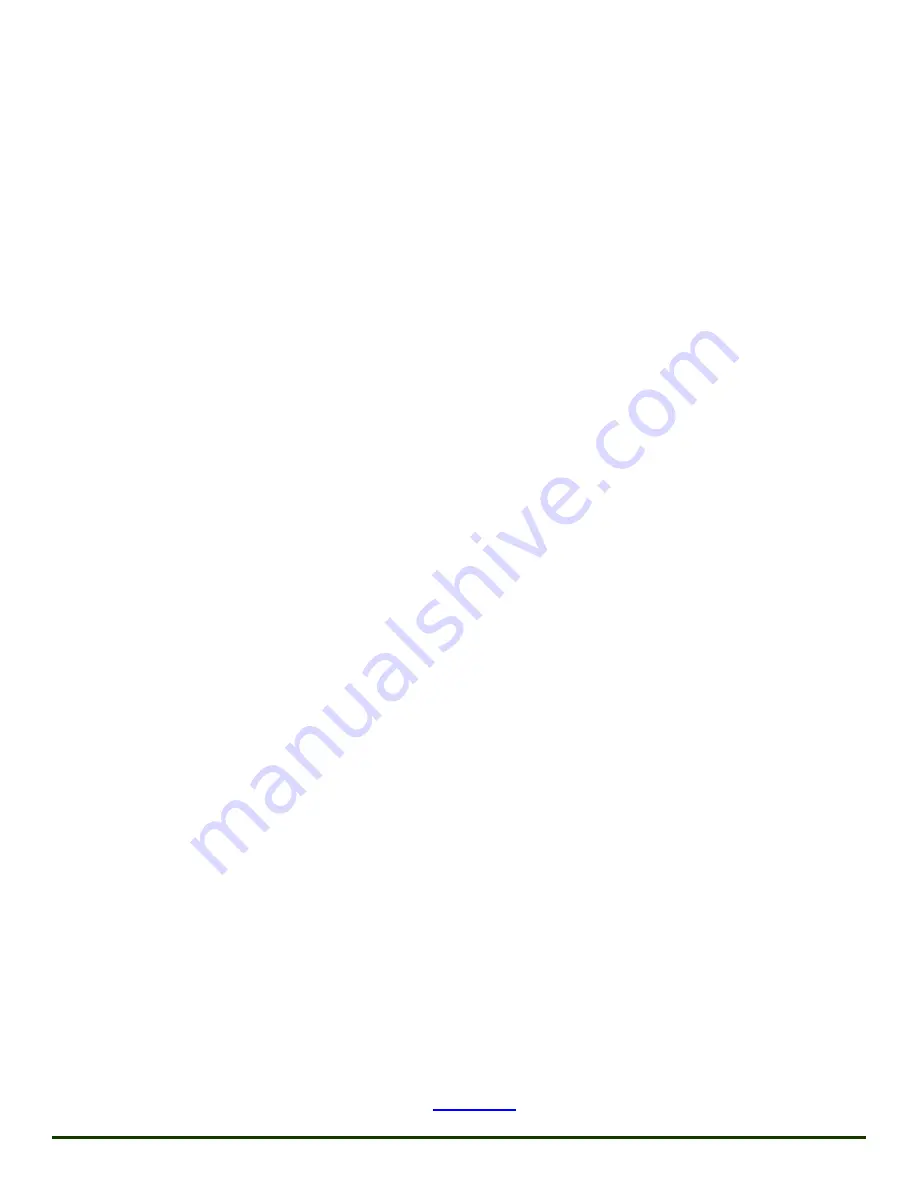
9.3
Replacing Valves and Seats
The valves, springs, and seats should be inspected for wear or corrosion after each well service job and replaced
as needed.
CAUTION:
Do not perform any service on the fluid end until you have verified that there is no
pressure in the discharge system, the suction supercharge pump is off and isolated and suction pressure
has been relieved. Do not perform service on the fluid end with the drive engine running. If there is a
bladder type pulsation dampener on the system, either isolate it, or bleed the nitrogen pressure from the
bladder. Failure to follow these precautions can lead to serious injury.
1)
After heeding the safety precautions, remove the suction and discharge covers, and/or gauge
connection(s), using the valve cover tool and a 10 lb. hammer.
MSI Hybrid™ Well Service Pump Enhancement – The suction cover nuts consist of a thread half and a
gland half and are attached with a shoulder screw to allow one piece extraction yet also allow the two
parts to rotate independently. This design effectively prevents seal bore galling and scoring that is
common in one piece cover nuts.
CAUTION:
Well service fluid will be trapped between the inlet and outlet valves and will spill out
when removing the suction valve covers. Expectation of and preparation for this is important for safety
and environmental reasons. A catch pan, appropriate absorbent materials, and proper PPE will be
needed.
2)
Remove the spring and discharge valve from the top of the fluid cylinder.
3)
Rotate the pump by hand until the plunger is clear of the bore being serviced. Do this for each
remaining bore.
4)
Remove the suction valve stop from the fluid cylinder by lifting the retaining spring from its groove
then turning the stop approximately 90 degrees. A flathead screwdriver may be used to assist in
disengaging the spring. Be careful to not damage the seal bores during extraction. See following
drawing.
MSI Hybrid™ Well Service Pump Enhancement – By incorporating an integral anti-rotation device
directly into the valve stop MSI has increased the clearance space directly ahead of the fluid end
plunger. The result is a safer operating pump with more fluid escape volume.
5)
Remove the valve spring and suction valve.
6)
Remove the discharge and suction valve seat using the valve seat tool (FEC0113 or FEC0114). The
tapered bore in the fluid cylinder must be thoroughly cleaned and lightly hand polished with 220-240
grit Emory cloth prior to installing new seats.
7)
Thoroughly clean each new valve seat OD taper before installing. Do not use any grease, sealer, etc.
as the valve seat must be installed clean and dry. After hand tight installation of the valve seat, press
the valve seat into the taper using a heavy steel bar with a Teflon or wood pad, then hammer the
valve seat into the taper. Final seating of the valves takes tremendous force and must be
accomplished by operating the pump per
Section 6.1
.
Revision K 03/12/2019
MSI - A Division of Dixie Iron Works, Ltd. All rights reserved.
Page 51