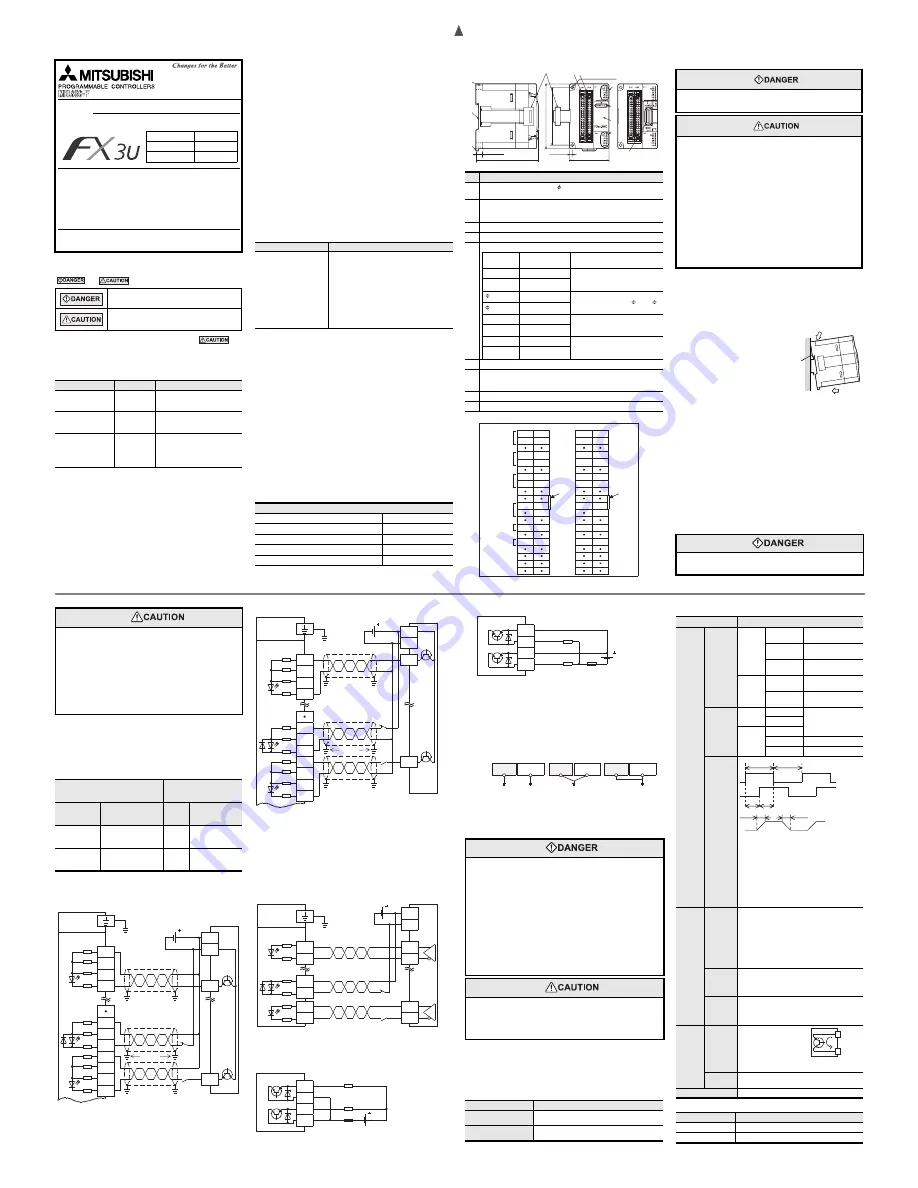
JY997D36701A
Safety Precaution
(Read these precautions before use.)
This manual classifies the safety precautions into two categories:
and
.
Depending on the circumstances, procedures indicated by
may
also cause severe injury.
It is important to follow all precautions for personal safety.
Associated Manuals
How to obtain manuals
For product manuals or documents, consult with the Mitsubishi Electric dealer
from who you purchased your product.
Certification of UL, cUL standards
The following product has UL and cUL certification.
UL, cUL File Number:E95239
Models:
MELSEC FX
3U
series manufactured
from December 1st, 2009
FX
3U
-2HC
Indicates that incorrect handling may cause hazardous
conditions, resulting in death or severe injury.
Indicates that incorrect handling may cause hazardous
conditions, resulting in medium or slight personal injury
or physical damage.
