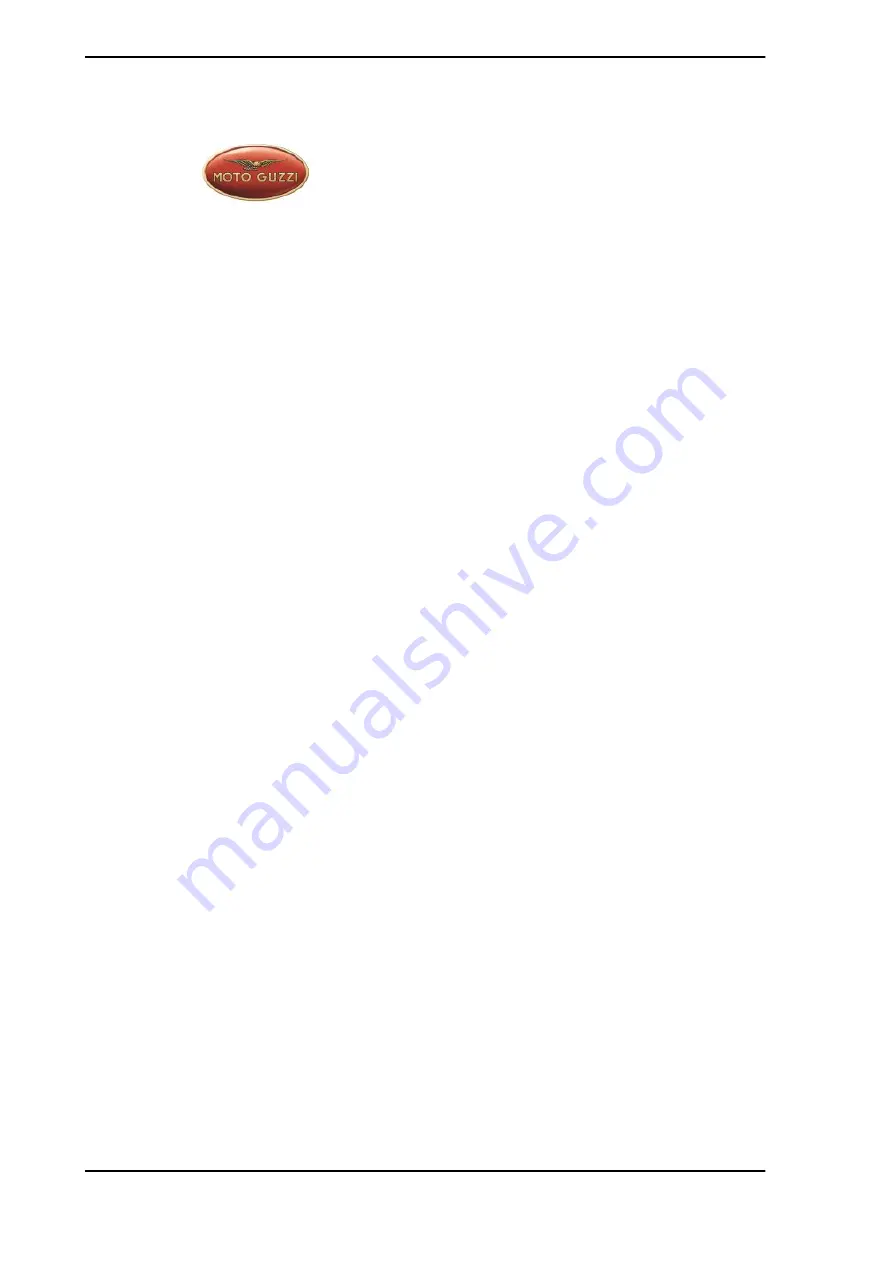
SERVICE STATION
MANUAL
V7 II ABS
THE VALUE OF SERVICE
As a result of continuous updates and specific technical training programmes for Moto Guzzi products,
only
Moto Guzzi
Official Network mechanics know this vehicle fully and have the specific tools necessary
to carry out maintenance and repair operations correctly.
The reliability of the vehicle also depends on its mechanical conditions. Checking the vehicle before riding
it, its regular maintenance and the use of
original Moto Guzzi spare parts
only are essential factors!
For information on the nearest
Official Dealer and/or Service Centre
consult our website:
Only by requesting Moto Guzzi original spare parts can you be sure of purchasing products that were
developed and tested during the actual vehicle design stage. All Moto Guzzi original spare parts undergo
quality control procedures to guarantee reliability and durability.
The descriptions and images in this publication are given for illustrative purposes only and are not binding.
While the basic characteristics as described and illustrated in this booklet remain unchanged, Piaggio &
C. S.p.A. reserves the right, at any time and without being required to update this publication beforehand,
to make any changes to components, parts or accessories, which it considers necessary to improve the
product or which are required for manufacturing or construction reasons.
Not all versions/models shown in this publication are available in all countries. The availability of individual
versions should be checked with the Official Moto Guzzi sales network.
The Moto Guzzi brand is owned by Piaggio & C. S.p.A.
© Copyright 2016 - Piaggio & C. S.p.A. All rights reserved. Reproduction of this publication in whole or
in part is prohibited.
Piaggio & C. S.p.A. Viale Rinaldo Piaggio, 25 - 56025 PONTEDERA (PI), Italy
Содержание V7 II ABS
Страница 1: ...SERVICE STATION MANUAL 2Q000105 V7 II ABS ...
Страница 4: ......
Страница 6: ...INDEX OF TOPICS CHARACTERISTICS CHAR ...
Страница 44: ...INDEX OF TOPICS SPECIAL TOOLS S TOOLS ...
Страница 47: ...INDEX OF TOPICS MAINTENANCE MAIN ...
Страница 69: ...INDEX OF TOPICS ELECTRICAL SYSTEM ELE SYS ...
Страница 80: ...TABLE H 1 Clamp 2 Cable guide TABLE I 1 Cable grommet 2 Speed sensor Electrical system V7 II ABS ELE SYS 80 ...
Страница 132: ...INDEX OF TOPICS ENGINE FROM VEHICLE ENG VE ...
Страница 146: ...INDEX OF TOPICS ENGINE ENG ...
Страница 148: ...INDEX OF TOPICS POWER SUPPLY P SUPP ...
Страница 158: ...INDEX OF TOPICS SUSPENSIONS SUSP ...
Страница 173: ...V7 II ABS Suspensions SUSP 173 ...
Страница 179: ...INDEX OF TOPICS CHASSIS CHAS ...
Страница 206: ... Fit the crown Fit the plates and tighten the screws Insert the washer Insert the washer Chassis V7 II ABS CHAS 206 ...
Страница 220: ...INDEX OF TOPICS BRAKING SYSTEM BRAK SYS ...
Страница 253: ...INDEX OF TOPICS BODYWORK BODYW ...
Страница 270: ...INDEX OF TOPICS PRE DELIVERY PRE DE ...
Страница 278: ... Place the two seat saddle Pre delivery V7 II ABS PRE DE 278 ...