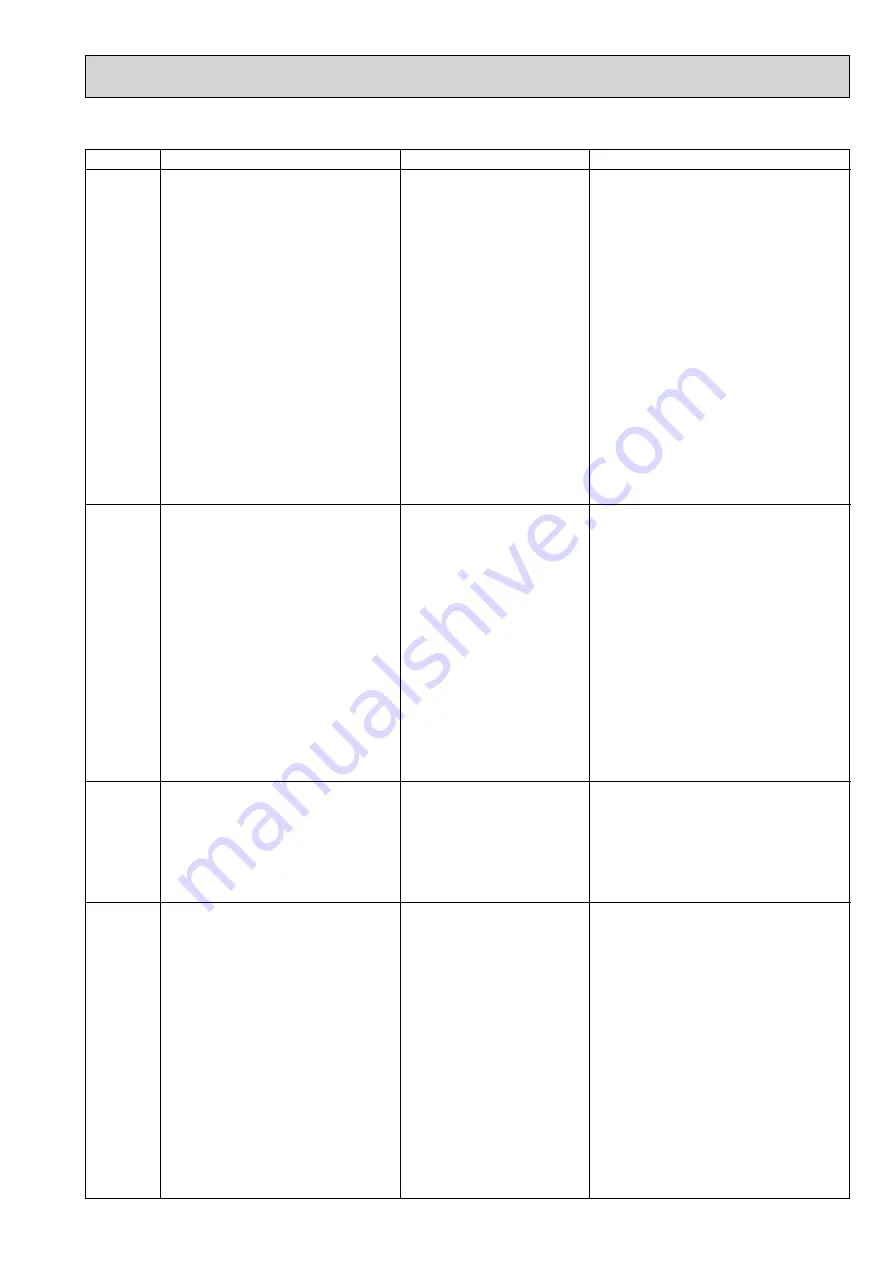
23
9-3. SELF-DIAGNOSIS ACTION TABLE
Note: Refer to the manual of outdoor unit for the details of display
such as F, U, and other E.
Error Code
Abnormal point and detection method
Cause
Countermeasure
P1
P2
Room temperature thermistor (TH1)
1
The unit is in 3-minute resume
prevention mode if short/open of
thermistor is detected. Abnormal if the
unit does not reset normally after 3
minutes. (The unit returns to normal
operation, if it has been reset normally.)