Manual name
Manual No.
Description
FX
3U
Series
User’s Manual
- Hardware Edition
JY997D16501
MODEL CODE:
09R516
Explains the FX
3U
Series PLC
s p e c i f i c a t i o n s f o r I / O , w i ri n g ,
installation, and maintenance.
FX
3UC
Series
User’s Manual
- Hardware Edition
JY997D28701
MODEL CODE:
09R519
Explains the FX
3UC
Series PLC
s p e c i f i c a t i o n s f o r I / O , w i ri n g ,
installation, and maintenance.
F X
3 G
/ F X
3 U
/ F X
3 U C
Series
Programming Manual
- Basic & Applied
Instruction Edition
JY997D16601
MODEL CODE:
09R517
D e s c r i b e s F X
3 G
/ F X
3 U
/ F X
3 U C
Series PLC programming for basic/
applied instructions and devices.
Compliance with EC directive (CE Marking)
This note does not guarantee that an entire mechanical module produced in
accordance with the contents of this note will comply with the following standards.
Compliance to EMC directive and LVD directive for the entire mechanical module
should be checked by the user / manufacturer. For more details please contact the
local Mitsubishi Electric sales site.
Requirement for Compliance with EMC directive
The following products have shown compliance through direct testing (of the identified
standards below) and design analysis (through the creation of a technical construction
file) to the European Directive for Electromagnetic Compatibility (2004/108/EC) when
used as directed by the appropriate documentation.
Attention
•
This product is designed for use in industrial applications.
•
Manufactured by:
Mitsubishi Electric Corporation
2-7-3 Marunouchi, Chiyoda-ku, Tokyo, 100-8310 Japan
•
Manufactured at:
Mitsubishi Electric Corporation Himeji Works
840 Chiyoda-machi, Himeji, Hyogo, 670-8677 Japan
•
Authorized Representative in the European Community:
Mitsubishi Electric Europe B.V.
Gothaer Str. 8, 40880 Ratingen, Germany
Type:
Programmable Controller (Open Type Equipment)
Models:
MELSEC FX
3U
series manufactured
from December 1st, 2009
FX
3U
-2HC
Caution for EC Directive
•
Installation in Enclosure
Programmable logic controllers are open-type devices that must be installed and
used within conductive control cabinets. Please use the programmable logic
controller while installed within a conductive shielded control cabinet. Please secure
the cabinet door to the control cabinet (for conduction). Installation within a control
cabinet greatly affects the safety of the system and aids in shielding noise from the
programmable logic controller.
1. Outline
1.1 Outline
The hardware high-speed counter block is a 2-channel high-speed counter. It is a
special function block for the FX
3U
and FX
3UC
series PLC.
1.2 Major Features of the FX
3U
-2HC
•
Differential-Line-Driver (AM26C31 or equivalent) and open collector output
encoders are available for the FX
3U
-2HC.
•
The FX
3U
-2HC has two outputs per channel. When the counter value coincides with
an output compare value, the appropriate output is set ON. The output transistors
are individually isolated to allow either sink or source connection methods.
•
Various counter modes, such as 1-phase or 2-phase, 16-bit or 32-bit modes, can be
selected using commands in the sequence program. Allow the FX
3U
-2HC unit to
run only after setting these mode parameters.
1.3 Incorporated Items
Verify that the following product and items are included in the package:
Standard
Remark
EN61131-2:2003
Programmable controllers
- Equipment requirements
and tests
Compliance with all relevant aspects of the standard.
EMI
• Radiated Emissions
• Conducted Emissions
EMS
• Radiated electromagnetic field
• Fast Transient burst
• Electrostatic discharge
• High-energy surge
• Voltage drops and interruptions
• Conducted RF
• Power frequency magnetic field
Included Items
FX
3U
-2HC
1 Unit
Special unit/block No. label
1 Sheet
Dust proof protection sheet
1 Sheet
Manuals [Japanese version]
1 manual
Manuals [English version] (This manual)
1 manual
1.4 External Dimensions, Part Names, and Terminal Layout
Weigh: 0.2kg (0.44lbs)
No.
Name
[1]
Direct mounting hole: 2 holes of
4.5 (0.18") (mounting screw: M4 screw)
Used when attaching FX
3U
-2HC directly.
[2]
Extension cable (PLC side)
Used to connect this special function block to the FX
3U
/FX
3UC
main unit or an
extension block.
