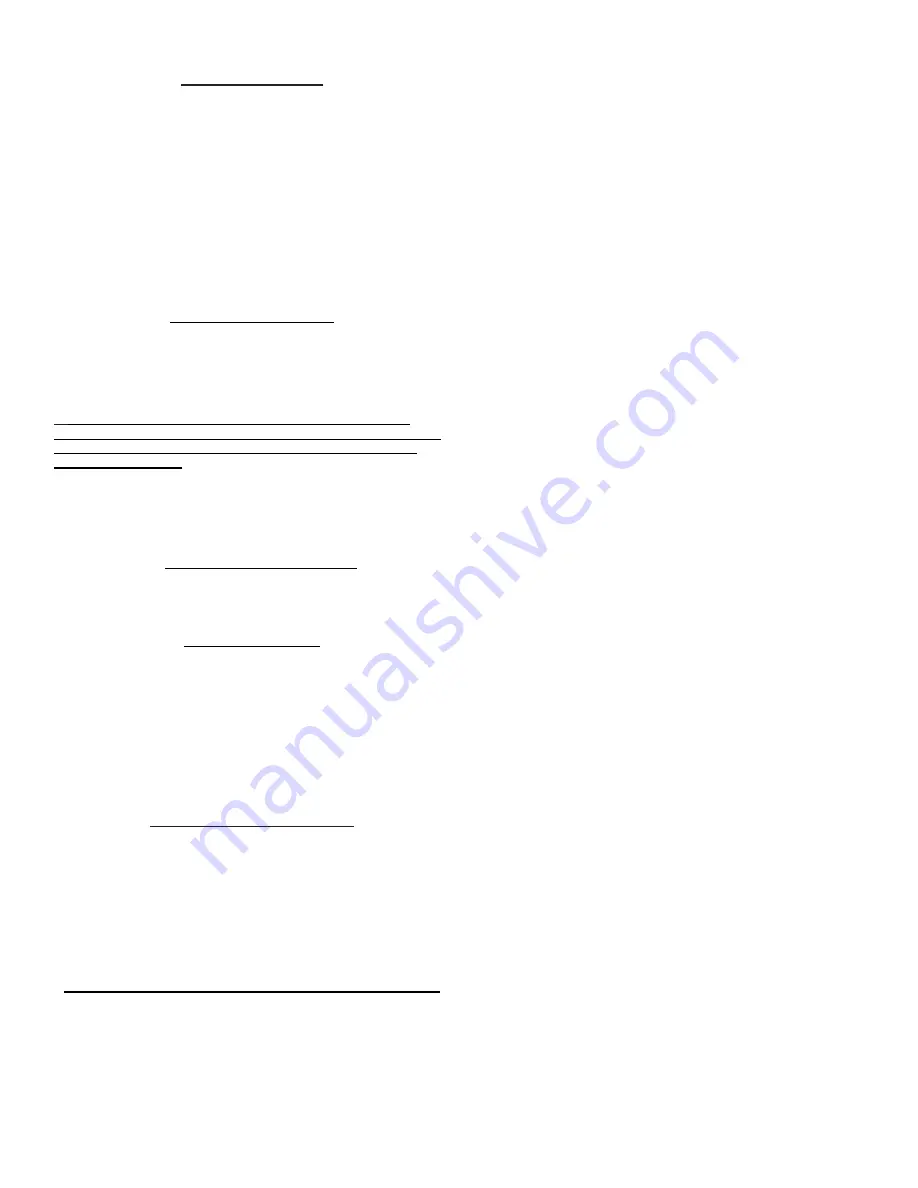
Propeller Removal
Replace and/or repair the propeller when it shows signs of damage or excessive
wear. Lack of power or reduced thrust in mud is an indication of prop wear.
A
bent propeller causes vibration that will lead to driveline failure.
- Place a large wrench on the nut located behind the propeller. If available,
add a long piece of tube or pipe to the wrench for leverage. Use a Mud Buddy
prop wrench, to unscrew the propeller. You can also make a prop wrench by
drilling a 7/8” hole in a 1.25" X 3’ section of flat bar steel.
- Usually, the prop will be threaded on very tightly and it will require
considerable force to unscrew. Do not hit the propeller with a hammer, this
never loosens the prop, rather, it causes damage. Call us if you have difficulty
removing a prop. Leverage is the key.
Propeller Installation
Inspect the nuts and washers and replace as needed, using only the Mud Buddy
nut set. They are of special design which ensures the prop runs perfectly
straight on the drive shaft. Ensure two propeller washers are installed on the
drive shaft prior to mounting the propeller.
-
Never force a tight fitting propeller on the drive shaft. The shaft is
constructed of a very hard steel and the propeller is stainless steel. The two
will jam and the propeller will neither go on or off, requiring extensive
machine work to remove.
