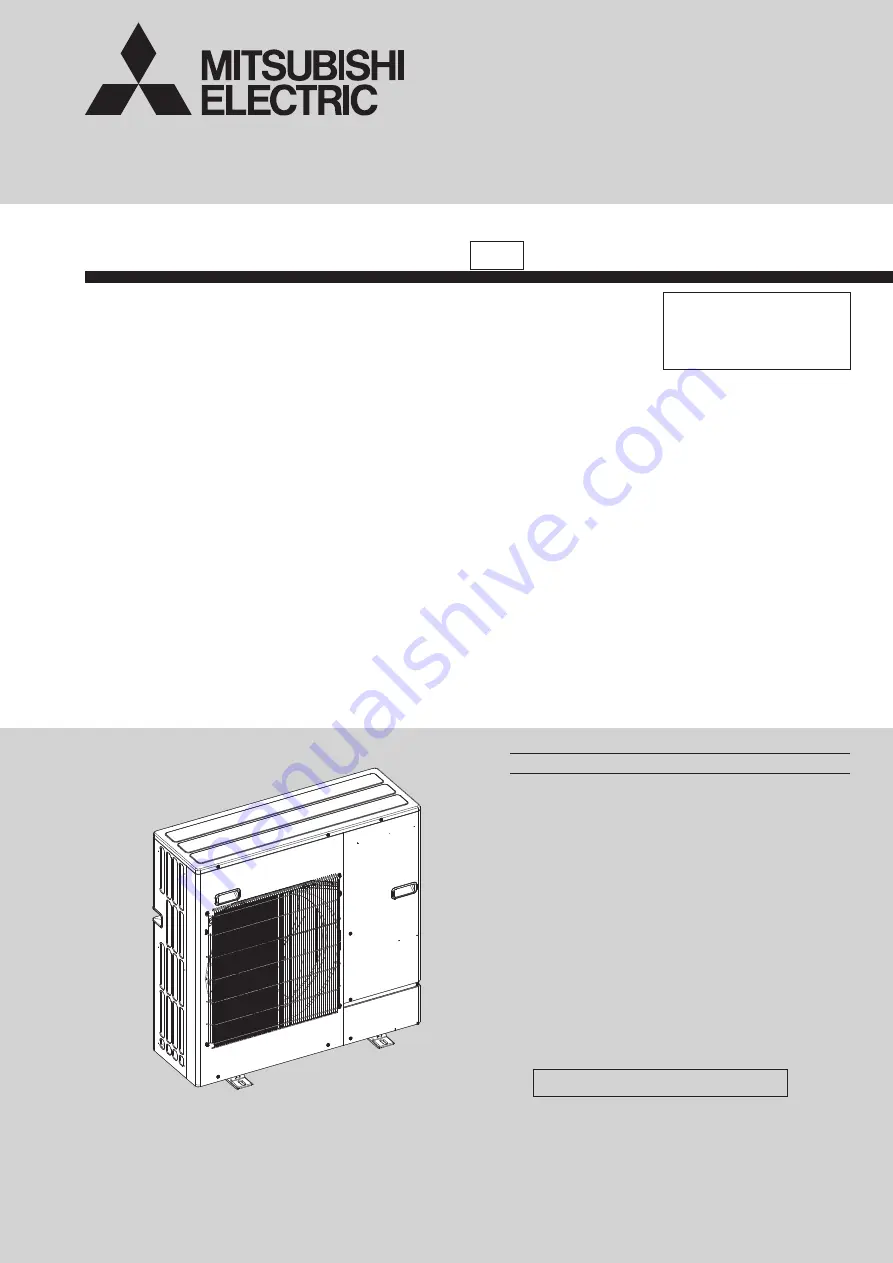
SERVICE MANUAL
No. OCH727
R32
March 2020
PARTS CATALOG (OCB727)
<Outdoor unit>
[Model Name]
PUZ-WM50VHA
PUZ-WM60VAA
PUZ-WM85VAA
PUZ-WM85YAA
PUZ-WM112VAA
PUZ-WM112YAA
Salt proof model
PUZ-WM50VHA-BS
PUZ-WM60VAA-BS
PUZ-WM85VAA-BS
PUZ-WM85YAA-BS
PUZ-WM112VAA-BS
PUZ-WM112YAA-BS
CONTENTS
1. REFERENCE MANUAL ································ 2
2. SAFETY PRECAUTION ······························· 3
3. SPECIFICATIONS ······································ 10
4. DATA ··························································· 12
5. OUTLINES AND DIMENSIONS·················· 13
6. WIRING DIAGRAM ····································· 15
7. WIRING SPECIFICATIONS ························ 18
8. REFRIGERANT SYSTEM DIAGRAM ········ 19
9. TROUBLESHOOTING ································ 22
10. MONITORING THE OPERATION DATA BY THE REMOTE CONTROLLER ···· 60
11. DISASSEMBLY PROCEDURE ··················· 66
Note:
• This manual describes
service data of the outdoor
units only.
AIR TO WATER HEAT PUMP UNITS
[Service Ref.]
PUZ-WM50VHA.UK
PUZ-WM60VAA.UK
PUZ-WM85VAA.UK
PUZ-WM85YAA.UK
PUZ-WM112VAA.UK
PUZ-WM112YAA.UK
PUZ-WM50VHA-BS.UK
PUZ-WM60VAA-BS.UK
PUZ-WM85VAA-BS.UK
PUZ-WM85YAA-BS.UK
PUZ-WM112VAA-BS.UK
PUZ-WM112YAA-BS.UK
PUZ-WM50VHA.UK
Содержание PUZ-WM112VAA
Страница 15: ...15 OCH727 6 WIRING DIAGRAM PUZ WM50VHA UK PUZ WM50VHA BS UK ...
Страница 16: ...16 OCH727 PUZ WM60VAA UK PUZ WM85VAA UK PUZ WM112VAA UK PUZ WM60VAA BS UK PUZ WM85VAA BS UK PUZ WM112VAA BS UK ...
Страница 17: ...17 OCH727 PUZ WM85YAA UK PUZ WM112YAA UK PUZ WM85YAA BS UK PUZ WM112YAA BS UK ...