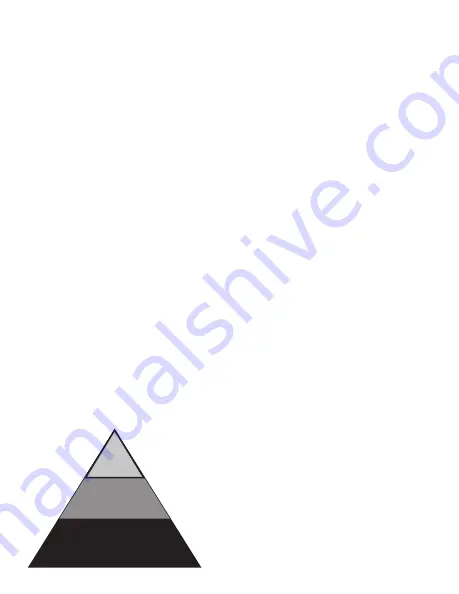
6
CRITICAL
ESSENTIAL
REDUNDANT
a loss of lubrication which induced the mechanical failure. If vibration
increased first, followed by increased temperature readings, then a
mechanical defect caused the lubrication failure.
6.3 Lube Oil Analysis (Ferrography)
Monitoring oil condition warns of an increase in foreign substances,
such as water, which can degrade the lubricating properties of the
oil and cause bearing failures. It also detects the presence of metallic
particles carried into the oil stream. These metallic particles are
analyzed to determine which part of the machine is wearing and
how fast. Lubrication analysis is the earliest warning of a developing
problem.
7.0 SELECTING MACHINERY AND MEASUREMENTS
Maintenance personnel have always made visual and hands‑on inspections
of their machinery on a periodic basis. Systematic data collection and
trending allows for recall and comparison of events over time but is not a
replacement for good maintenance practices. Collecting machinery data is
an aid to the maintenance professional, which is used in addition to good
maintenance practices.
7.1 Selecting and Classifying Machinery
Setting up an effective Predictive Maintenance Program requires a
careful study of the needs of the plant. It is necessary to know each
machine and its response to change. The following is an example of
machinery classification: