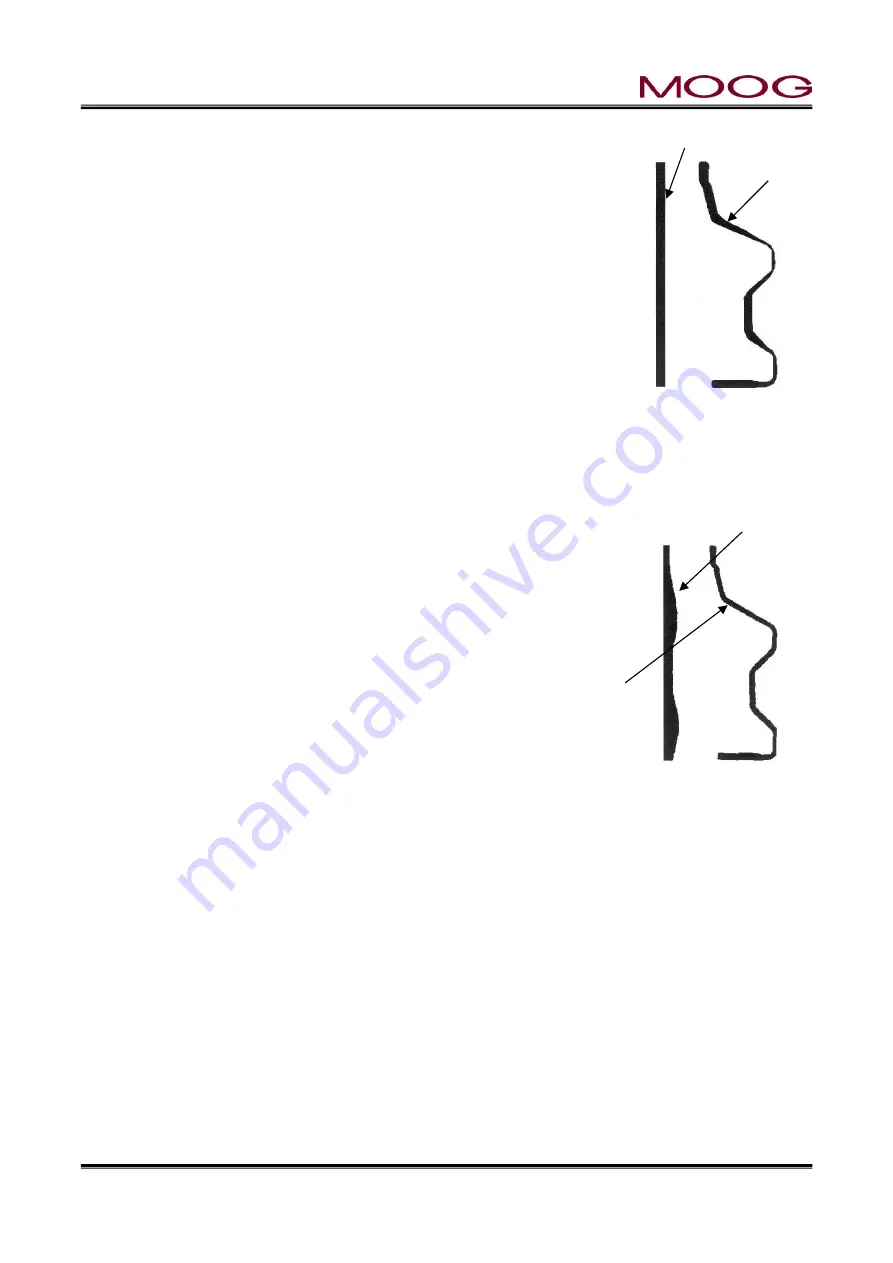
© MOOG 2019
This document is subject to MOOG INTELLECTUAL AND PROPRIETARY INFORMATION LEGEND . The details are on page II.
45
MRJ06301
2-2-5. PARISON PROGRAMMING BENEFITS
If the die mandrel gap is constant, the extruded parison wall thickness is con-
stant. When the parison is expanded by air pressure, it is stretched and made
thinner. The resulting container walls contain thick and thin portions depending
upon the amount of parison stretching occurring during the inflation of the con-
tainer.(Figure 2-2)
When this container is filled with a test fluid and dropped, it is likely to split in the
heavy wall areas upon impact, due to reduced material strength resulting from
uneven cooling stress. The entire container must be made thicker or more uni-
form to provide even cooling and improved strength.
Figure 2-2 Section of an Un-
programmed Parison and the
Resulting Container Walls
As a result the container walls will be heavier throughout the container, require
a long cooling time, material cost will increase and container production rates
will decrease.
If the parison container thickness can be programmed as it is extruded by var-
ying the die mandrel gap width, the resulting container will have constant thick-
ness walls.(Figure 2-3)
Figure 2-3 Section of a Pro-
grammed Parison and the
Resulting Container Walls
This container will pass the drop test with less material as there are no heavy spots.
On average, the wall thickness will be less requiring shorter time to cool the container.
The container will have constant thickness walls.
Programmed parison wall thickness control therefore results in higher container production rates using
less material per container and higher profits.
Container
Wall Profile
Container
Wall Profile
Programmed
parison