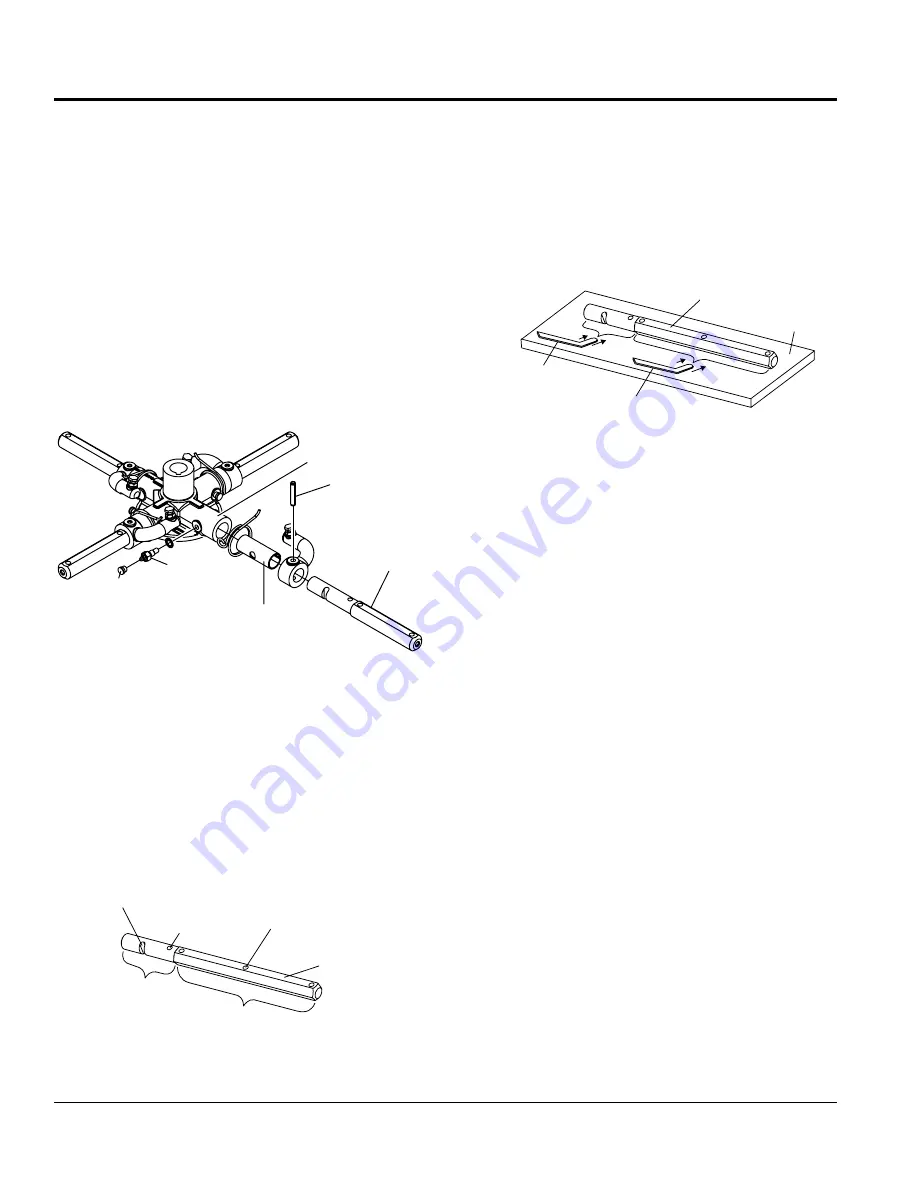
PAGE 38 — BS90C WALK-BEHIND TROWEL • OPERATION AND PARTS MANUAL — REV. #0 (9/4/15)
MAINTENANCE
TROWEL ARM REMOVAL
1. Each trowel arm is held in place at the spider plate
by a hex head bolt (zerk grease fitting) and a roll
pin. Remove both the hex head bolt and the roll
pin (Figure 57) from the spider plate.
2. Remove the trowel arm from the spider plate.
3. Should the trowel arm inserts ( bushing ) come out with
the trowel arm, remove the bushing from the trowel arm
and set aside in a safe place. If the bushing is retained
inside the spider plate, carefully remove the bushing
4. Examine the trowel arm bushing insert (Figure 57),
clean if necessary. Replace bushing if out of round
or worn.
