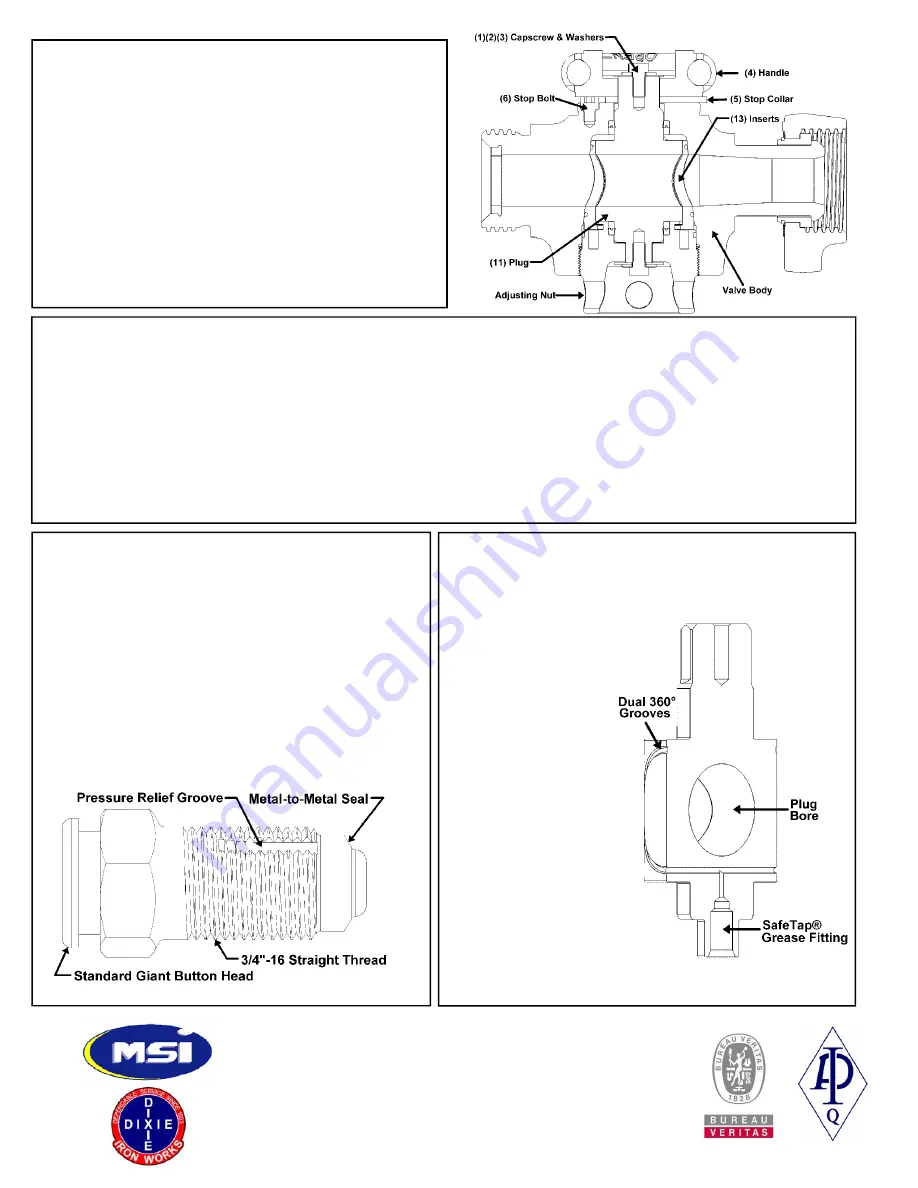
Disassembly
1. Remove
the
top
capscrew
(1)
, washers
(2)(3)
, handle
(4)
, and
stop collar
(5)
.
2. Secure the valve assembly with the adjusting nut facing up.
3. Using a bar, unscrew the adjusting nut counter-clockwise until
it disengages from the valve body. Leaving the bottom cap-
screw
(15)
in place will allow the entire internal assembly to be
removed from the valve at once.
4. Remove the bottom capscrew
(15)
and washers
(2)(3)
.
5. Remove the plug
(11)
and inserts
(13)
from the adjusting nut.
6. Remove the insert o-rings
(12)
, adjusting nut o-ring
(14)
, and
plug seals
(8)
.
7. Remove all grease and debris from all valve components.
8. Remove the grease fitting
(7)
from the body or plug
(11)
.
Inspection and Repair
1. After degreasing the parts, visually inspect for wear, corrosion, or any other physical damage.
2. Inspect the primary sealing surface of the plug
(11)
and inserts
(13)
for any scratches or dings. Parts with heavy dings or deep
scratches in the sealing surfaces should be replaced. For light wear or superficial blemishes, use 600-grit sandpaper along with a
solvent to polish.
3. All surfaces which contact the elastomeric seals must be smooth and free of rust and pitting. Use sandpaper to polish. Parts with
excessive pitting and rust should be replaced.
4. Lubricate and screw the adjusting nut (without the o-ring) completely into the valve body to check for damaged threads. It should
turn easily all the way.
5. Check
the
roll
pins
(10)
in the valve body by gently sliding a set of inserts
(13)
into the valve. The inserts should move freely up and
down the length of the roll pin slots without interference.
6. Inspect the grease fitting
(7)
for damaged threads or sealing surface.
SafeTap® Grease Fitting
SafeTap® grease fittings are design to provide maximize safe
operation in the field with these key features:
•
The unique metal-to-metal seal eliminates wetted threads
and pipe taps. Since the threads do not perform a sealing
function they do not require Teflon tape or other sealing
aids.
•
The heavier cross section stands up better to impacts.
•
Each fitting has a slot machined through the threads which
serves as a pressure relief path in the event of a leak.
•
The metal-to-metal seal and the pressure relief slot of the
SafeTap® grease fitting also allows a means to safely bleed
any residual internal pressure.
GreaSeal® Plug
The patented GreaSeal® plug is designed to provide maximum
lubrication in the harshest field conditions. Key features include:
•
The only plug that
allows greasing in the
opened or closed po-
sition while in service.
•
Dual 360° grease
channels
•
Forces grease into
360° of the seal area
when closed.
•
Allows for complete
distribution of lubricant
immediately prior to
opening a valve when
exposure to high tem-
peratures and well
fluids may have com-
promised the existing
grease.
•
Greasing in the closed
position can stop or
significantly slow
leaks in valves with
worn or damaged
parts.
MSI is a Division of Dixie Iron Works, Ltd.
300 West Main * Alice, Texas 78332 * USA
ph: 800.242.0059
ph: 361.664.6597
fax: 361.664.4840
email: [email protected]
www.plugvalve.com