Instead, use a wire brush to clean the threads. It
may also be necessary to run a 7/8” coarse die-nut over the threads. You may
also need to run a 7/8" coarse TPI tap through the propeller to ensure the
threads are clear of any burrs.
- Coat the drive shaft threads with marine grease or never-seize.
- Install the propeller
(use gloves, the prop might be sharp)
with cupped ends
toward you. Install in this order— two bronze washers, propeller, another
bronze washer, jam nut, and finally, the nylon lock nut. Some props only have
one nut.
Warranty Service
Your Mud Buddy is designed to last you many years. Warranty items are
repaired by authorized Honda, Vanguard, Robin, Kohler, or Kawasaki engine
repair centers and the drive/frame by Mud Buddy Service Centers. Parts and
tool information and prices are available from Mud Buddy. Tools may be
purchased or rented for a reasonable fee, plus shipping. Tools are available,
free for your use, to complete service work during the warranty period, and may
be rented thereafter. You are important to us, so call whenever you have
questions or need assistance.
Prior approval by Mud Buddy is required
before completing any warranty work.
Drive Assembly Inspection
The most common reason for drive failure is a bent propeller. Replace an
unbalanced propeller immediately. A common symptom of a bent propeller bent
driveshaft is a vibration at mid and full throttle. If you encounter either,
remove the propeller for balancing. While the propeller is removed, run the
engine at an idle checking the shaft for straightness. Notice the small gap
between the bearing cap and drive shaft. Watch the shaft as it rotates. If the
shaft is bent, it will be obvious.
Outdrive Removal , Belt Replacement or Rebuild
Simply remove the top brace and nine face bolts from the outdrive. If repairs
are needed, you can do it yourself or send the outdrive to Mud Buddy. We have
convenient outdrive UPS shipping boxes that we will send to you if needed.
Coordinate any warranty work with your Mud Buddy dealer.
Belt Tension or Replacement Procedure:
You can purchase a belt tensioning kit for $19.95 which contains the hex
wrench, belt tensioning tool, silicone sealer and photo instructions. The tool
may also be rented for $10 to cover shipping and handling. Call us at
801.352.8011.
You can also go to our web page and click on customer page for photo
instructions. Your user name is outdoor and password is fun. All lower case.
Check the web page often for product updates, service tips and more
The Goodyear Eagle PD belt is tensioned by moving the outdrive up and down
on the engine and engine mount face. The adjustment bolt is located on the
bottom inside of the aluminum outdrive.
- Remove the outdrive top access cover. (says Mud Buddy patented
HyperDrive on the cover) Loosen the four engine face bolts. Do not remove the
bolts, just loosen them enough to allow the cast aluminum outdrive to slide in
the bolt slots.
- Loosen the outdrive belt tension bolt about a half inch. It is located on the
lower back end of casting.
- Locate the four lower cast aluminum mounting bolts. They are above the
outdrive adjustment bolt on the outside of the rear lower end of the casting.
Loosen them slightly. Again, just enough so the aluminum casting can slide up
and down to tension the belt.
- If retentioning, skip the following 9 steps and go to
*
below.
- Squeeze the belt together. This will cause the outdrive housing to slide up in
the adjustment slots. Tighten one of the engine face bolts to hold the outdrive
in the up position. This will help you get the belt back on the drive sprocket
later.
- Remove the five lower outdrive bolts and top brace. Clean the old silicone
off the casting mounting face.
- Place a new belt on the sprocket. Ensure the belt is facing the correct
direction so the teeth and belt mesh.
- Place a thin bead of silicone on the main outdrive casting.
- With a few bolts in hand, hold the drive tube section in place. Tighten the
face bolts.
- Slip the belt up and over the top sprocket. Turn the propeller to ensure the
belt and sprockets are engaged.
- Remove each of the lower four adjustment bolts, one-by-one, and place
silicone on the threads. Replace and tighten snugly, but not too tight yet.
- Remove each of the four engine face bolts, one-by-one and add a small drop
of blue 243 loctite to each. Tighten all the face bolts snug, but not so tight that
it restricts tightening of the belt.
- Adjust the belt tension by turning the tension bolt.
*
Locate the belt tension access hole on the right side of the casting. Remove
the hole plug.
- Check the belt tension with a Mud Buddy belt tension tool. The procedure is
very simple. The belt should move 1/4” with 18-20 pounds of force from the
belt tension tool. No more than 18 pounds for the Honda and 29, 32 and 35
large block Vanguards. The tool is inserted through the access hole. While
holding a tape measure across the front of the belt, depress the belt with the
tool, moving the belt 1/4”. The o-ring on the tool will slide down its inner shaft
and mark how many pounds it took to move the belt 1/4”. Adjust the rear
casting tension bolt as needed to get the pounds of belt tension. Lock
the tension bolt in place with its jam nut.
4