2
Constantly detected during cooling,
drying, and heating operation.
Short:
-90
:
or more
Open:
-40
:
or less
1
Defective thermistor
characteristics
2
Contact failure of connector
(CN20) on the indoor controller
board (Insert failure)
3
Breaking of wire or contact
failure of thermistor wiring
4
Defective indoor controller
board
1
–
3
Check resistance value of thermistor.
0
:
15.0k
"
10
:
9.6k
"
20
:
6.3k
"
30
:
4.3k
"
40
:
3.0k
"
If you put force on (draw or bend) the lead wire
while measuring resistance value of thermistor,
breaking of wire or contact failure can be
detected.
2
Check contact failure of connector (CN20)
on the indoor controller board. Refer to 9-7.
Turn the power on again and check restart
after inserting connector again.
4
Check room temperature display on remote
controller.
Replace indoor controller board if there
is abnormal difference with actual room
temperature.
Turn the power off, and on again to operate
after check.
Pipe temperature thermistor/Liquid
(TH2)
1
The unit is in 3-minute resume
prevention mode if short/open of
thermistor is detected. Abnormal if the
unit does not reset normally after 3
minutes. (The unit returns to normal
operation, if it has been reset normally.)
2
Constantly detected during cooling,
drying, and heating (except defrosting)
operation
Short:
90
:
or more
Open:
-40
:
or less
1
Defective thermistor
characteristics
2
Contact failure of connector
(CN44) on the indoor controller
board (Insert failure)
3
Breaking of wire or contact
failure of thermistor wiring
4
Defective refrigerant circuit is
causing thermistor temperature
of 90
:
or more or -40
:
or
less.
5
Defective indoor controller
board
1
–
3
Check resistance value of thermistor.
For characteristics, refer to (P1) above.
2
Check contact failure of connector (CN44)
on the indoor controller board. Refer to 9-7.
Turn the power on and check restart after
inserting connector again.
4
Check pipe <liquid> temperature with remote
controller in test run mode. If pipe <liquid>
temperature is extremely low (in cooling
mode) or high (in heating mode), refrigerant
circuit may have defective.
5
Check pipe <liquid> temperature with
remote controller in test run mode. If there is
extremely difference with actual pipe <liquid>
temperature, replace indoor controller board.
Turn the power off, and on again to operate
after check.
P4
Contact failure of drain float switch
(CN4F)
• Extract when the connector of drain float
switch is disconnected.
(
3
and
4
of connector CN4F is not
short-circuited.)
• Constantly detected during operation
1
Contact failure of connector
(Insert
failure)
2
Defective indoor controller
board
1
Check contact failure of float switch connector.
Turn the power on again and check after
inserting connector again.
2
Operate with connector (CN4F) short-
circuited.
Replace indoor controller board if abnormality
reappears.
P5
Drain over flow protection operation
1
Suspensive abnormality, if drain float
switch is detected to be underwater for
1 minute and 30 seconds continuously
with drain pump on.
Compressor and indoor fan will be
turned off.
2
Drain pump is abnormal if the condition
above is detected during suspensive
abnormality.
3
Constantly detected during drain pump
operation
1
Malfunction of drain pump
2
Defective drain
Clogged drain pump
Clogged drain pipe
3
Defective drain float switch
Jamming of the drain float
switch or malfunction of moving
parts causing the drain float
switch to be detected under
water (Switch On)
4
Defective indoor-controller
board
1
Check if drain pump works.
2
Check drain function.
3
Remove drain float switch connector CN4F
and check if it is short (Switch On) with the
moving part of float switch UP, or OPEN with
the moving part of float switch down.
Replace float switch if it is short with the
moving part of float switch down.
4
Replace indoor controller board if it is short-
circuited between
3
-
4
of the drain float
switch connector CN4F and abnormality
reappears.
It is not abnormal if there is no problem about
the above-mentioned
Turn the power off, and on again to operate
after check.
OCH535