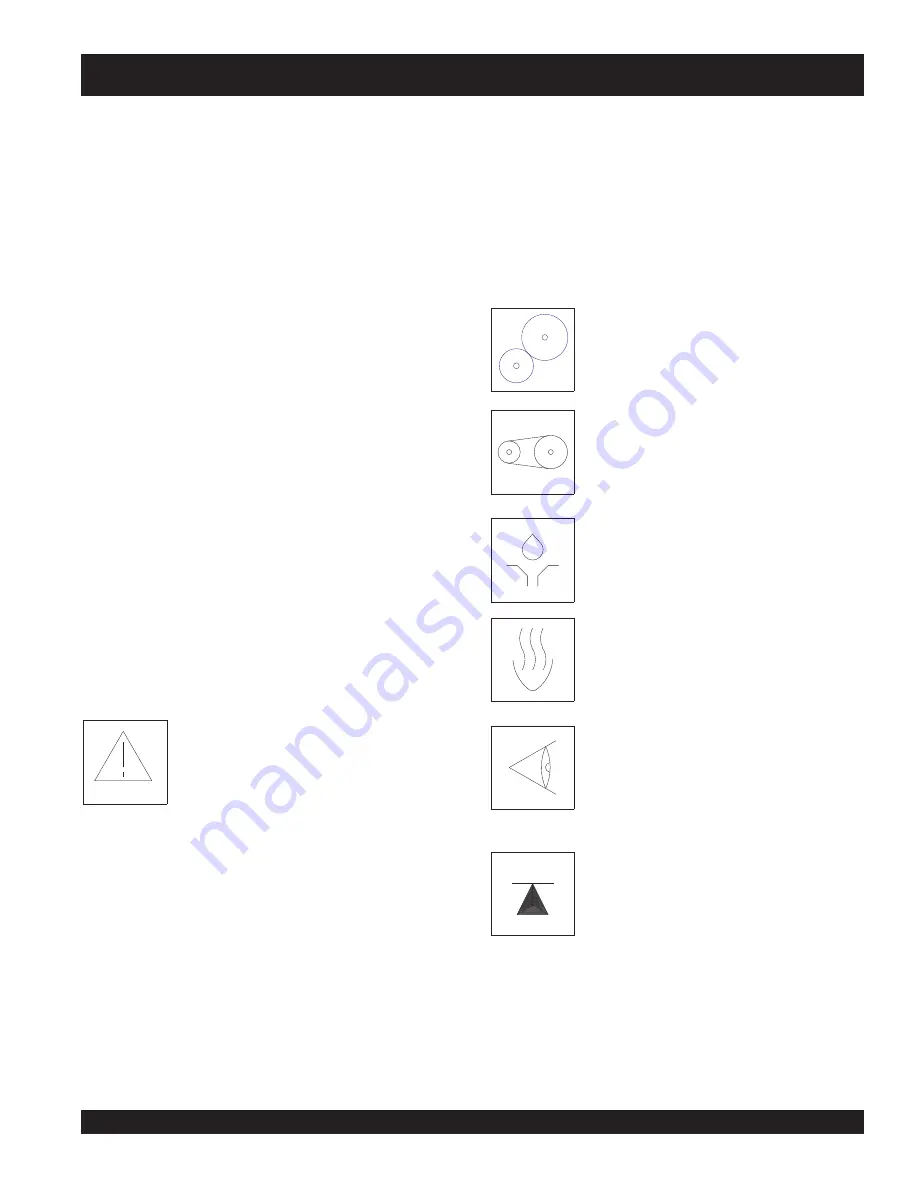
J-SERIES TROWEL — OPERATION AND PARTS MANUAL — REV. #3 (07/07/10) — PAGE 7
FUEL
FUEL
Handle fuel safely. Motor fuels are highly flammable and can be
dangerous if mishandled. Do not smoke while refueling. Do not
refuel if the engine is hot or running.
Always shut off fuel flow with the fuel line valve after every
machine use. Never store the machine with fuel in the tank for any
extended period of time.
Clean up spilled fuel immediately!
PERSONAL PROTECTIVE EQUIPMENT
Always wear proper clothing while operating this equipment.
Protective clothing includes (but is not limited to): boots, long
sleeve shirt, long pants, gloves, hearing protection and safety
eyeglasses. Consult with the construction site foreman to
determine what protective clothing is required on the construction
site.
HAZARDOUS MATERIALS
Exposure and mishandling of hazardous material can cause
personal injury or damage the environment. Potentially hazardous
material used on this machine may include the following:
lubricants, fuel, paints and adhesives.
Take care to handle hazardous materials properly. MSDS
information sheets are available upon request.
BE PREPARED FOR EMERGENCIES
Always know the location of the nearest fire extinguisher and first
aid kit. Know the location of the nearest telephone. Also know the
phone numbers of the nearest ambulance, doctor and fire
department. This information will be invaluable in an emergency.
MAINTENANCE SAFETY
Caution! Disconnect spark plug wires before
attempting service.
Before attempting maintenance on this
machinery, know the procedure and have the
correct tools. Always make sure that the machine is stopped and
the spark plug wires are disconnected before attempting service.
Securely support any machine components that must be raised
for service (i.e. trowel arms). Never lubricate the machine or
attempt service on a running machine. Always allow the machine
proper time to cool before servicing.
Keep machinery in proper running condition. Make sure that
there is no buildup of concrete, grease, oil or debris. Keep all
parts properly installed. Fix damage immediately and always
replace worn or broken parts.
Dispose of potentially hazardous waste properly. Examples of
potentially hazardous waste are: motor oil, fuel and filters. Use
rigid containers for trapping these items. Do not use old food or
beverage containers, someone may be mislead. Do not pour
waste oil or fuel directly onto the ground, down a drain or into any
water source.
Inquire what the proper disposal procedures are for waste fuel
and oil in your local area.
MACHINE SAFETY DECALS
Gear Drive
— Located on the gearbox.
Belt Drive
— Located on the belt guard.
Lubrication
— Located near the fill hole for
gearbox lubricant.
Hot!
— Located on the muffler shield.
Check
— Located near the oil level check for
the gearbox.
Lifting point
— Located on the lift bale.