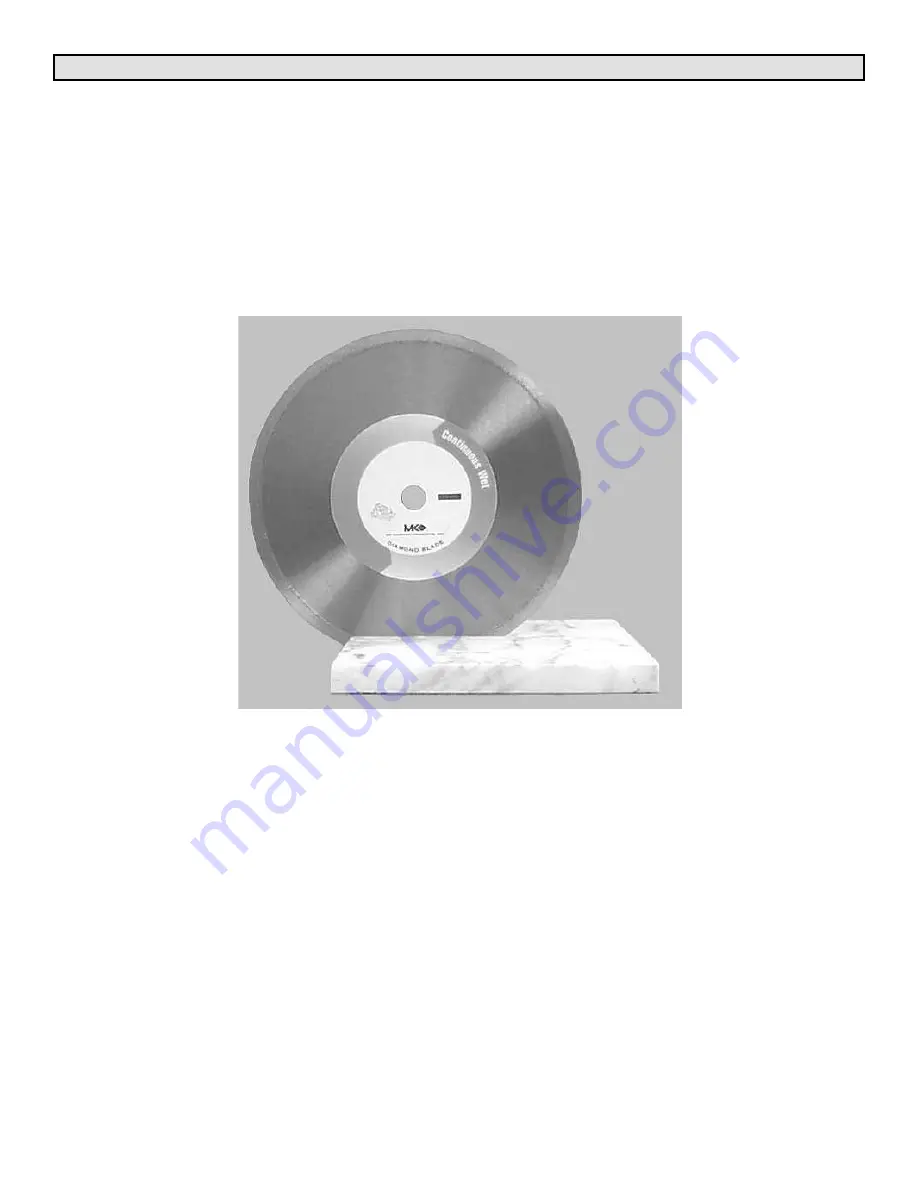
42
MK-370 EXP
Revision 12/03, Effective Date December 30, 2003
43
MK-370 EXP
Revision 12/03, Effective Date December 30, 2003
THEORY
THEORY OF DIAMOND BLADES
Diamond blades do not really cut; they grind the material through friction. Diamond crystals, often visible at the
leading edge and sides of the rim/segment, remove material by scratching out particles of hard, dense materials,
or by knocking out larger particles of loosely bonded abrasive material.
This process eventually cracks or fractures the diamond particle, breaking it down into smaller pieces. As a
result, a diamond blade for cutting soft, abrasive material must have a hard metal matrix composition to resist
this erosion long enough for the exposed diamonds to be properly utilized.
Conversely, a blade for cutting a hard, non-abrasive material must have a soft bond to ensure that it will erode
and expose the diamonds embedded in the matrix. These simple principles are the foundation of “controlled
bond erosion”.
Types of Cutting
There are two basic types of cutting-Dry or Wet. The choice of which type of blade to use depends on:
• The requirements of the job
• The machine/tool utilizing the diamond blade
• The preference of the operator
In the case of DRY cutting, the overwhelming popularity and quantity of hand-held saws and the flexible nature
of MK Diamond blades to professionally handle most ceramic, masonry, stone and concrete materials, make the
DRY cutting blade a very attractive tool. When using a DRY blade, the user must be aware of distinct operating
practices to ensure optimum performance. DRY cutting blades require sufficient airflow about the blade to
prevent overheating of the steel core. This is best accomplished by shallow, intermittent cuts of the material
with periods of “free-spinning” (for several seconds) between each cut, to maximize the cooling process.
For WET cutting applications, MK has the exact blade to compliment both the material to be cut and the wet
cutting machine to be used. During cutting operations, liberal amounts of water act as a coolant to support the
cutting effectiveness and longevity of the WET blade. Additionally, using water adds to the overall safety of
cutting operations by keeping the dust signature down.
Know All You Can About the Material You Wish to Cut