[3]
CH1 connector
[4]
CH2 connector
[5]
Status LED (the upper side: CH1, the lower side: CH2)
POWER
(Green)
Power LED
ON when the 5V power supply is
normally supplied from the PLC.
UP (Red)
Up count LED
The respective LED is ON according
to up/down count direction of the
counter.
DOWN (Red)
Down count LED
A (Red)
A phase input LED
The respective LED is ON (flicker)
according to ON/OFF of A and B
input.
B (Red)
B phase input LED
DIS (Red)
DISABLE input LED T h e r e s p e c t i v e L E D i s O N / O F F
according to ON/OFF of PRESET and
DISABLE input.
PRE (Red)
PRESET input LED
YH1 (Red)
YH1 output LED
T h e r e s p e c t i v e L E D i s O N / O F F
according to status of YH1 and YH2
output.
YH2 (Red)
YH2 output LED
[6]
Top cover
[7]
Extension connector (Extension side)
Used to connect a FX
3U
extension block to the right of this special function
block. Remove top cover for connecting.
[8]
DIN rail mounting hook
[9]
DIN rail mounting groove (DIN rail: DIN46277, 35mm (1.38") width)
87(3.43")
9(0.36")
[1]
[5]
55(2.17")
[2]
[3] [4]
80(3.15")(mounting hole pitch)
[9]
[8]
90(3.55")
4(0.16")
Without top cover
[5]
[6]
[5]
2-Ø4.5 mounting holes
[7]
CH2
A24+
A5+
B24+
B5+
P24+
P5+
A12+
A-
B12+
B-
P12+
P-
XD24
YH1+
YH2+
XD5
COMD
YH1-
YH2-
Notch
CH1
A24+
A5+
B24+
B5+
P24+
P5+
A12+
A-
B12+
B-
P12+
P-
XD24
YH1+
YH2+
XD5
COMD
YH1-
YH2-
YH1 output
YH2 output
Notch
FX
3U
-2HC connector arrangement
Phase A
input
Phase B
input
PRESET
input
DISABLE
input
2. Installation, Connect to the PLC
2.1 Mounting
The product is mounted by the following method.
•
DIN rail mounting
•
Direct mounting (mounting screw: M4 screw)
For further information on installation arrangements, refer to the following manuals.
→
Refer to the FX
3U
Series User's Manual - Hardware Edition.
→
Refer to the FX
3UC
Series User's Manual - Hardware Edition.
2.1.1
DIN Rail Mounting
The product can be mounted on a DIN rail
(DIN46277, 35mm (1.38") width).
1) Fit the upper edge of the DIN rail mounting
groove (fig. A) onto the DIN rail.
2) Press the product against the DIN rail.
- An interval space of 1 to 2 mm (0.04" to
0.08") between each unit is necessary.
2.1.2
Direct Mounting (mounting screw: M4 screw)
The product can be installed directly with screws.
Refer to the External Dimensions (section 1.4) for the product’s mounting hole
pitch information.
An interval space between each unit of 1 to 2 mm (0.04" to 0.08") is necessary.
2.2 Connection to the PLC
A maximum of eight
*1
FX
3U
-2HC(s) are connectable with the main unit or the right
side of the powered extension unit/block. A unit number of No.0 to No.7 is
assigned based on the order in which special function units/blocks are attached to
the main unit.
For connection to an FX
3UC
Series PLC or FX
2NC
Series PLC extension block, an
FX
2NC
-CNV-IF or FX
3UC
-1PS-5V is required.
*1 Up to seven special function units/blocks in total can be connected to the
FX
3UC
-32MT-LT(-2) PLC. Unit numbers assigned to special function units/
blocks begins with No.1.
For further information on installation arrangements, refer to the following manuals.
→
Refer to the FX
3U
Series User's Manual - Hardware Edition.
→
Refer to the FX
3UC
Series User's Manual - Hardware Edition.
3. Wiring (Power supply and analog input)
INSTALLATION
PRECAUTIONS
•
Make sure to cut off all phases of the power supply externally before
attempting installation or wiring work.
Failure to do so may cause electric shock or damage to the product.
INSTALLATION
PRECAUTIONS
•
Use the product within the generic environment specifications described in PLC
main unit manual.
Never use the product in areas with excessive dust, oily smoke, conductive
dusts, corrosive gas (salt air,
Cl
2
, H
2
S, SO
2
, or NO
2
), flammable gas, vibration
or impacts, or expose it to high temperature, condensation, or rain and wind.
If the product is used in such conditions, electric shock, fire, malfunctions,
deterioration or damage may occur.
•
Do not touch the conductive parts of the product directly.
Doing so may cause device failures or malfunctions.
•
Install the product on a flat surface.
If the mounting surface is rough, undue force will be applied to the PC board,
thereby causing nonconformities.
•
When drilling screw holes or wiring, make sure cutting or wire debris does
not enter the ventilation slits.
Failure to do so may cause fire, equipment failures or malfunctions.
•
Be sure to remove the dust proof sheet from the PLC's ventilation port when
installation work is completed.
Failure to do so may cause fire, equipment failures or malfunctions.
•
Connect extension cables securely to their designated connectors.
Loose connections may cause malfunctions.
WIRING
PRECAUTIONS
•
Make sure to cut off all phases of the power supply externally before
attempting installation or wiring work.
Failure to do so may cause electric shock or damage to the product.
1)
2)
A
3.1 Connection to input/output connector
The input and output connectors conform to the MIL-C-83503.
→
For the input and output connectors pin assignment, refer to section 1.4.
1) Compliant connectors (commercially available connectors)
Use a 40-pin (1-key) socket connector conforming to MIL-C-83503.
Confirm in advance that the connectors do not interfere with other parts
including connector covers.
2) Connectors for user-made input/output cables (available from Mitsubishi)
Users should provide electric wires and a pressure bonding tool.
3.2 Wiring
Note:
Make sure to properly wire in accordance with the encoder output specifications.
Incorrect wiring may cause accidents or damage to the product.
3.2.1
NPN output encoders
WIRING
PRECAUTIONS
•
When drilling screw holes or wiring, make sure cutting or wire debris does
not enter the ventilation slits.
Failure to do so may cause fire, equipment failures or malfunctions.
•
Make sure to observe the following precautions in order to prevent any
damage to the machinery or accidents due to abnormal data written to the
PLC under the influence of noise:
1) Do not bundle the main circuit line together with or lay it close to the main
circuit, high-voltage line or load line. Otherwise, noise disturbance and/or
surge induction are likely to take place. As a guideline, lay the control line at
least 100mm (3.94") or more away from the main circuit or high-voltage lines.
2) Ground the shield wire or shield of the shielded cable at two points; on the
PLC and the device on other end. However, do not use common grounding
with heavy electrical systems.
Model name and composition of input/
output connector
Applicable electric wire
(UL-1061 are recommended)
and tool
Our model
name
Details of part
(made by DDK Ltd.)
Electric
wire
size
Pressure bonding
tool (made by DDK
Ltd.)
FX-I/O-CON2-S
for bulk wire
(2-piece set)
Housing:HU-400S2-001
Solderless contact:
HU-411S
AWG22
(0.3mm
2
)
357J-5538
FX-I/O-CON2-SA
for bulk wire
(2-piece set)
Housing:HU-400S2-001
Solderless contact:
HU-411SA
AWG20
(0.5mm
2
)
357J-13963
Encoder (NPN)
+24V
0V
24V DC
*1
*1
Phase
Z
Phase
A
Class D
PRESET
*3
DISABLE
A24+
A12+
A 5+
A -
3.3k
1.5k
0.2k
0.12k
XD24
XD 5
COMD
1.65k
0.47k
0.22k
*1
*1
Wiring of the B phase is the same as that of the A phase.
*1
*2
*2
P24+
P12+
P 5+
P -
3.3k
1.5k
0.2k
0.12k
Class D
Class D
Class D
Class D
Class D
FX
3U
FX
3UC
FX
3U
-2HC
*3
Shielded
Twisted-Pair
Shielded
Twisted-Pair
Shielded
Twisted-Pair
Drive power supply of the encoder.
Use either 24V DC, 12V DC, or 5V DC according to the encoder type.
When connecting the A phase, the B phase, and the Z phase to the
FX
3U
-2HC, connect to the power supply terminal.
When using 24V DC for PRESET or DISABLE signals, connect to the 24V
DC (P24+, XD24) terminal
*1.
This wiring is unnecessary when not using the PRESET function or the
DISABLE function.
*2.
*3.
3.2.2
PNP output encoders
3.2.3
Differential-Line-Driver output encoders
When applying the Differential-Line-Driver encoder (AM26C31 or equivalent) to the
FX
3U
-2HC, connect the encoder output with the 5V DC terminal as shown in the figure
below.
3.2.4
YH1, YH2 output wiring [Sink wiring]
Caution
A protection fuse should be inserted at the output.
Use a load power supply capacity that is at least 2 times larger than the total rated
fuse capacity.
Class D
Encoder (PNP)
+24V
0V
24V DC
*1
PRESET
*3
DISABLE
*3
Phase
A
*1
*1
*1
*3.
*2. Wiring of the B phase is the same as that of the A phase.
A24+
A12+
A 5+
A -
3.3k
1.5k
0.2k
0.12k
*2
*2
Class D
XD24
XD 5
COMD
1.65k
0.47k
0.22k
P24+
P12+
P 5+
P -
3.3k
1.5k
0.2k
0.12k
Class D
Class D
Class D
Class D
FX
3U
FX
3UC
FX
3U
-2HC
Shielded
Twisted-Pair
Shielded
Twisted-Pair
Shielded
Twisted-Pair
*1
Phase
Z
Drive power supply of the encoder.
Use either 24V DC, 12V DC, or 5V DC according to the encoder type.
When connecting the A phase, the B phase, and the Z phase to the
FX
3U
-2HC, connect to the power supply terminal.
When using 24V DC for PRESET or DISABLE signals, connect to the 24V
DC (P24+, XD24) terminal.
*1.
This wiring is unnecessary when not using the PRESET function or the
DISABLE function.
Class D
Encoder
A 5+
A -
0.2k
0.12k
XD 5
COMD
0.47k
0.22k
+5V
0V
5V DC
LA
LAR
P 5+
P -
0.2k
0.12k
PRESET
*2
Wiring of the B phase is the same as that of the A phase.
DISABLE
*2
LZR
LZ
*1
*1
FX
3U
FX
3UC
FX
3U
-2HC
This wiring is unnecessary when not using the PRESET function or the
DISABLE function.
*1.
*2.
YH1+
YH1-
YH2+
YH2-
Fuse
FX
3U
-2HC
Output load driving
power, 5 - 24V DC
3.2.5
YH1, YH2 output wiring [Source wiring]
Caution
A protection fuse should be inserted at the output.
Use a load power supply capacity that is at least 2 times larger than the total rated
fuse capacity.
3.3 Grounding
Grounding should be performed as stated below.
•
The grounding resistance should be 100
Ω
or less.
•
Independent grounding should be performed for best results.
When independent grounding is not performed, perform "shared grounding"
of the following figure.
→
For details, refer to the FX
3U
Series User's Manual - Hardware Edition.
→
For details, refer to the FX
3UC
Series User's Manual - Hardware Edition.
•
The grounding wire size should be AWG 22-20 (0.3-0.5 mm
2
).
•
The grounding point should be close to the PLC, and all grounding wires
should be as short as possible.
4. Specifications
4.1 General Specifications
The general specifications are equivalent to the PLC main unit.
(For general specifications, refer to the manual of the PLC main unit.)
Caution
When a dielectric withstand test of this product is performed, ground all terminals of
this product and the PLC unit.
4.2
Power Supply Specifications
DESIGN
PRECAUTIONS
•
Make sure to have the following safety circuits outside of the PLC to ensure safe
system operation even during external power supply problems or PLC failure.
Otherwise, malfunctions may cause serious accidents.
1) Most importantly, have the following: an emergency stop circuit, a protection
circuit, an interlock circuit for opposite movements (such as normal vs.
reverse rotation), and an interlock circuit (to prevent damage to the
equipment at the upper and lower positioning limits).
2) Note that when the PLC CPU detects an error, such as a watchdog timer
error, during self-diagnosis, all outputs are turned off. Also, when an error that
cannot be detected by the PLC CPU occurs in an input/output control block,
output control may be disabled.
External circuits and mechanisms should be designed to ensure safe
machinery operation in such a case.
3) Note that when an error occurs in a relay, triac or transistor output device, the
output could be held either on or off.
For output signals that may lead to serious accidents, external circuits and
mechanisms should be designed to ensure safe machinery operation in such
a case.
