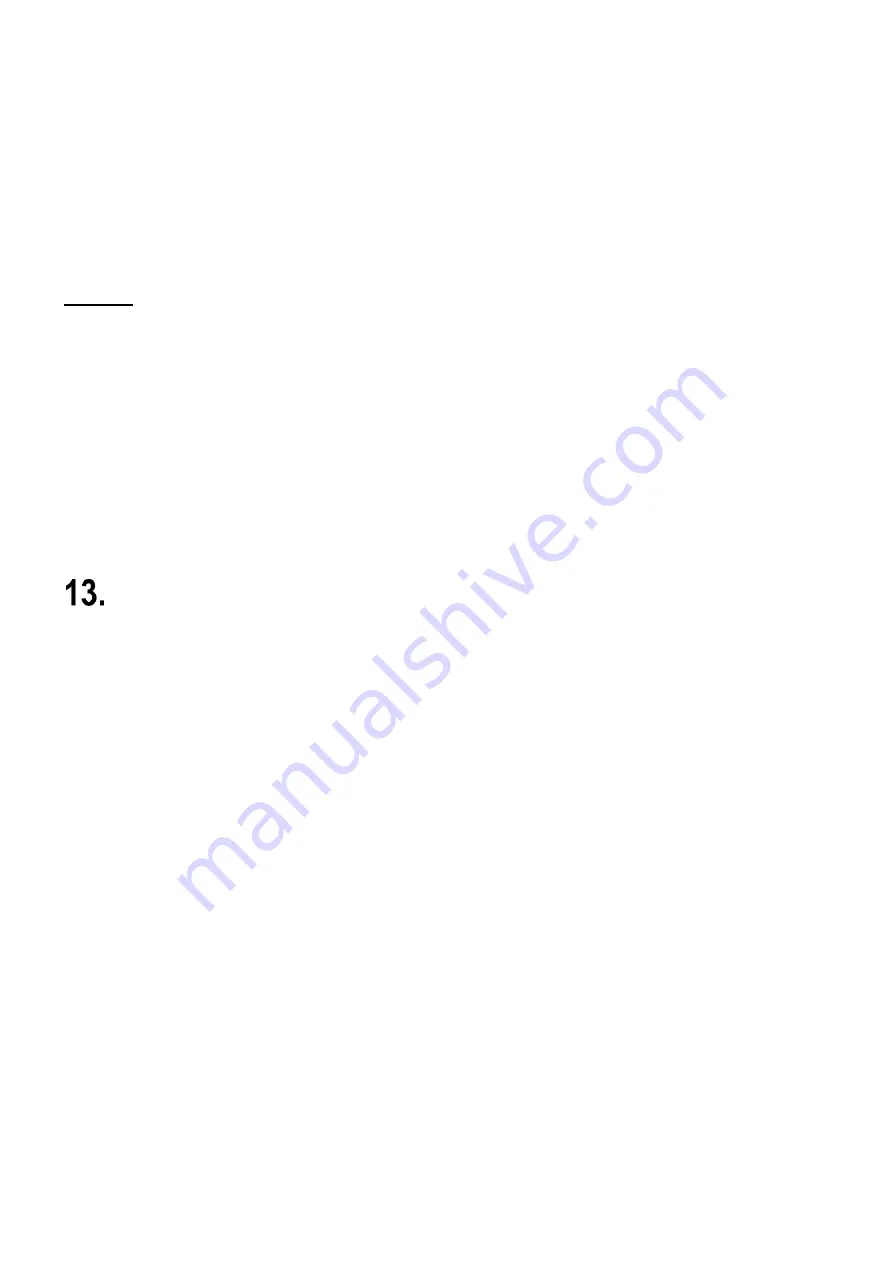
Fm210_01b_oi_e.docx / Nov-20
Page 36 / 40
To obtain an optimal correction over a wide frequency range, the Base Correction value must first be
set at low frequency (approx. 10 kHz). Here the other two parameters (Correction Freq and
Correction Value) are set to zero. Now start with values at 25 and check the deviation of the
differential counter.
Then increase the frequency to the maximum value. The differential counter will show a higher
deviation. These two values can now be transferred to the two parameter values.
Here the parameter Correction Freq is overwritten with the value 500 for 500kHz, for the parameter
Correction Value the value 1500 is entered. After these settings, the differential counter decreases to
a value between -40 and -20. (see example below)
Example:
10kHz
Difference counter moves around zero at Correction Basis = 25
500kHz
Difference counter moves around -1590
Now the Correction Freq is set to 500 and Correction Value to 1500.
500kHz
Difference counter now moves around -40 to -20
If the frequency is now reduced to 250kHz, the differential counter moves by -20 to -10.
The position shift has approximately halved.
Overshoot
With the overshoot parameter the maximum allowed frequency change at the output can be set. With
a setting of 10, the output frequency is changed by +/-10% to reduce the differential counter deviation.
This prevents that any occurring difference increments are reduced too quickly and with excessive
acceleration. For the Trim and Offset commands, the settings must be made in such a way that not
more increments are entered into the differential counter than can be reduced. If this is not done, the
drive may run longer even when the Trim command is reset, because there are still increments in the
differential counter and these cause a further shift.
But the overshoot also acts as a frequency limit or compensation limit, so that for example the output
frequency does not exceed a certain value at constant input frequency.