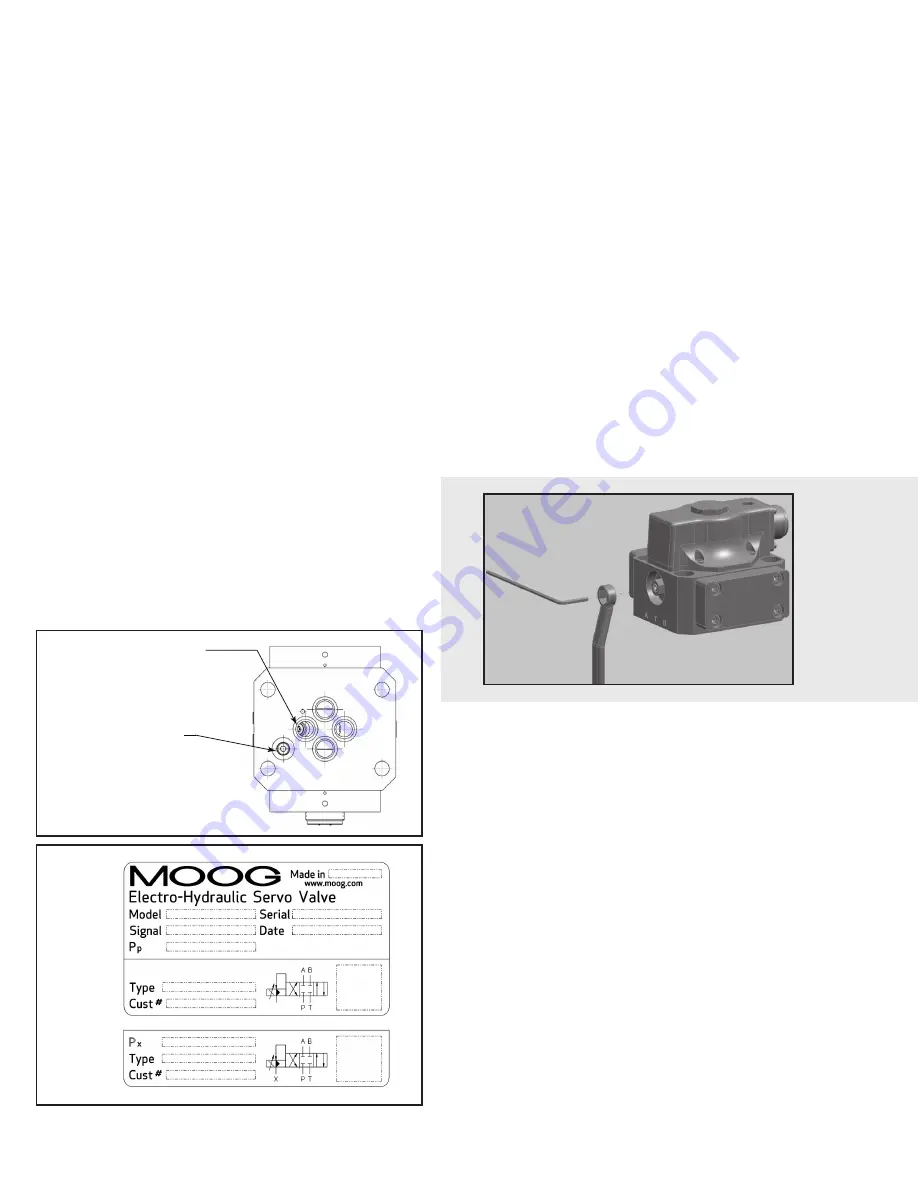
Relocate screw
and seal washer to
P port for external
(5th port) pilot
oil supply
Location of
screw and seal
washer for
standard internal
(4th port) pilot
oil supply
3. HYDRAULIC SYSTEM PREPARATION
To prolong servovalve operational life and to reduce hydraulic system
maintenance, it is recommended that the hydraulic fluid be kept at a cleanliness
level of ISO DIS 4406 Code 16/13 maximum, 14/11 recommended. The most
effective filtration scheme incorporates the use of a kidney loop or “off-line”
filtration as one of the major filtration components. The filter for the “off-line”
filtration scheme should be a B
3
≥
75 filter for maximum effectiveness.