DESIGN
PRECAUTIONS
•
Do not bundle the control line together with or lay it close to the main circuit or
power line. As a guideline, lay the control line at least 100mm (3.94") or more
away from the main circuit or power line.
Noise may cause malfunctions.
•
Install module so that excessive force will not be applied to I/O connectors.
Failure to do so may result in wire damage/breakage or PLC failure.
Item
Specifications
Units driving power
5V DC, 245mA (Internal power supply from main unit
or extension power supply unit)
Allowable instantaneous
power failure time
Operation can be continued upon occurrence of
instantaneous power failure for 1 ms or less.
YH1+
YH1-
YH2+
YH2-
Fuse
FX
3U
-2HC
Output load
driving power,
5 - 24V DC
PLC
PLC
PLC
Another
equipment
Shared grounding
Good condition
Common grounding
Not allowed
Independent grounding
Best condition
Another
equipment
Another
equipment
4.3 Performance Specifications
4.4 Applicable PLC
The version number can be checked by reading the last three digits of device
D8001.
*1 An FX
2NC
-CNV-IF or FX
3UC
-1PS-5V is necessary to connect the FX
3U
-
2HC with the FX
3UC
PLC.
Item
Specification
Input
signal
Signal
level
(Selected
by terminal
connec-
tion)
Phase A,
Phase B,
PRESET
[A24+],[B24+],
[P24+]
24V DC
±
10%,
8mA or less
[A12+],[B12+],
[P12+]
12V DC
±
10%,
8mA or less
[A5+],[B5+],
[P5+]
3.0V to 5.5V DC,
12.5mA or less
DISABLE
[XD24]
10.8V to 26.4V DC,
15mA or less
[XD5]
5V DC
±
10%,
8mA or less
MAX.
frequency
1 - p h a s e
input
1 input
200kHz
2 input
2 - p h a s e
input
1 edge count
2 edge count
100kHz
4 edge count
50kHz
Pulse
shape
t1(ON/OFF pulse):
1.5
μ
s or more (at 200kHz)
t2(Phase difference between A and B):
0.75
μ
s or more (at 200kHz)
t3(Overlap time):
0.7
μ
s or more (at 200kHz)
t4(Rise/fall time):
0.75
μ
s or less
PRESET(Z phase) input signal width:
ON width 1.5
μ
s or more,
OFF width 30
μ
s or more
DISABLE (count prohibit) input signal width:
ON width 100
μ
s or more,
OFF width 100
μ
s or more
Count-
ing spec-
ification
Format
Automatic UP/DOWN
However, when on 1-phase 1-input mode, UP/
DOWN is determined by the following.
•
Hardware UP/DOWN:
Up/down count is decided by OFF/ON of the A-
phase input terminal.
•
Software UP/DOWN:
Up/down count is decided by the current value
(K0/K1) of BFM #1, #41.
Range
When 32-bit is specified:
-2,147,483,648 to +2,147,483,647
When 16-bit is specified: 0 to 65,535
(upper limit is set up by BFM #3, #2, #43, #42.)
Compari-
son Type
When the present value and the comparison set
value of the counter are equal, the comparison
output is set (ON) within 30
μ
s and is cleared (OFF)
within 100
μ
s by the reset command.
Output
signal
Types of
outputs
YH1+: transistor output for
YH1 output
YH1-: transistor output for
YH1 output
YH2+: transistor output for
YH2 output
YH2-: transistor output for YH2 output
Output
capacity
5V ~ 24V DC, 0.5A
I/O occupation
8 points (can be either inputs or outputs)
Model name
Applicability
FX
3U
Series PLC
Ver. 2.20 and later
FX
3UC
Series PLC
*1
Ver. 2.20 and later
t4
t4
t1
t1
t2
t3
YH1+,
YH2+
YH1-,
YH2-
FX
3U
-2HC
USER’S MANUAL
This manual describes the part names, dimensions, mounting, wiring, and
specifications of the product. Before use, read this manual and the manuals of
all relevant products fully to acquire proficiency in handling and operating the
product. Make sure to learn all the product information, safety information, and
precautions.
Store this manual in a safe place so that it can be taken out and read whenever
necessary. Always forward it to the end user.
Registration:
The company and product names described in this manual are registered
trademarks or the trademarks of their respective companies.
Effective December 2009
Specifications are subject to change without notice.
©
2009 Mitsubishi Electric Corporation
Manual Number
JY997D36701
Revision
A
Date
December 2009