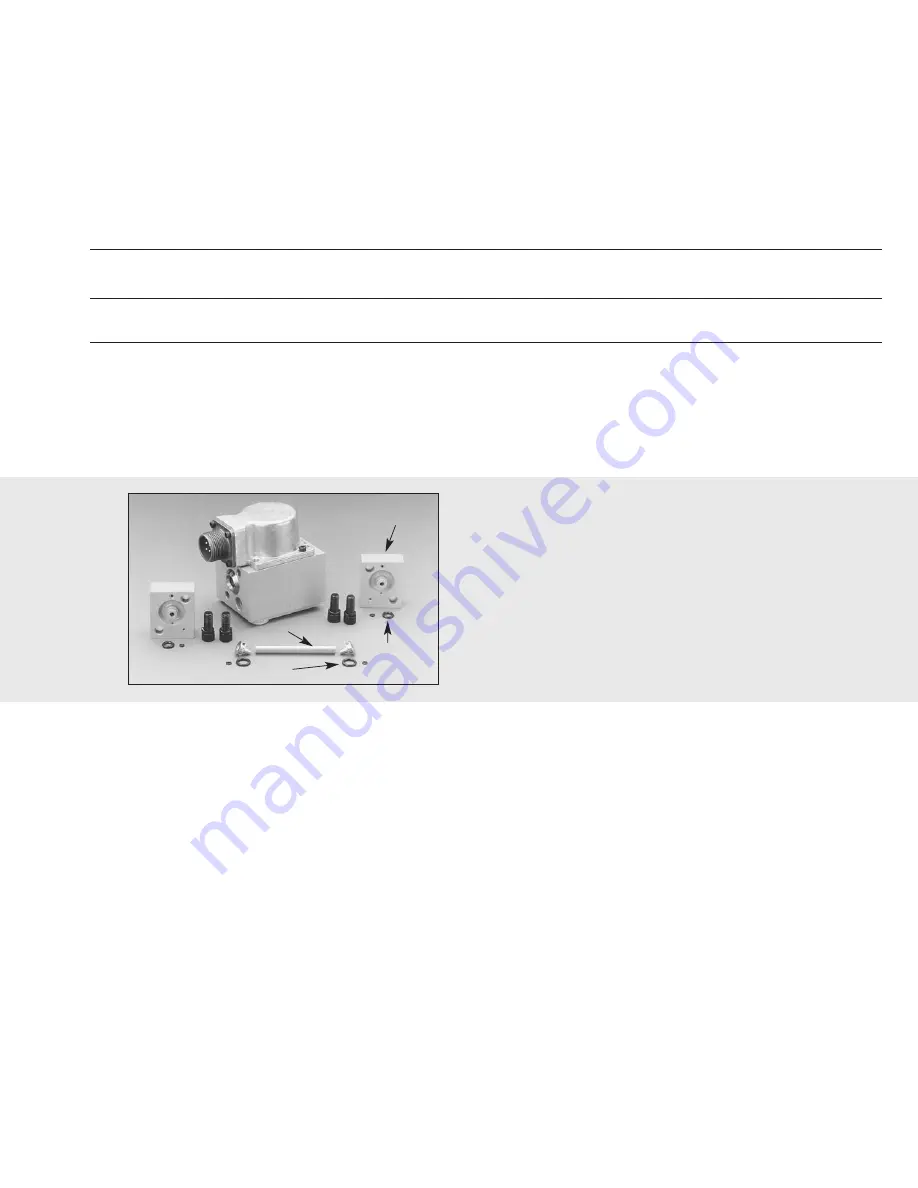
Potential Trouble
Servovalve does not follow input command
signal. (Actuator or components are
stationary or creeping slowly.)
High threshold. (Jerky, possible oscillatory
or “hunting” motion in closed loop system.)
Poor response. (Servovalve output lags
electrical command signal).
High Null Bias. (High input current required
to maintain hydraulic cylinder or motor
stationary.)
Probable Cause
Plugged inlet filter element.
Plugged filter element.
Partially plugged filter element.
1. Incorrect null adjustment
2. Partially plugged filter element.
Remedy
Replace filter element.
Replace filter element.
Replace filter element and check for dirty
hydraulic fluid in system.
1. Readjust null
2. Replace filter element and check for dirty
hydraulic fluid in system.
7.TROUBLESHOOTING CHART
The following troubleshooting chart list potential troubles encountered, probable causes, and remedies.
8. FILTER ASSEMBLY REPLACEMENT
a. Remove four socket head cap screws and lockwashers using a
3
/
16
inch
Allen wrench. Remove end caps. (See Figure 3).
b. Remove O-Rings from end caps.
c. Remove inlet orifice assembly from both sides of body.
Note: 2-56 screw threads into the filter plug and inlet orifice assembly.
Remove filter.The inlet orifice assemblies are matched to each other and
are therefore interchangeable.
Note:
These assemblies seat in body and cannot go through bore
during removal.
d. Remove O-Rings from inlet orifice assemblies.
e. Visually inspect orifice assemblies for damage or foreign material.
f.
Discard O-Rings and filters.
g. Install O-Rings on inlet orifices.
h. Install filter and inlet orifice assembly in body. Inlet orifice assembly pilots
into filter. Install the other inlet orifice assembly into other end of filter.
Inlet orifice assemblies are interchangeable.
i.
Install O-Rings on end caps.
j.
Install end caps on body and install four socket head cap screws and
lockwashers.Torque the screws to 85 inch-pounds.
9. FUNCTIONAL CHECKOUT AND CENTERING
a.
Install servovalve on hydraulic system or test fixture, but do not connect
electrical lead.
b.
Apply required system pressure to servovalve and visually examine for evi-
dence of external leakage. If leakage is present and cannot be rectified by
replacing O-Rings, remove the discrepant component and return for
repair or replacement.
Note:
If the system components are drifting or hardover, adjust
the mechanical null of the servovalve.
c.
Connect electrical lead to servovalve and check phasing in accordance
with system requirements.
10.AUTHORIZED REPAIR FACILITIES
If servovalve continues to malfunction after all recommended corrective
action procedures are performed, defective valve should be returned to Moog
for repair. Moog does not authorize any facilities other than Moog or Moog
subsidiaries to repair its servovalves. It is recommended you contact Moog at
(716) 652-2000 to locate your closest Moog repair facility. Repair by an
independent (unauthorized) repair house will result in voiding the Moog
warranty and could lead to performance degradation or safety problems.
End cap
End Cap O-Rings
Figure 3
Filter
Inlet Orifice O-Rings (two at each end cap)
Tools and Equipment
a. Blade screwdriver
b.
3
/
16
Allen wrench
c. No. 2-56 NC by 1
1
/
2
inch screw
d. Torque wrenches