Upon system startup and prior to mounting the servovalve, the entire
hydraulic system should be purged of built-in contaminating particles by an
adequate flushing. The servovalve should be replaced by a flushing manifold and
the hydraulic circuit powered up under conditions of fluid temperature and fluid
velocity, reasonably simulating normal operating conditions. New system filters are
installed during the flushing process whenever the pressure drop across the filter
element becomes excessive. The flushing processes should turn over the fluid in
the reservoir between fifty to one hundred times.
To maintain a clean hydraulic system, the filters must be replaced on
a periodic basis. It is best to monitor the pressure drop across the filter
assembly and replace the filter element when the pressure drop becomes
excessive. In addition to other filters that are installed in the hydraulic circuit,
it is recommended that a large capacity, low pressure ß
3
≥
75 filter be installed
in the return line. This filter will increase the interval between filter element
replacement and greatly reduce the system contamination level.
4. PILOT STAGE OIL SUPPLY AND NAMEPLATE
MODIFICATION
(applies to models G761-3001B through G761-3010B)
The Moog G761/761 series industrial servovalve can be configured for pilot
stage oil supply through the internal pressure “P” port, or from a separate supply
line through the “X” port. Standard configuration is internal pilot operation with
a screw and seal washer in the “X” port. This same screw and seal washer must
be relocated to the “P” port if an external pilot oil supply source is desired. Refer
to Figure 2 for screw and seal washer locations.
Upon valve installation, the nameplate must display the proper hydraulic
schematic and typecode (if applicable). The nameplate currently shows internal
(4th port) pilot hydraulic schematics and typecode. If a separate pilot supply will
be used, please attach the provided lower half label showing external (5th port)
information. See Figure 3.
5. INSTALLATION
The Moog G761/761 series industrial servovalve may be mounted in any
position, provided the servovalve pressure, control and return ports match their
respective manifold ports.
The mounting pattern and port locations of the servovalve are shown on
Figure 6. The servovalve should be mounted with 5/16-18 x 1.75 inch long, socket
head cap screws. Apply a light film of oil to the screw threads and torque to
96 inch pounds. Wire the mating connector for desired coil configuration and
polarity. Thread the connector to valve.
6. NULL ADJUSTMENT
It is often desirable to adjust the flow null of a servovalve independent
of other system parameters. The “mechanical null adjustment” on the Moog
G761/761 series servovalve allows at least ±20% adjustment of flow null.
The “mechanical null adjustor” is an eccentric bushing retainer pin located
above the “return” port designation on the valve body (see Figure 4) which, when
rotated, provides control of the bushing position. Mechanical feedback elements
position the spool relative to the valve body for a given input signal. Therefore, a
movement of the bushing relative to the body, changes the flow null.
Mechanical Adjustment Procedure
Using a
3
/
8
inch offset box wrench, loosen the self-locking fitting until the
null adjustor pin can be rotated. (This should usually be less than 1/2 turn).
DO NOT remove self-locking fitting. Insert a
3
/
32
inch Allen wrench in null
adjustor pin. Use the
3
/
32
Allen wrench to rotate the mechanical null adjustor
pin to obtain desired flow null. Torque self-locking fitting to 57 inch lbs.
Figure 3
Sample
Nameplate
7. GENERAL SERVICING RECOMMENDATIONS
a.
Disconnect the electrical lead to the servovalve.
b.
Relieve the hydraulic system of residual pressure.
c.
Remove the servovalve.
Figure 2
Figure 4
Mechanical Null Adjustment
Important:
Local regulations may require precise hydraulic labeling on components!