Figure 57. Trowel Arm Removal
CHECKING TROWEL ARM STRAIGHTNESS
Trowel arms (Figure 58) can be damaged by rough
handling, such as dropping the trowel on the pad, or
by striking exposed plumbing, forms, or rebar while in
operation. A bent trowel arm will not allow the trowel to
operate in a smooth fluid rotation. If bent trowel arms are
suspect, check for flatness as follows:
Figure 58. Trowel Arm
TROWEL
ARM
ROLL PIN
SPIDER PLATE
ZERK
GREASE
FITTING
CAP
BUSHING
TROWEL ARM
ROUND SHAFT
SECTION
ROLL PIN
HOLE
BLADE ATTACHMENT
BOLT HOLE
FLAT OF HEXAGONAL
SHAFT (TOP OF ARM)
LEVER
MOUNTING
SLOT
TROWEL ARM
HEXAGONAL (HEX)
SHAFT SECTION
1. Use a thick steel plate, granite slab or any surface
which is true and flat, to check all six sides of each
trowel arm for flatness (Figure 59).
2. Check each of the six sides of the trowel arm (hex
section). A feeler gauge of .004 inch (0.10 mm) should
not pass between the flat of the trowel arm and the test
surface along its length on the test surface.
Figure 59. Checking Trowel Arm Flatness
3. Next, check the clearance between the round shaft
and the test surface as one of the flat hex sections of
the arm rests on the test surface. Rotate the arm to
each of the flat hex sections and check the clearance
of the round shaft. Use a feeler gauge (Figure 60) of
.005 inch (0.127 mm). Each section should have the
same clearance between the round of the trowel arm
shaft and the test surface.
4. If the trowel arm is found to be uneven or bent, replace
the trowel arm.
TROWEL
ARM
TROWEL
ARM
FLAT TEST
SURFACE
FEELER GAUGE
(.004 IN/0.10 MM)
FEELER GAUGE
(.005 IN/0.127 MM)
Содержание BS90C
Страница 70: ...PAGE 70 BS90CWALK BEHINDTROWEL OPERATION AND PARTS MANUAL REV 0 9 4 15 EX27 CRANKCASE ASSY ...
Страница 72: ...PAGE 72 BS90CWALK BEHINDTROWEL OPERATION AND PARTS MANUAL REV 0 9 4 15 EX27 CRANKSHAFT ASSY ...
Страница 74: ...PAGE 74 BS90CWALK BEHINDTROWEL OPERATION AND PARTS MANUAL REV 0 9 4 15 EX27 MUFFLER ASSY ...
Страница 76: ...PAGE 76 BS90CWALK BEHINDTROWEL OPERATION AND PARTS MANUAL REV 0 9 4 15 EX27 AIR CLEANER ASSY ...
Страница 78: ...PAGE 78 BS90CWALK BEHINDTROWEL OPERATION AND PARTS MANUAL REV 0 9 4 15 EX27 GOVERNOR ASSY ...
Страница 80: ...PAGE 80 BS90CWALK BEHINDTROWEL OPERATION AND PARTS MANUAL REV 0 9 4 15 EX27 BLOWER ASSY ...
Страница 82: ...PAGE 82 BS90CWALK BEHINDTROWEL OPERATION AND PARTS MANUAL REV 0 9 4 15 EX27 RECOIL STARTER ASSY ...
Страница 84: ...PAGE 84 BS90CWALK BEHINDTROWEL OPERATION AND PARTS MANUAL REV 0 9 4 15 EX27 FUEL TANK ASSY ...
Страница 86: ...PAGE 86 BS90CWALK BEHINDTROWEL OPERATION AND PARTS MANUAL REV 0 9 4 15 EX27 CARBURETOR ASSY ...
Страница 88: ...PAGE 88 BS90CWALK BEHINDTROWEL OPERATION AND PARTS MANUAL REV 0 9 4 15 EX27 IGNITION COIL ASSY ...
Страница 90: ...PAGE 90 BS90CWALK BEHINDTROWEL OPERATION AND PARTS MANUAL REV 0 9 4 15 EX27 OIL SENSOR ASSY ...
Страница 93: ...BS90CWALK BEHINDTROWEL OPERATION AND PARTS MANUAL REV 0 9 4 15 PAGE 93 NOTES ...