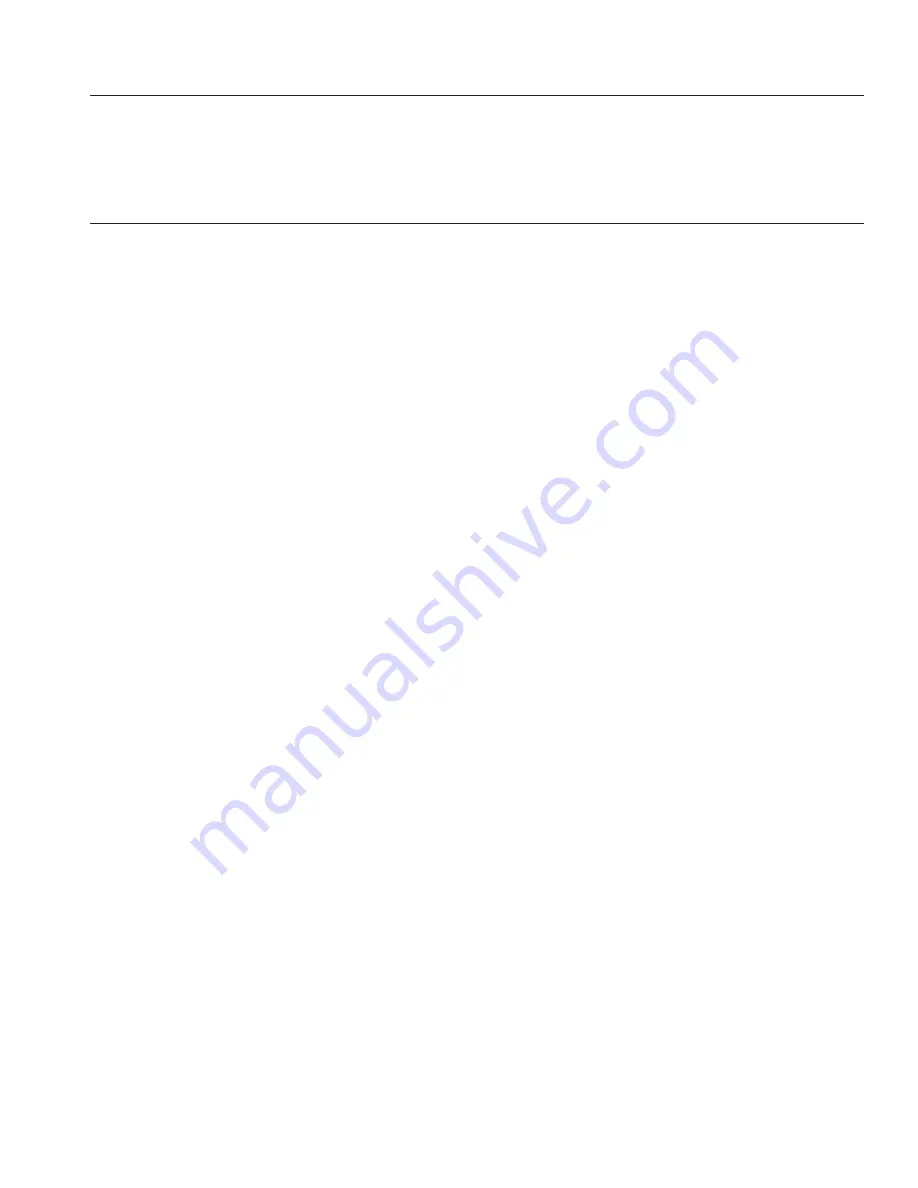
Part Number: 000016427 Rev 00 08/2020 65
PKU0155 Model
Troubleshooting an Ice Machine Will Not Run
n
Warning
High (line) voltage is applied to the control board (terminals #2 and #4) at all times.
Removing control board fuse or moving the toggle switch to OFF will not remove the
power supplied to the control board.
1. Verify primary voltage is supplied to ice machine and the fuse/circuit breaker is
closed.
2. Verify control board fuse is okay.
3. If the bin switch light functions, the fuse is okay.
4. Verify the bin switch functions properly. A defective bin switch can falsely indicate a
full bin of ice.
5. Verify ON/OFF/WASH toggle switch functions properly. A defective toggle switch may
keep the ice machine in the OFF mode.
6. Verify low DC voltage is properly grounded. Loose DC wire connections may
intermittently stop the ice machine.
7. Replace the control board.
8. Be sure Steps 1 – 5 were followed thoroughly. Intermittent problems are not usually
related to the control board.
Troubleshooting
Содержание PKM0335
Страница 2: ......
Страница 8: ...THIS PAGE INTENTIONALLY LEFT BLANK ...
Страница 64: ...64 Part Number 000016427 Rev 00 08 2020 Troubleshooting THIS PAGE INTENTIONALLY LEFT BLANK ...
Страница 98: ...98 Part Number 000016427 Rev 00 08 2020 Troubleshooting THIS PAGE INTENTIONALLY LEFT BLANK ...
Страница 130: ...130 Part Number 000016427 Rev 00 08 2020 Specifications THIS PAGE INTENTIONALLY LEFT BLANK ...
Страница 131: ......
Страница 132: ...Katom 305 Katom Drive Kodak Tennessee 37764 Part Number 000016427 Rev 00 08 2020 ...