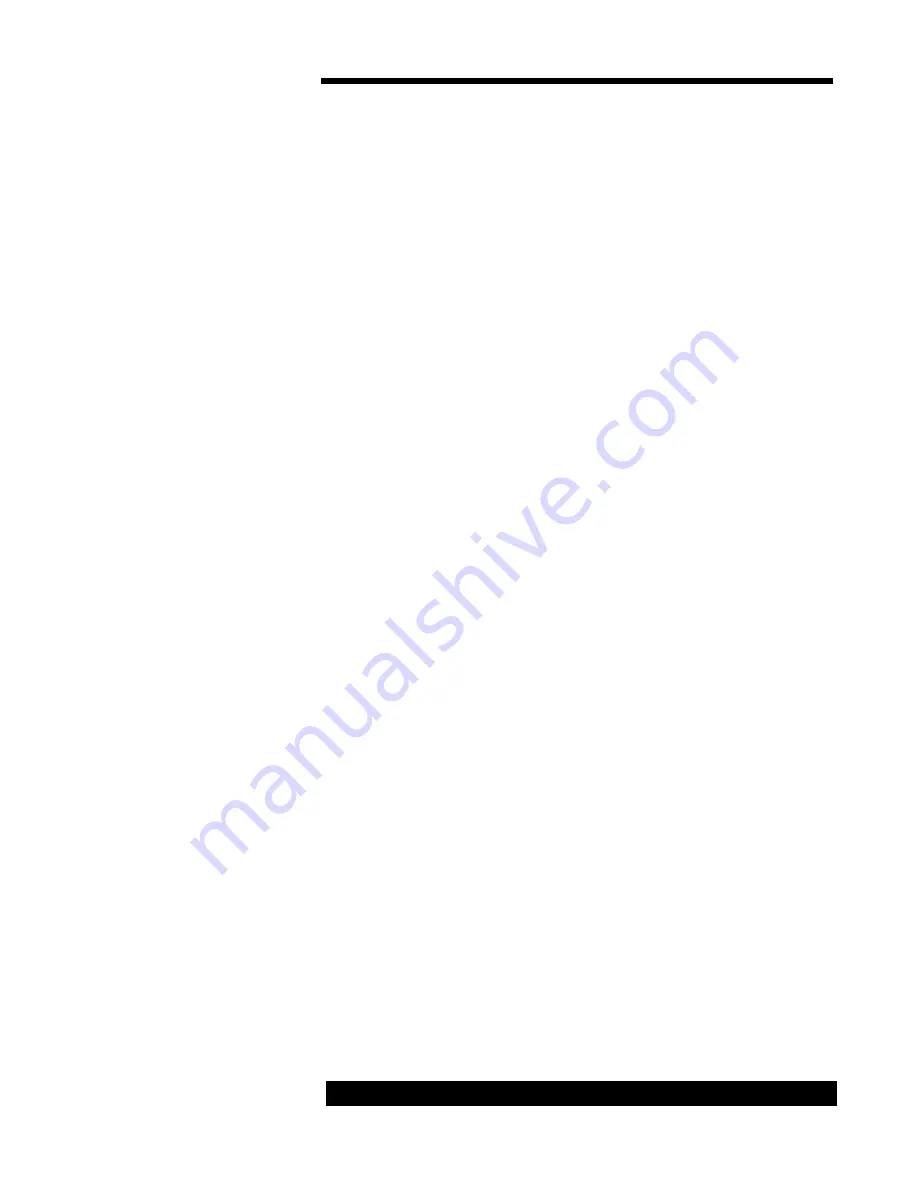
Vacuum Sentry
TM
safety Valve
9
Repair of Subassemblies
Piston / Diaphragm Subassembly
1.
Remove diaphragm (11) from piston by unscrewing
sleeve (3) from the piston using a spanner wrench, or
two 1/8” drill bits, in the 1/8 holes provided in the sleeve.
Inspect orifices (19) and (20) and clean if necessary. Be
careful not to enlarge the orifices, because performance
may suffer. Inspect the diaphragm (11) for holes, tears,
or accumulated contamination. Discard if damaged
2.
Inspect the dry bushings (2) pressed into sleeve (3). These
bushings are normally good for several hundred thousand
cycles, but they can be replaced when they have worn out.
A worn bushing can be identified by excessive exposure of
the sintered bronze matrix, which is not normally visible. A
modest amount of lead / TEFLON
R
flakes in and around the
bushing and pin is normal and does not constitute abnormal
wear of the bushing. If there is any doubt about the
condition of the bushings, they should be replaced.
Removal is readily accomplished by inserting a number 10
machine screw and pulling. There are two 1/4 inch long
bushings used in tandem. After removal of the old bushings
inspect the bore in the sleeve (3) for debris and burrs.
Clean as necessary. Press two new bushings into the bore,
one at a time, flush to the top of the sleeve.
3.
To reassemble, place diaphragm (11) on the piston with the
inner bead down and the outer bead up. See figure 3. A
small amount of vacuum compatible grease should be
smeared on the sleeve side of the diaphragm / sleeve
contact area to prevent puckering of the diaphragm during
tightening of the sleeve. Also, if the piston and sleeve have
been decreased prior to assembly, then a small amount of
vacuum compatible lubrication should be applied to the
male threads of the sleeve to prevent seizing of the sleeve
to the piston. DuPont KRYTOX
R
GPL 206 is acceptable.
Tighten the sleeve hand tight. Do not over tighten, this is
not a vacuum grade seal.
Nose Piece O-ring Replacement
1.
The nosepiece O-ring (5) should be removed only if a new
replacement is available. To remove the old O-ring, insert a
sharp pointed tool, such as a machinist’s scribe obliquely
into the ring. The sharp point must not pass through the
seal or the surface of the groove will be damaged. Lift the
seal out with the scribe. Use care not to scratch any of the
sealing surfaces.